I am a shaft alignment trainer. My insight on the real state of industrial alignment practices comes from many hours spent making alignment checks and corrections on process equipment. Here are some of my observations:
-
Most of the attention to precision alignment has centered on large, process-critical machines.
-
Most maintenance departments have been downsized and spend much of their human capital addressing unscheduled maintenance.
-
Most of the unscheduled maintenance activity is on small equipment such as ANSI pumps and mixers.
-
Most plants have very few people capable of achieving precision alignment.
-
There are even fewer people who really understand shaft alignment.
-
Most tradesmen are smart and can learn alignment in one or two days.
-
Shaft alignment of direct coupled machines can be done quickly without sacrificing precision.
THINK SMALL
Small, rotating machines are often badly aligned. I see terrible things: piles of coupling debris, spare coupling parts in the mechanical room, packing and seals leaking profusely, and misalignment so severe that it can be seen with the naked eye. No doubt, large machines are important, but they are rarely severely misaligned. Huge payback can result from aligning the many small machines that often fail catastrophically. How big can the payback be? A corn processor in the Midwest with a population of around 800 pumps used to repair two to three pumps every day. After focusing on small pump alignment, the site now repairs one to two per month and is saving more than 4,000 maintenance hours per year. That is equivalent to adding two people to the maintenance staff.
Figure 1. Dimensions are entered.
WHY ALIGNMENT?The objective of precision shaft alignment is to remove destructive forces that cause premature bearing failure and reduce seal life. Destructive misalignment forces are generated at the planes of power transmission when the machines are coupled.
Every shaft rotates around an axis that forms a straight line. If two shaft rotational axes are positioned so that they are collinear when the machines are at operating temperatures and conditions, the forces at the power planes will be minimal. As a result, bearing and seal life is lengthened.
FIRST, PRE-ALIGNMENT
You can accomplish precision alignment in one or two moves virtually every time. Multiple alignment correction moves frustrate tradesmen and waste time. But, perform pre-alignment steps prior to using precision tools or your alignment corrections will be unpredictable. The box on Page 36 shows five simple steps that eliminate most unnecessary corrective moves.
Figure 2. The measurement -12.4 shows the need to add .012 inches to the front feet; +9.7 means remove .010 inches from the rear feet.
MEASURE MISALIGNMENTLaser sensors are affixed to the shafts on or near the couplings. Enter the dimensions from sensors to the coupling and to the machinery feet into the laser system (Figure 1). Most shaft alignment tolerances are based on revolutions per minute (RPM), so also enter that data.
Rotate the shafts from 60 to 180 degrees to determine the vertical and horizontal position of the two rotational axes at the sensors. The laser system calculates the misalignment at the coupling (where the forces are generated) to determine the alignment quality. In this case, color guidance indicates that the alignment tolerances aren't satisfied. The laser also computes the vertical and horizontal positions at the machine feet because that is where adjustments can be made.
Figure 3. Measure the misalignment.
CONVENTIONAL APPROACH
Conventional wisdom in shaft alignment is to completely solve the vertical misalignment first. Horizontal corrections are only undertaken after vertical tolerances are satisfied. What dismays many is that after making horizontal adjustments, the vertical tolerances are no longer satisfied. Therefore, after time has been spent to make a precise vertical alignment and after the horizontal alignment is made, the vertical will again require readjustment. This is because vertical misalignment affects the horizontal alignment and vice versa.
A NEW APPROACH
A compound move is a process where both the vertical and horizontal alignment is made from one set of alignment data. After measuring the misalignment, the vertical shim adjustment is performed.
Before rechecking the vertical outcome and before the bolts are retightened, also make the horizontal alignment (Figures 4-5). Live correction data gives the operator feedback on the correction. Color guidance indicates when tolerances are satisfied.
Only then, after both vertical and horizontal corrections are made, should you retake the alignment data. By making compound vertical and horizontal corrections, you minimize the "cross effect". The first compound move should get you very close to tolerance in both planes. Consequently, repeating the procedure with a second compound move will result in a precise alignment virtually every time.
KEYS TO SUCCESS
Here is my advice to you:
- Think small for big results: Go after the small machines that steal your human resources.
- Establish a core group: Find three people who are willing to share information and who are respected in your maintenance department. I haven't seen one really successful alignment program that doesn't have at least one "go to" person to help others with problem jobs.
- Expect widespread alignment competence: If only one or two people can perform a satisfactory alignment, then only the critical machines will get aligned properly. There won't be enough alignment talent to get to the small machines. Every person involved in mechanical maintenance should be competent at machinery alignment.
- Set alignment tolerances: Setting tolerances indicates you want to perform precision maintenance. Make the tolerances reasonable and achievable. If you make the specifications too tight, you'll only frustrate your people.
- Train for competence: Find a competent trainer that teaches both alignment concepts and equipment-specific laser techniques. Hands-on practice is a key training element. Never have more than three people per practice rig. Two days of professional training should cost between $500 and $600 per trainee.
- Tools: In addition to a laser system or dial indicator alignment tool, you need, at a minimum, shims, movers (hydraulic, pry bars, dead blow hammers) and a dial indicator with a magnetic base.
- Give people opportunities and time to gain confidence: People need the real-world practice after training in order to gain confidence. Also, new trainees will need more time to make precision alignments. With the proper tools, a one coupling alignment rarely takes more than 45 minutes, regardless of equipment size. However, new trainees will be slower. Further, you need to realize that obstacles like being base-bound or bolt-bound will slow the process down.
- Document alignment data: Correlate alignment to machinery performance and vibration data and use it for root cause failure analysis.
- Thermal growth and dynamic movement: Some machines are intentionally misaligned at ambient temperature so that the rotational axes are collinear when the machine is operating. After your people can demonstrate alignment competence, consider determining the off-line-to-running (OL2R) data required for this practice.
Figure 4.
Figure 5.
Figure 6. Final alignment data.
Figure 7. The document is saved.
David Zdrojewski is the founder and CEO of VibrAlign Inc., an educational resource and distributor of vibration analysis equipment. To learn more, call 804-379-2250 or visit www.vibralign.com.
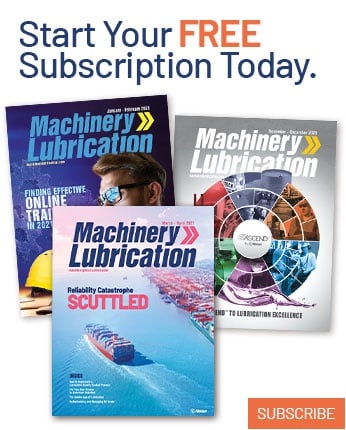