Over the last year or so, the question of reducing the cost of reliability has been ever present. Many maintenance budgets have been slashed without due process or reflecting on the true cost over time. I recently attended a conference where this was a topic of conversation.
Out of all the discussions that I have heard, the most effective statement was to respond to that request from a CEO or plant manager with the following question: “How much are you willing to reduce the amount spent on safety?”
Unfortunately, not everyone makes the tie that reliability and safety go hand in hand. I am reminded of a letter that Dave O’Reilly, the CEO of Chevron Corporation, sent to employees where he said, “Reliability, like safety, is a critical element of operational excellence and requires our constant attention.” I couldn’t agree more.
Reliability drives safety and vice versa. Consider that most accidents don’t occur when things are running smoothly and the equipment has a high level of reliability. Accidents occur when we fall into reactive chaos.
When a packaging machine is no longer operating in a reliable state, lots of minor stops may cause an operator to reach into a running machine (bypassing the safety procedures) and remove jammed cartons or film. The moment of frustration may cause the loss of a finger, hand or worse.
Less spending on maintenance may result in more leaking piping or vessels. The operator gives up on keeping the floor clean. Now, not only are the pipes leaking, but the main process line is acting up.
When the product piles up on the end of a main conveyor due to a neglected bearing, the operator makes a mad dash to clear the pileup. On the way, he or she slips and falls in the area where the leak has created a puddle on the floor. The spiral only worsens.
The challenge that we face as maintenance and reliability professionals is to connect the dots for our leadership. We have to elevate maintenance and reliability as a profession and not have it viewed as “a necessary evil.” Sure, it is one of the most controllable costs in a site.
When you toss out labor as a “sunk cost” (X number of people to produce X number of widgets), the largest (and easiest target) is the maintenance budget. Most every other cost requires capital to influence (energy costs, as an example) or is fixed via contract (logistics, raw materials, etc.) or global pricing.
While it is one of the most controllable costs, maintenance and reliability can be one of the greatest drivers of productivity and reduced costs. This is done not by slashing the budgets indiscriminately, but by keeping the focus on reliability as a long-term investment strategy.
So when you are asked by the CEO or plant manager about reducing reliability costs, ask if that leader is willing to reduce the organization’s investment in safety.
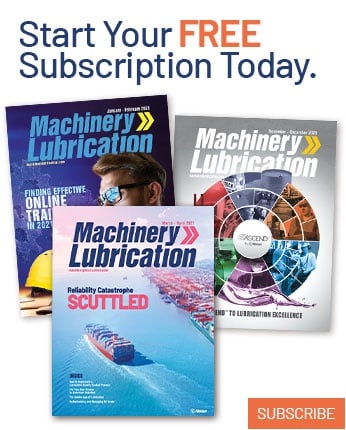