Predictive maintenance (PdM) is maintenance that monitors the performance and condition of equipment during normal operation to reduce the likelihood of failures. Also known as condition-based maintenance, predictive maintenance has been utilized in the industrial world since the 1990s.
Yet, in reality, predictive maintenance is much older, although its history is not formally documented. According to Control Engineering, “The start of predictive maintenance (PdM) may have been when a mechanic first put his ear to the handle of a screwdriver, touched the other end to a machine, and pronounced that it sounded like a bearing was going bad.”
The goal of predictive maintenance is the ability to first predict when equipment failure could occur (based on certain factors), followed by preventing the failure through regularly scheduled and corrective maintenance.
Predictive maintenance cannot exist without condition monitoring, which is defined as the continuous monitoring of machines during process conditions to ensure the optimal use of machines. There are three facets of condition monitoring: online, periodic and remote. Online condition monitoring is defined as the continuous monitoring of machines or production processes, with data collected on critical speeds and changing spindle positions (“Condition Monitoring of Rotating Machines,” Istec International).
Periodic condition monitoring, which is achieved through vibration analysis, “gives insight into changing vibration behavior of installations” with a trend analysis (“Condition Monitoring of Rotating Machines,” Istec International). Lastly, remote condition monitoring, as its name suggests, allows equipment to be monitored from a remote location, with data transmitted for analysis.
Before establishing a predictive maintenance program, an organization must take several steps, which include:
-
Analyzing the need and equipment history
-
Reviewing any and all available records on downtime, equipment defects, losses (yield and energy), potential regulation fines and workplace safety
-
Establishing definitions and concepts as well as building a case for PdM
-
Educating major stakeholders and getting buy-in
-
Completing an equipment inventory and appraising the current equipment conditions
-
Selecting equipment for the program’s initial implementation
-
Developing system details based on individual systems and/or components
-
Evaluating any existing preventive or predictive maintenance
-
Deciding which systems to include and what to inspect for
-
Defining the program’s criticality and establishing PdM frequency and schedule type
-
Evaluating the anticipated resources and assigning personnel roles and responsibilities
-
Organizing the program and integrating it into the scheduling system
-
Educating and obtaining buy-in from operations and maintenance
-
Upgrading equipment and conducting training
-
Creating a computerized maintenance management systems (CMMS)
Around 65 percent of maintenance personnel surveyed in Reliable Plant's 2019 Predictive Maintenance Survey said they use predictive maintenance. When implemented and executed, predictive maintenance is a cornerstone of a successful maintenance program.
The Difference Between Predictive Maintenance and Preventive Maintenance
While many maintenance programs use a bit of both, there are several differences between predictive maintenance and preventive maintenance. Preventive maintenance has involved inspecting and performing maintenance on machinery, regardless of whether the equipment was in need of maintenance. This maintenance schedule is based on either a usage or time trigger. For example, a heating unit is serviced every year before winter, or a car requires scheduled maintenance every 5,000 miles.
Also, preventive maintenance does not demand the condition monitoring component that predictive maintenance does. By not requiring condition monitoring, a preventive maintenance program does not involve as much capital investment in technology and training. Lastly, many preventive maintenance programs need manual data-gathering and analyzing.
While preventive maintenance is determined by using the average life cycle of an asset, predictive maintenance is identified based on preset and predetermined conditions of specific pieces of equipment, utilizing different technologies. Predictive maintenance also requires more investments in people, training and equipment than preventive maintenance, but the time savings and cost savings will be greater in the long run.
Advantages and Disadvantages of Predictive Maintenance
As mentioned, the advantages of predictive maintenance are tremendous from a cost-savings perspective and include minimizing planned downtime, maximizing equipment lifespan, optimizing employee productivity and increasing revenue (Immerman, “The Impact of Predictive Maintenance on Manufacturing”). Another advantage of predictive maintenance is its ability to transform both a maintenance team and an organization, as implementing PdM allows asset managers to improve outcomes and better balance priorities such as profitability and reliability.
One of the main disadvantages of predictive maintenance is the amount of time it takes to assess and implement a PdM schedule. With predictive maintenance being a complex initiative, plant personnel must be trained on how to not only use the equipment but also how to interpret the analytics (or data).
While many organizations choose to train existing employees on predictive maintenance, there are condition-monitoring contractors who specialize in performing the required labor and analyzing the results for a facility. In addition to the training costs, predictive maintenance involves an investment in maintenance tools and systems. This cost has decreased over time with the introduction of cloud-based technology.
