Improving asset uptime through condition inspections and predictive maintenance is a critical yet often underutilized reliability practice. For many manufacturing facilities, maintaining a dedicated condition-based inspection team can be challenging due to size constraints or difficulty retaining necessary expertise. In these cases, partnering with third-party reliability service companies can be a practical solution.
These service companies provide the necessary personnel, equipment, knowledge, and experience to help plants implement effective condition-based maintenance programs. They offer flexibility in maintaining in-house expertise for specific inspections while outsourcing others.
When selecting a reliability services provider, it is essential to address several key questions:
- What assets require inspection?
- What technologies will be used?
- What is the inspection frequency?
- How will results be reported, and who will be accountable?
- How can the plant ensure all contracted machines are inspected?
- Are results provided in print or online?
- Who is responsible for creating work orders?
- Is there a weekly status meeting included in the contract?
- What are the contractor’s responsibilities for critical machine inspections?
- Is the contractor responsible for validating repairs?
- What program metrics are required?
- Is there a need to calculate and report program savings or avoided costs?
Many leading reliability services companies now leverage off-the-shelf reliability information management systems (RIMS) to consolidate data and enhance their services. These systems enable better elimination of in-service failures, extended operating life between failures, and improved productivity through timely and robust analysis.
This means improved reliability outcomes for asset owners and operators without investing in advanced reliability tools or systems. This article explores how reliability services companies enhance their interactions and reporting with partner plants, and why a robust software platform is crucial for success.
Bridging the Gap between Plants and Service Providers
Historically, the interaction between plants and service providers has faced challenges. Some plants prefer direct entry of work orders into their Computerized Maintenance Management System (CMMS) when defects are identified. However, according to Dean Stephens, reliability director at Benchmark Reliability Services, many CMMS systems need more granularity to optimize condition monitoring efforts. This limitation can obscure important details necessary for effective maintenance.
Alternatively, some plants use spreadsheets, which can become cumbersome when managing large equipment counts. Dave Reynolds, owner of Midlands Reliability & Consulting, notes that while spreadsheets may work for smaller operations, they become inefficient for larger ones, complicating the task of tracking, organizing, and reporting findings.
Advantages of RIMS for Service Providers
Reliability information management systems (RIMS) address these challenges by providing a consolidated and consistent information source. These systems integrate data from multiple condition-monitoring technologies into a standardized database, offering several benefits:
- Consolidated Information: A single source of truth replaces disparate information sources, allowing for efficient communication and standardized reporting.
- Standardized Reporting: Automated and standardized reporting improves accuracy and control with readily available integrated condition status reports and lifecycle metrics.
- Active Communication: RIMS facilitates proactive scheduling, historical activity tracking, and real-time updates, enhancing communication between service providers and clients.
- Increased Accountability: Tasks managed within the RIMS ensure accountability through auditable actions and automated notifications, improving quality control.
-
Best Practices Enablement: Access to comprehensive data supports root-cause failure analysis and continuous improvement efforts.
Renewed Relationships through RIMS
Adopting RIMS enhances the relevance of roles and relationships within reliability services. Providers can demonstrate the value of their services through data and statistics, boosting client retention and satisfaction. Clients better understand their equipment’s performance, aiding in better planning and budget allocation. Technicians benefit from seeing the impact of their detailed work, fostering a sense of pride and contribution to operational improvements.
Ultimately, a robust RIMS supports a more collaborative and informed decision-making process, strengthening the partnership between plants and their reliability service providers.
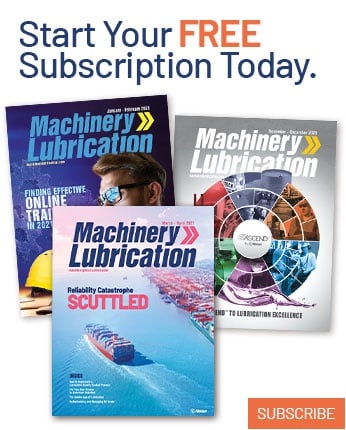