Reliability refers to how consistent a plant's operation and performance are. Thus, a plant boasting high reliability demonstrates the capability to sustain consistent production levels, meet market demands, and avert unexpected asset failures and downtime.
According to findings and benchmarks from Solomon & Associates and Emerson, top-performing entities in the first quartile managed to cut maintenance costs by three to five times compared to their less successful counterparts. Simultaneously, their asset availability reached levels that were seven to 14 percent higher. The key to achieving these outcomes lies in adopting best practices in maintenance and reliability.

Source: RAM study, Solomon consulting
Embarking on this journey starts with a crucial initial step: benchmarking your organization against industry leaders. This process involves undergoing a comprehensive maintenance and reliability assessment, which, when executed correctly, yields a detailed action plan for you and your team.
A robust maintenance and reliability assessment should encompass various essential components to thoroughly evaluate the performance of a manufacturing plant and its maintenance practices. These foundational elements should revolve around the following core pillars:
Pillar 1: Asset Reliability Foundation
- The CMMS (Computerized Maintenance Management System) features a thorough, precise, and comprehensive master equipment list.
- Parts, including items and materials, are meticulously detailed, uniquely identified, easily procurable, and maintained at optimal inventory levels.
- Bills of Materials (BOMs) are both accurate and comprehensive.
- Regular and up-to-date criticality ranking is conducted, considering impacts on safety, environment, operations, maintainability, and quality.
- Maintenance strategies are clearly defined for all assets, aligning with criticality rankings and addressing specific failure modes. The aim is to ensure that the right task is carried out at the right time, by the right person, and in the right manner. The effectiveness of these strategies is continually assessed to prevent breakdowns and optimize asset performance.
-
The facility is consistently maintained in a clean condition, and assets are appropriately lubricated.
Pillar 2: Work Management
- Review and analyze maintenance workflows and processes, from work order initiation to completion. Identify bottlenecks, inefficiencies, and opportunities for automation or optimization.
- Evaluate roles and responsibilities in key work management elements, including work identification, planning, scheduling, execution, feedback, and follow-up.
- Monitor the efficiency of planning and scheduling through metrics such as preventive maintenance (PM) compliance, backlog management, and wrench time.
-
Ensure efficient and effective execution of shutdowns and turnarounds.
Pillar 3: Craft Skills
- Assess maintenance technicians' skills and training levels, ensuring they are adequately trained and certified for effective job performance.
- Promote the application of precision maintenance techniques by craftsmen, emphasizing proper installation, alignment, balancing, and torque application.
- Encourage operators to engage in defect elimination, providing training and support as necessary.
-
Establish competency development plans for all trades.
Pillar 4: Parts Management
- Evaluate the spare parts inventory management system to ensure the availability of critical spare parts and minimize downtime during equipment failures.
- Perform parts criticality ranking based on lead time, costs, usage, and default detectability.
- Define service levels based on parts criticality, automate min/max, and reorder processes considering criticality, service levels, and safety stocks.
-
Assess warehouse practices, including storage, labeling, accuracy, and other relevant aspects.
Pillar 5: Reliability Engineering
- Define and measure key reliability metrics, including Mean Time Between Failures (MTBF), Mean Time to Repair (MTTR), and Overall Equipment Effectiveness (OEE), to gain insights into asset performance and maintenance effectiveness.
- Evaluate the plant's approach to root cause analysis for equipment failures, ensuring thorough investigations to prevent recurrence.
- Review the implementation of condition monitoring techniques and technologies, such as vibration analysis, thermal imaging, and oil analysis, to detect equipment degradation early.
-
Explore using data analytics and predictive maintenance tools to identify equipment issues and optimize maintenance interventions proactively.
Pillar 6: Leadership for Reliability
- Conduct performance benchmarking by comparing the plant's maintenance and reliability performance with industry benchmarks and best practices to identify areas for improvement.
- Establish a culture of continuous improvement, using feedback from assessments to drive ongoing refinements in maintenance practices.
- Align the maintenance budget with the plant's needs and allocate resources effectively to support maintenance efforts.
-
Define and track key performance indicators (KPIs) related to maintenance and reliability, such as equipment uptime, maintenance cost as a percentage of revenue, and mean time to failure.
How to Properly Conduct the Assessment and Build the action Plan
Engage all stakeholders throughout the assessment process, including maintenance teams, operations, procurement, HSE, and management. This inclusive approach ensures a diverse perspective and secures buy-in for future improvement initiatives.
Complete the assessment within a timeframe of three days for a single manufacturing plant, allowing for 45-minute interviews with the mentioned personnel. Subsequently, compile findings into an Excel table detailing all action items. Prioritize these actions based on two criteria:
Effort to Implement:
1 = High effort
3 = Low effort
Effect/Impact after Implementation:
1 = Negligible impact
3 = High impact
Multiply the scores for each action item and sort them in descending order (9 to 1) to identify low-hanging fruit. Collaborate with key plant stakeholders to conduct the prioritization exercise. Once prioritization is complete:
- Identify the person responsible for each action item.
- Set reasonable deadlines for completion.
Example of a timeline for an action plan in a chemical facility
Consider the budget required for each item (determine if it falls under capex investment or regular maintenance budget).
This systematic approach ensures that improvement efforts are strategically aligned and responsibilities, timelines, and budget considerations are transparently established with input from all relevant stakeholders.
What Happens After?
After prioritizing and assigning responsibilities, the following steps involve:
- Identify a Champion: Designate a champion who will be held accountable for overseeing the implementation of the action plan. This individual should be committed, influential, and possess the necessary skills to drive change.
- Establish Recurring Meetings: Schedule recurring meetings immediately to ensure ongoing progress and address any challenges during the implementation phase. These meetings should involve key stakeholders to maintain alignment and commitment.
- Emphasize Collaboration: Stress the importance of collaboration and support from all organization members. Building a culture where reliability is seen as everyone's responsibility fosters a collective commitment to the improvement process.
- Leadership Involvement: Upper management should lead the change initiative and actively participate in the implementation process. Their visible support and engagement set the tone for the entire organization and reinforced the significance of the reliability improvement efforts.
- Continuous Improvement: Conclude by reminding readers that reliability in a manufacturing organization is an ongoing effort. The action plan should be regularly reviewed and updated to adapt to changing plant needs and industry trends. This ensures that the organization remains agile and responsive to evolving challenges.
- Just do it! You have spent time and effort on building this action plan. There is no excuse not to execute it!
In summary, a successful maintenance and reliability assessment is characterized by its thoroughness, reliance on data, and a clear focus on achieving tangible improvements in equipment performance, uptime, and cost-effectiveness. It should be viewed as a dynamic and iterative process, with regular assessments and updates to stay aligned with evolving organizational needs and industry advancements.
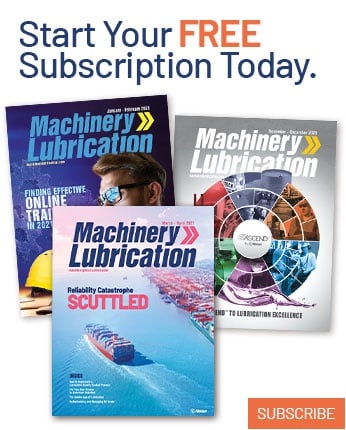