Predictive Maintenance vs. Inspection for Defects
For some time, a considerable amount of confusion has existed over the appropriate way to inspect for the presence of a given failure mode. Should I perform some type of sensory inspection? Should I perform some type of quantitative inspection? Should I apply one or more condition-monitoring technologies? Should I apply some combination of these techniques to maximize the conditional probability of finding the defect?
How do I identify the presence of a key defect in such a way as to maximize the amount of time my planning department has to develop the job procedures, create work orders, order the parts, and schedule and complete the work before the conditional probability of failure becomes too high? An explanation of the types of inspections and how they complement one another goes a long way toward clarifying which ones are most appropriate.
Types of Defect Inspection Techniques
Sensory inspections have long been considered the backbone of any good inspection program and maintenance work. It was believed that sending someone around often enough to inspect for problems with machinery would result in identifying defects in plenty of time to mitigate unplanned downtime. The inspector would use sight, sound and touch to determine if anything had changed since the last inspection. Any change would be recorded, reported and investigated by a craftsperson on the next scheduled outage.
While there is a tremendous amount of benefit to sending someone around to perform inspections, there are so many holes in this strategy that it should never be considered the backbone of the inspection program. Sensory inspections typically only identify the most obvious and drastic of problems. It is all but impossible for a sensory inspection to identify early, internal defects in machines.
Enhanced Sensory Inspections
Enhanced sensory inspections fill that gray zone. They are both a sensory inspection and a quantitative measurement with condition-monitoring characteristics. These inspections use instruments like spot radiometers, strobe lights, handheld vibration pens and simple ultrasonic meters to detect defects further up the P-F curve. While these tools multiply the power of the human senses, they have their limit. These simple tools do allow for different failure modes to be detected, but they shouldn't replace a comprehensive condition-monitoring program.
Quantitative Inspections
Quantitative inspections can provide useful information when it comes to generating data for trending and determining the characteristic life of a failure mode. Quantitative inspections need someone to measure something. Very common quantitative inspections include measuring the temperature of a seal on a pump or measuring the backplate clearance on a pump impeller. These measurements provide data to the planner and engineer and help determine the need for further maintenance action.
When designed properly, a quantitative inspection procedure details limits and typically expected measurements. Any inspection that requires someone to measure something should have the minimum, maximum and typical values, with conditional tasks defined for when the limits are exceeded. But a quantitative inspection performed at the proper inspection frequency rarely will have a measurement that exceeds the limits.
Predictive Maintenance as a Defect Inspection Technique
Condition monitoring, also known as predictive maintenance (PdM), is the application of condition-based monitoring technologies, statistical process control or equipment performance for early detection and elimination of equipment defects that could lead to unplanned downtime or unnecessary expenditures.
And generally speaking, you must conduct this while the equipment is in normal operation, with little to no process interruption. The purpose of these tools (vibration analysis, infrared thermography, motor circuit analysis, etc.) is to find defects not found through previously available inspections methods, while the machine is in normal operation.
Taking advantage of the available technology lets you assess the condition of parts and the presence of defects heretofore impossible to detect. An example of the advantage these tools have in the area of quantitative inspections or sensory inspections is the use of vibration analysis to determine the presence of a defect on a rolling element bearing.
Previously, mechanics and millwrights relied on "lift checks" to determine the amount of clearance in a bearing. Unfortunately, this technique is only valid for bearing defects that resulted in the removal of material from the raceways of the bearing; this bearing would be pretty bad off to have thousandths of inches of play in it.
Sub-surface fatigue is easily seen with vibration analysis and at this point in the failure propagation has resulted in no removal of material from the raceways. This is the most common example of the advantages of predictive maintenance technologies.
There are different types of defect inspection techniques that can be brought to bear on a machine, and each has its advantages and disadvantages. Yet, these techniques aren't exact replacements for each other. Each determines the presence of the defect at different places along the P-F curve and, as a result, each gives the planning function different amounts of time to respond to the defect.
A failure modes, effects and criticality analysis (FMECA) can help you determine which inspection techniques should be applied, how often and with what degree of redundancy. Remember, the trick is to balance risk with rigor. How much risk you are willing to take with a given failure mode coupled with how much you are willing to pay for the inspection determines the appropriate strategy.
Predictive Maintenance Technologies
As the name suggests, the goal of predictive maintenance is to predict when maintenance is needed. While there is no Magic 8-Ball, there are several condition-monitoring devices and techniques that can be employed for effectively predicting failure, as well as providing advanced warning for maintenance on the horizon.
