Introduction
Performance measurement is a fundamental principle of management. Performance measurement is crucial because it identifies gaps between the current and desired performance and indicates progress toward closing the gaps.
Carefully selected Key Performance Indicators (KPIs) identify precisely where to take action to improve performance.
Physical Asset Management
The purpose of most equipment in manufacturing is to support the production of products destined for downstream customers. The focus is on meeting customer needs. Customer expectations are usually defined by product quality, on-time delivery, and competitive pricing.
By reviewing the composite requirements of all current and potential customers in those markets we wish to penetrate, the performance requirements of our physical assets can be defined. Manufacturing performance requirements are quality, availability, customer service, operating costs, safety, and environmental integrity.
To achieve this performance, there are three inputs to be managed.
- Design Practices: Provide capable equipment "by design" (inherent capability) to meet the manufacturing performance requirements.
- Operating Practices: Make use of the inherent capability of processing equipment. The documentation of standard operating practices assures equipment's consistent and correct operation to maximize performance.
- Maintenance Practices: Maintain the inherent capability of the equipment.
Deterioration begins to take place as soon as equipment is commissioned. In addition to normal wear and deterioration, other failures may also occur. This happens when equipment is pushed beyond its design limitations or operational errors occur. Degradation in equipment conditions results in reduced equipment capability. The visible outcome is equipment downtime, quality problems, or the potential for accidents and/or environmental excursions. All of these can negatively impact operating costs.
Manufacturing KPIs provide information on the current state of manufacturing. Asset capability, operating practices, and the maintenance of asset conditions all contribute to the ability to meet these performance requirements.
Some typical KPIs for manufacturing include:
- Operating costs
- Asset availability
- Lost time injuries
- Number of environmental incidents
- Overall Equipment Effectiveness (OEE)
- Asset utilization
Consider asset utilization – a manufacturing-level KPI. It is a function of many variables. For example, asset utilization is impacted by both maintenance and non-maintenance-related downtime. Non-maintenance-related downtime may be attributed to:
- A lack of demand
- An interruption in raw material supply
- Production scheduling delays beyond the control of the maintenance function
Asset utilization is also a function of operating rate, quality, yield losses, etc. Maintenance may be a factor in each of these areas, but it is not the only contributor. To maintain and improve performance, each function in the organization must focus on the portion of the indicators they influence.
Similarly, other manufacturing-level performance indicators are not only a function of maintenance. They are affected by causes beyond the control of the maintenance function. Asset capability, operating practices, and the maintenance of asset conditions all contribute to the ability to meet performance requirements.
Suppose a manufacturing level indicator is used to measure maintenance performance. In that case, improved maintenance may not result in a proportional improvement in the manufacturing metric.
For instance, the maintenance contributors may all be positive in the asset utilization example cited above. Yet, the resulting asset utilization may not improve due to other causes.
A key principle of performance management is to measure what you can manage. To maintain and improve manufacturing performance, each function in the organization must focus on the portion of the indicators they influence. Maintenance performance contributes to manufacturing performance, and KPIs for maintenance are selected to ensure a direct correlation between the maintenance activity and the KPI measuring it.
When defining a KPI for maintenance, a good test of metric validity is to seek an affirmative response to this question:
"If the maintenance function does 'everything right,' will the suggested metric always reflect a result proportional to the change or are there other factors, external to maintenance, that could mask the improvement?”
The maintenance function can involve other departments beyond the maintenance organization. Similarly, the maintenance department has added responsibilities beyond the maintenance function and, as such, will have additional KPIs to report.
Maintenance organizations may include KPIs for other areas of accountability, such as health and safety performance, employee performance management, training and development, etc.
The Asset Reliability Process
Managing physical asset performance is integral to business success, including maintaining physical asset reliability.
The Asset Reliability Process is an integral part of a proactive system. It is represented by seven elements that deliver the performance required to meet a facility's corporate objectives. Each aspect is essential to provide an effective maintenance strategy. Omitting any element will result in poor equipment performance, increased maintenance costs, or both.
