Reliability has become a buzzword commonly used to describe maintenance improvement initiatives. Several books have been written with titles such as Reliability-Centered Maintenance, Reliability-Based Maintenance, etc.
In these books, I have not yet found a definition of reliability. Many suppliers of predictive maintenance tools also use the term reliability to describe their products and services.
Definitions
Dictionaries describe reliability as: dependability, trustworthiness, consistency. To me, reliability is best described as, “being able to be trusted to do what is expected or has been promised.”
Here, we talk about reliable production in pulp and paper mills, so it is obvious that the term reliability cannot only focus on maintenance improvement initiatives or only predictive maintenance.
We use the term “production reliability” to lay the foundation for the vital partnership between operations and maintenance. In this concept, operations and maintenance both deliver reliability as a result of their work. Operations focuses on reliable process and maintenance focuses on reliable equipment.
To become true partners, the operations and maintenance departments must have one common performance measurement as described in the figure below.
Measurements of Reliability
Quality Performance x Time Performance x Speed Performance
90% x 90% x 90% = 72.9%
Reliability Index = MTBPL \ MPL
MTBPL = Mean Time Between Production Loss (Time running/number of production losses)
MPL = Tons Lost/Number of Production Losses
The most common way to measure overall production reliability is to measure quality, time and speed performance. Time performance must include all available hours; for example, 8,760 hours in a year less market-related downtime and time for capital rebuilds.
Reliability Index
Another way to measure overall production reliability is the reliability index. You must know three things to use this index: production calendar time, number of production losses, and total production losses including losses in quality, time and speed.
In summary, the reliability index says that you want to operate as long as possible without losses; and when you have losses, you want to fix them as quickly as possible.
What is Asset Management?
Asset management is another word hijacked by providers of maintenance services and products, especially by computer system suppliers.
To me, asset management includes much more than maintenance management software. I wonder how many maintenance managers would respond to an ad in the Wall Street Journal for a position as asset manager.
A company’s assets include much more than maintenance management – you must also consider brand name, patents, capital, etc. Even the term Equipment Asset Management is not appropriate because the right people, their skills and commitment are more important assets.
New terms for the same things can only lead to confusion and a lack of followers for improvement efforts. Whatever you chose to call your concept, explain it well and stick to it long term. An idea would be to use the term maintenance to describe maintenance activities and production reliability to describe and measure the results of your operations and maintenance organization’s work.
Torbjörn (Tor) Idhammar is partner and vice president of reliability and maintenance management consultants for IDCON Inc. His primary responsibilities include training and implementation support for preventive maintenance/essential care and condition monitoring, planning and scheduling, spare parts management, and root cause problem elimination. He is the author of “Condition Monitoring Standards” (volumes 1 through 3). He earned a BS in industrial engineering from North Carolina State University and an MS in mechanical engineering from Lund University (Sweden). Contact Tor at 800-849-2041 or www.idcon.com.
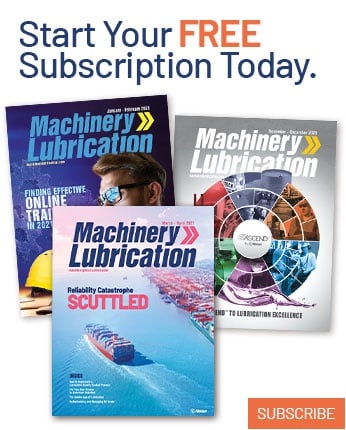