Infrared Thermography
Known as a nondestructive or nonintrusive testing technology, infrared (IR) thermography in predictive maintenance is widely used. With IR cameras, personnel are able to detect high temperatures (aka, hotspots) in equipment. Worn components, including malfunctioning electrical circuits, typically emit heat that will display as a hotspot on a thermal image (“Predictive Maintenance,” Lean Manufacturing Tools).
By quickly identifying hotspots, infrared inspections can pinpoint problems and help avoid costly repairs and downtime. Infrared technology is considered “one of the most versatile predictive maintenance technologies available … used to study everything from individual components of machinery to plant systems, roofs and even entire buildings,” (Control Engineering). More uses for infrared technology include detecting thermal anomalies and problems with process systems relying on heat retention and/or transfer.
Acoustic Monitoring
With acoustic technologies, personnel can detect gas, liquid or vacuum leaks in equipment on a sonic or ultrasonic level. Considered less expensive than ultrasonic technology, sonic technology is useful on mechanical equipment but limited in its use. Ultrasonic technology has more applications and is more reliable in detecting mechanical issues.
It allows a technician to “hear friction and stress in rotating machinery, which can predict deterioration earlier than conventional techniques” (“Predictive Maintenance,” Wikipedia) by using instrumentation to convert sounds in the 20- to 100-kilohertz range into “auditory or visual signals that can be heard/seen by a technician. These high frequencies are the exact frequencies generated by worn and underlubricated bearings, faulty electrical equipment, leaky valves, etc.” (Wright, “How to Leverage Multiple Predictive Maintenance Technologies”).
While both sonic and ultrasonic testing can be expensive, there is another form of acoustic monitoring that is quite affordable: a technician’s ears. “Something as simple as detecting an oil leak or a gearbox that sounds weird could and often does lead to the prevention of a catastrophic failure, avoiding tens of thousands of dollars in losses,” (Wright, “How to Leverage Multiple Predictive Maintenance Technologies”).
Vibration Analysis
Employed primarily for high-speed rotating equipment, vibration analysis allows a technician to monitor a machine’s vibrations by using a handheld analyzer or real-time sensors built into the equipment. A machine operating in peak condition exhibits a particular vibration pattern. When components like bearings and shafts begin to wear and fail, the machine will begin to generate a different vibration pattern. By proactively monitoring the equipment, a trained technician can compare the readings against known failure modes to determine where problems are occurring.
Among the issues that can be detected with vibration analysis include misalignment, bent shafts, unbalanced components, loose mechanical components and motor problems.
Ensuring technicians are trained will be vital, as it can be difficult to predict machine failure utilizing vibration analysis. Many organizations offer in-depth training to prepare individuals for certification as vibration analysts. The only downside to using vibration analysis is the cost associated in implementing it with a PdM program.
Oil Analysis
Oil analysis is an effective tool in predictive maintenance. It enables a technician to check the oil’s condition and determine if other particles and contaminants are present. Some oil analysis tests can reveal the viscosity, presence of water or wear metals, particle counts, and the acid number or base number.
One of the benefits of using oil analysis is that the initial test(s) will set a baseline for a new machine. When done properly, oil analysis can yield a myriad of results to help make predictive maintenance successful.
Other Technologies
Along with these techniques, facilities may use other technologies such as motor condition analysis, which details the operating and running condition of motors; and eddy current analysis, which identifies changes in tube wall thickness within centrifugal chillers and boiler systems. Borescope inspections, CMMS, data integration and condition monitoring can also help facilitate predictive maintenance. While there are several different technologies to aid in your PdM efforts, it is vital to choose the right one to ensure success.
Business Case for Predictive Maintenance
To realize return on capital investments and keep machines running at peak efficiency, facilities must place a greater emphasis on predictive maintenance. According to the Wall Street Journal, “Unplanned downtime costs industrial manufacturers an estimated $50 billion annually. Equipment failure is the cause of 42 percent of this unplanned downtime. Unplanned outages result in excessive maintenance, repair and equipment replacement.”
As operations and management are pushed toward reducing costs and increasing productivity, the need for predictive maintenance becomes clear, since it is difficult to make any cost-effective, long-term decisions for a facility.
The value of predictive maintenance comes from a cost-saving and/or time-saving approach, as maintenance is only performed when needed. In fact, several studies by the U.S. Department of Energy’s Federal Energy Management Program found that a properly functioning predictive maintenance program provides savings ranging from 30-40 percent over reactive maintenance, and 8-12 percent over preventative maintenance.
For a PdM strategy to be successful, several criteria must be considered and met. First, the commitment should come from the top down. The entire organization must be committed to making predictive maintenance a mandated part of the normal schedules. All process operators must also be educated and involved in performing the required maintenance checks. In addition, the entire organization needs to understand the actual cost and repercussions of poor maintenance. Finally, PdM procedures must be implemented immediately in order for the organization to start reaping the benefits.