The seven elements include:
- Business Focus: Focuses on the maintenance of physical asset reliability and the company's business goals. The potential contribution of the asset base to these goals is evaluated. The most significant contributors are recognized as critical assets, and specific performance targets are identified.
- Work Identification: Produces technically based Asset Reliability Programs. Program activities identify and control failure modes impacting the equipment's ability to perform the intended function at the required performance level. Activities are evaluated to judge if they are worth doing based on the consequences of failure.
- Planning: Develop procedures and work orders for these work activities. The procedures identify resource requirements, safety precautions, and unique work instructions required to execute the work.
- Scheduling: Evaluate the availability of all resources required for work "due" in a specified time frame. Often, this work requires the equipment to be shut down. A review of production schedules is required. Resources are attached to a specific work schedule. The use of resources is balanced out.
- Execution: Trained, competent personnel perform the required work.
- Follow-Up:Respond to information collected in the execution process. The work order completion comments outline what was done and what was found. The actual time and manpower to complete the job are documented. Job status is updated as complete or incomplete. Corrective work requests resulting from the analysis of inspection data are created. Requests are made for changes to drawings and procedures.
- Performance Analysis: Evaluates maintenance program effectiveness. Gaps between actual process performance and the required performance are identified. Historical maintenance data is compared to the current process performance. Maintenance activity costs are reviewed. Significant performance gaps are addressed by revisiting the Work Identification function.
Performance Metrics for the Maintenance Function
The Asset Reliability Process represents the collection of all the tasks required to support the maintenance function. If a step in the process is skipped or performed at a substandard level, the process creates failures.
Asset Reliability Process measures are leading indicators. They monitor if the tasks being performed will produce the desired results. For example, a leading process indicator would monitor if the planning function was taking place. If people do all the right things, the results will follow. The leading process indicators are more immediate than result measures.
Result measures monitor the products of the Asset Reliability Process, including:
- Maintenance costs (as a contributor to total operating cost)
- Asset downtime due to planned and unplanned maintenance (as a contributor to availability)
- The number of failures on assets (the measure of reliability, which can be translated into mean time between failures)
The maintenance function's KPIs need to include leading (maintenance process) measures and lagging (result) measures. Collectively, these measurements are the KPIs for the maintenance function.
Key Performance Indicators of Maintenance Effectiveness (Result Measures)
The product of maintenance is reliability. A reliable asset is an asset that functions at a performance level that satisfies the user's needs. Reliability is assessed by measuring failure.
Failures
The primary function of maintenance is to reduce or eliminate the consequences of physical asset failures. Functional failure is defined as any asset performance falling below its required performance. Therefore, a KPI for maintenance effectiveness is measuring failure on the asset(s). If the maintenance function is effective, failures on critical assets and, thus, their consequences should be reduced or eliminated.
Failure consequences impact manufacturing-level KPIs. Failure classification by consequence identifies the contribution of maintenance function to manufacturing-level performance.
Failure consequences are classified into the following categories:
- Hidden Consequences: There is no direct consequence of a single-point failure other than exposure to the increased risk of multiple failures (a second failure has to occur to experience a consequence).
- Safety Consequences: A single-point failure results in a loss of function or other damage that could injure or kill someone.
- Environmental Consequences: A single-point failure results in a loss of function or other damage that breaches any known environmental standard or regulation.
- Operational Consequences: A single-point failure directly affects operational capability (output, product quality, customer service, and operating costs, in addition to the direct cost of repair).
- Nonoperational Consequences: A single-point failure involving only the cost of repair.
Therefore, tracking the number and frequency of asset failures by area of consequence is important. This metric has no universal standard because of the diversity of industries and even plants within industry segments. However, it is reasonable to expect a downward trend and set reduction targets based on current performance levels and business needs.
Maintenance Costs
Maintenance costs are another direct measure of maintenance performance—maintenance effectiveness and efficiency impact maintenance costs. Maintenance maximizes effectiveness by ensuring it performs "The Right Work at the Right Time.” Proactive maintenance means intervening before the failure event occurs.
