
Unexpected equipment failures can cause costly interruptions in your process flow, damage to equipment and product losses. Downtime may also divert personnel from their preventive maintenance (PM) duties. These consequences may result in expensive overtime hours and reduced PM completion rates. In extreme cases, this can eventually lead to a chaotic "run-to-fail" cycle.
Collecting Downtime Data
The best way to track equipment downtime is with a computerized maintenance management system (CMMS). Although many of these programs use a work order system to track downtime, a CMMS with a dedicated downtime module can result in better analysis and reporting of equipment problems and trends. It doesn't make sense to record an instance of equipment failure as work. Of course, a corresponding work order is usually created to correct the failure. Nevertheless, an instance of work and an instance of failure should be kept as separate records.
When collecting downtime data, it is important to determine how the downtime is logged. Are downtime cause fields user-defined and easy to understand? Some maintenance operations prefer a more general failure cause naming convention. Examples might include "electrical," "mechanical," "operational," etc. Other managers may prefer more descriptive cause definitions such as "blown fuse(s)," "operator error" or "water in electrical." Either way is acceptable if it suits the maintenance manager's requirements. However, a more descriptive failure cause will lead to a more accurate analysis of downtime later.
Logging the actual time the equipment is down is important, but what about other losses attributed to this event? In many cases, product losses due to equipment failures, employee overtime and other bottom-line factors outweigh the direct maintenance costs for downtime. A good downtime tracking system must consider all of these factors.
Benefits of Downtime Tracking
Downtime data is valuable for many reasons. First, by understanding downtime trends, you can prioritize and implement corrective action to prevent additional equipment failures. A CMMS that can track downtime fields like the maintenance shift and geographical location will further empower the maintenance manager's decision-making. Perhaps downtime is disproportionate during a certain production shift. This could be resolved with training and have nothing to do with maintenance efforts.
Downtime data can also help the maintenance manager prioritize preventive maintenance and equipment replacement. Justifying equipment replacement can now be verifiable and simplified. Statistical analysis, reporting and charting of downtime history will reveal equipment breakdown trends. These trends can then be used to guide your preventive and remedial efforts.
Tracking downtime has a profound effect on how, when and where maintenance resources are used. The time invested in logging equipment downtime can also be easily justified by the time- and money-saving benefits to the maintenance department and the organization as a whole.
About the Author
Daniel Cook is the vice president of development for MaintSmart CMMS Software. He has spent more than 25 years in maintenance, including 15 years as a maintenance manager.
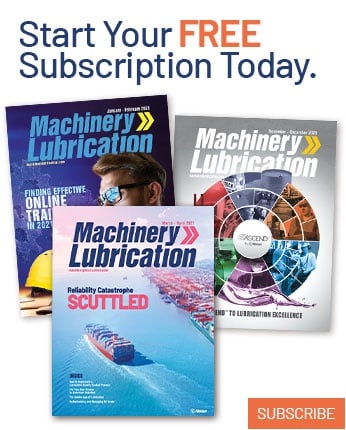