While many recognize the importance of utilizing predictive maintenance for high-dollar machines, PdM is also viable for monitoring smaller, everyday assets such as coffee machines, printers, postage meters and more. In reality, an entire facility can benefit from implementing predictive maintenance.
Predictive Maintenance Applications
The biggest application for predictive maintenance is in the manufacturing sector. As manufacturing plants continue to face demand to increase productivity, several maintenance strategies have been created and implemented. However, a majority of these have been reactive. Many facilities possess a mindset of “if it’s not broke, don’t fix it.” Unfortunately, this mindset contributes to unplanned maintenance and downtime.
As discussed previously, facilities began implementing predictive maintenance in the early 1990s. Back then, “the lack of availability of sensors generating data as well as a lack of computational resources for gathering and analyzing the data made it difficult to implement PdM” (“Predictive Maintenance in Manufacturing Overview,” Microsoft Azure).
With the introduction of the internet of things (IoT), machine learning, cloud computing and big data analytics, the manufacturing industry has moved forward in implementing predictive maintenance, resulting in increased uptime and quality control, optimization of maintenance routes, improved worker safety and greater productivity. As manufacturers work with tight margins and timeframes, the thought of unscheduled downtime has become undesirable. Predictive maintenance can offer a solution.
Another application for PdM is in the railway sector, particularly as it relates to the rail industry’s digital transformation. With trains having a high initial investment, there is a keen focus on keeping them in service as long as possible. Predictive maintenance enables rail companies to get the most value out of their fleet of trains through a variety of technologies and software that reduce operating costs and extend the fleet’s lifetime.
Within the railway sector, predictive maintenance is utilized to detect problems with linear, fixed and mobile assets; improve safety and track void detection through vehicle cab-based monitoring systems; and identify the type of track asset under which the void is located, as well as provide an indication of the void’s severity.
According to an article in MaintWorld, “In the future, reliable railway maintenance is expected to rely upon smart transportation systems and interconnected solutions such as predictive maintenance and integrated security tools in order to improve critical issues like safety, delays and overall system capacity” (Peycheva, “Railway Goes Smart with Predictive Maintenance and Industry 4.0 CMMS”).
While traditionally slow to modernize its maintenance systems, the oil and gas industry is becoming a major proponent of predictive maintenance. Each day, oil and gas companies collect massive amounts of data through sensors – particularly wireless sensors – in oil fields around the world. As oil and gas operations become more complex, visibility into the equipment’s condition becomes more difficult, especially in remote, offshore and deep-water locations.
In a 2015 white paper, MapR Technologies Inc. stated, “Oil and gas companies have a major opportunity to increase efficiency and reduce operational costs through better asset tracking and predictive maintenance.”
Predictive maintenance could be seen as a competitive advantage for oil and gas companies as well as the related service businesses, particularly during times of a recession when organizations are forced to find ways to work more efficiently and effectively. Of course, predictive maintenance does not just pertain to the manufacturing, rail, and oil and gas industries. In other applications, PdM is used to:
-
Help prevent utility outages with the help of drones and sensors that map utility networks
-
Detect a temperature decline in a steam pipeline, indicating a potential pressure leak
-
Capture increased temperatures in electrical panels to prevent component failures
-
Measure supply-side and demand-side power at a common coupling point for monitoring power consumption
-
Locate overloads in electrical panels
-
Identify motor amperage spikes or overheating from bad bearings or insultation breakdowns
-
Find three-phase power imbalances from harmonic distortion, overloads, degradation or failure of one or more phases
IIoT and PdM Integration
One of the most important factors – if not the most important factor – in a successful predictive maintenance program is the use and integration of the industrial internet of things (IIoT). According to a report by Deloitte, “the Internet of Things (IoT) is perhaps the biggest piece of the PdM puzzle … IoT translates physical actions from machines into digital signals using sensors such as temperature, vibration or conductivity … Once the physical actions have been translated into digital signals via sensors, they are processed, aggregated and analyzed. With the affordability of bandwidth and storage, massive amounts of data can be transmitted to give not only a full picture of assets in a single plant, but of an entire production network” (Coleman et al., “Predictive Maintenance and the Smart Factory”).
To be successful, predictive maintenance relies on sensors for collecting and analyzing data from various sources, such as a CMMS and critical equipment sensors. Using this data, the IIoT is able to create “advanced prediction models and analytical tools to predict failures and address them proactively. Additionally, over time, new machine-learning technology can increase the accuracy of the predictive algorithms, leading to even better performance” (Coleman et al., “Predictive Maintenance and the Smart Factory”).