The impact of proactive maintenance is not only to minimize the safety, environmental, and operational consequences of failure but also to reduce the cost of maintenance by reducing secondary damage. Less secondary damage means that repairs take less time (labor savings) and consume fewer parts (material savings).
Maintenance costs are also impacted by increasing maintenance efficiency. These efficiency gains are achieved through improved planning and scheduling of the proper work at the right time.
Maintenance Related Downtime
The maintenance function impacts asset availability by minimizing downtime attributed to maintenance, including scheduled and unscheduled maintenance. A key objective of proactive maintenance is to identify potential failures with sufficient lead- time to plan and schedule the corrective work before actual failure occurs.
It is equally important to measure scheduled downtime. The work identification element of the maintenance process strives to eliminate unnecessary scheduled maintenance by focusing on only performing the right work at the right time. Through more formal work identification and enhanced planning and scheduling, shutdown overruns should be minimized.
The Importance of the Work Order
Implementing KPIs for the maintenance function requires a reliable source of data on asset failures, maintenance costs, and downtime. Any time maintenance is performed on an asset; a maintenance work order should be created to create and organize this data.
A work order should include the following information:
- Asset identification at the level in the asset hierarchy where the work was performed.
- Date, time, and duration of the maintenance event.
- An indication if a failure has occurred.
When failure occurs, the maintenance work order should also include:
-
Identification of the failure consequences
- Hidden
- Safety
- Environmental
- Operational (product quality, throughput, customer service, operating costs)
- Nonoperational (cost of the repair)
- Actual costs (labor, materials, services)
- Process downtime (loss of production)
- Asset downtime (equipment out of service, but production can continue)
Queries in your Computerized Maintenance Management System (CMMS) can then be developed to track and report KPIs for asset failures, maintenance costs, and downtime.
Reporting and Use of Key Performance Indicators
Key performance indicators should align with defined roles and responsibilities for the maintenance function against the assets for which they apply. For example, a planner for 'Area A' would be responsible for the planning function KPIs for the ‘Area A’ assets.
The manager responsible for Area A assets would monitor all process and result metrics for Area A. Each metric should align the asset hierarchy with individual responsibility for the assets. Management’s action focuses on improving compliance with the requirements of Work Identification, Planning, Scheduling, Execution, and Follow-up.
In this way, the process is managed, leading to world-class results. This logic is repeated at each level of management in the organization. At the plant and/or corporate level, management exercises accountability for plant-wide maintenance metrics, both process and results.
Conclusion
Maintenance and reliability business process metrics (leading indicators) indicate compliance with the maintenance business process. They indicate where to take specific action because of a gap in how maintenance is performed.
This gap in the execution of the maintenance process will ‘eventually’ lead to asset failure(s). The consequence of these failures translates into poor manufacturing performance.
Therefore, maintenance, reliability, engineering, and operations must work together to define and measure the leading indicators of the asset reliability process (the seven elements required to support the maintenance function). The result will be optimal asset reliability at optimal cost – a healthy Asset Reliability Process output.
NOTE:
This paper is a selected chapter from "Rules of Thumb for Maintenance and Reliability Engineers Handbook" by Ricky Smith and R. Keith Mobley and republished on Reliable Plant with author permission. Republishing without author consent is prohibited. Editorial preferences that do not impact the quality or accuracy of the information herein have been made to maintain publication editorial guidelines.
To purchase a copy of this book, visit the Noria Bookstore here.
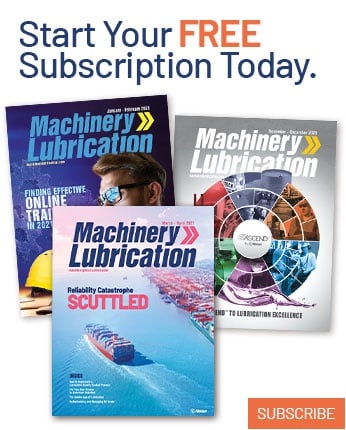