When paired with predictive maintenance, the IIoT has the ability to catch equipment failures in advance. With the arrival of Industry 4.0 in the manufacturing realm, facilities are eager to utilize the IIoT to gain better insights into operations.
Predictive Maintenance and Return on Investment
Implementing predictive maintenance requires a significant investment in money, personnel and education. While these initial investments might seem daunting to an organization, predictive maintenance’s return on investment (ROI) far outweighs any upfront costs.
According to a recent report by Deloitte, several facilities have seen a 5-10 percent cost savings in operations and maintenance, repair and operations (MRO) material spend; a 5-10 percent reduction in overall maintenance costs; and reduced inventory-carrying costs. Further data from the U.S. Department of Energy also shows that implementing a functional PdM program has the potential to yield a tenfold increase in ROI, a 25-30 percent reduction in maintenance costs, a 70-75 percent decrease in breakdowns and a 35-45 percent reduction in downtime.
“As far as maintenance costs are concerned, preventive maintenance costs $13 hourly pay per annum while predictive maintenance costs $9 hourly pay per annum, making predictive maintenance a cheaper option” (Ulbert, “The Difference Between Predictive Maintenance and Preventive Maintenance”).
References
Coleman, Chris, Satish Damodaran and Ed Deuel. “Predictive Maintenance and the Smart Factory.” Deloitte. 2017. https://www2.deloitte.com/content/dam/Deloitte/us/Documents/process-and-operations/us-cons-predictive-maintenance.pdf
“Condition Monitoring of Rotating Machines.” Istec International. Accessed November 1, 2018. https://www.istec.nl/en/condition-monitoring-rotating-machines/.
Control Engineering. “Predictive Maintenance Technologies.” Accessed November 4, 2018. https://www.controleng.com/single-article/predictive-maintenance-technologies/72faca6f85ddaef6b4479583b2741e6c.html.
Immerman, Graham. “The Impact of Predictive Maintenance on Manufacturing.” MachineMetrics. Accessed November 1, 2018. https://www.machinemetrics.com/blog/the-impact-of-predictive-maintenance-on-manufacturing.
Lean Manufacturing Tools. “Predictive Maintenance.” Accessed November 2, 2018. http://leanmanufacturingtools.org/427/predictive-maintenance/.
Peycheva, Ralitsa. “Railway Goes Smart with Predictive Maintenance and Industry 4.0 CMMS.” MaintWorld. October 11, 2017. Accessed November 4, 2018. https://www.maintworld.com/Applications/Railway-Goes-Smart-with-Predictive-Maintenance-and-Industry-4.0-CMMS.
“Predictive Maintenance in Manufacturing Overview.” Microsoft Azure. May 1, 2018. Accessed November 4, 2018. https://docs.microsoft.com/en-us/azure/industry/manufacturing/predictive-maintenance-overview.
“Predictive Maintenance Using Hadoop for the Oil and Gas Industry,” MapR Technologies Inc., May 2015. https://mapr.com/resources/predictive-maintenance-using-hadoop-oil-and-gas-industry/.
Ulbert, Sebastian, “The Difference Between Predictive Maintenance and Preventive Maintenance,” Coresystems, September 15, 2015. Accessed November 2, 2018. https://www.coresystems.net/blog/the-difference-between-predictive-maintenance-and-preventive-maintenance.
Wall Street Journal. Accessed November 2, 2018. https://partners.wsj.com/emerson/unlocking-performance/how-manufacturers-can-achieve-top-quartile-performance/.
Wikipedia. “Predictive Maintenance.” Accessed October 11, 2018. https://en.wikipedia.org/wiki/Predictive_maintenance.
Wright, Jeremy. “How to Leverage Multiple Predictive Maintenance Technologies.” Machinery Lubrication. Accessed November 1, 2018. https://www.machinerylubrication.com/Read/29819/predictive-maintenance-technologies
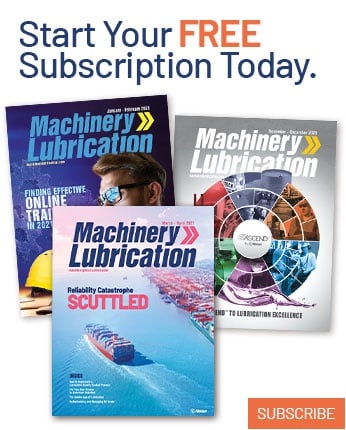