When faced with the task of improving plant efficiency, the average plant manager breaks the task down by the five or six existing "departmental silos." Each silo leader subdivides responsibility, repeating the mistake, and passes it on to individuals.
As a result, we see young, intelligent engineers overwhelmed by the task handed to them of "get out there and improve maintenance." The situation is not so bad for the less intelligent or those who have become automatons; they just keep repeating what has gone on forever and collect another paycheck.
What the plant manager needs is a better way to visualize his situation, a method that will allow him to develop a new strategy. The following insights are based on work done at MIT and by many other professors in "human error" at international centers of learning.
The "Error Pyramid" is unique, but the remaining techniques and technologies have been established for 15 years or more.
Insight No. 1 — Most people are familiar with the triangle hierarchy of safety incidents that shows that for every fatality there are seven serious accidents and dozens of minor incidents; and below that, there are many hundreds of near-misses. By reducing the number of near-misses, there will be a corresponding number of minor and serious injuries.
Taking the four main activities involved with manufacturing — safety, reliability, quality assurance and operating performance (accuracy) — each can be viewed as similar triangles. When placed together, they form a pyramid with a four-sided base.
Insight No. 2 — People in each silo see their problems as unique and have little time or apparent incentive to work on the other guy’s issues. They do, however, use common primary methodologies for solving problems within each of them — root cause analysis (RCA), cause and effect analysis, failure modes and effects analysis (FMEA), etc.
In my many years of experience, I've seen that any change in one area affects the remaining three. In a very specific sense, I always see an improvement in safety and quality as reliability and operational accuracy improve.
Insight No. 3 — Efficient manufacturers have small problem/error pyramids, while the less efficient have massive pyramids that overshadow everything else (i.e., the classic reactive mode of operation).
The more errors and mistakes made, the larger the pyramid becomes. Alternatively, the more problems that can be solved, the smaller it becomes. Unfortunately, this is a dynamic situation, and even though people solve problems every day, the pyramid of problems never seems to get smaller. Insight No. 4 will explain why this is true.
Insight No. 4 — We, and the systems with which we surround ourselves, are the products of the human mind. They are by our very nature prone to make errors at a constant rate (see David L. Weiner’s books on the human mind). Therefore, having an understanding of how and why we make mistakes is critical to the task of reducing their frequency and effect.
Insight No. 4A — Nobody ever deliberately makes a mistake, particularly those working among a group of peers. As an example, football players often drop passes, but nobody does so deliberately.
Reducing the Number of Errors Made
What is needed is to not only get better at solving problems but also to take some action that will reduce the number of new problems being created.
Insight No. 5 — We need a "non-penal system" that allows us to recognize all the errors so that we can classify them by type and respond to the causes across the organization. Not surprisingly, you will find that 90 percent of the issues identified can be considered as latent or systemic.
Many old systems were driven by veiled versions of "the beatings will continue until performance improves," and we have seen just how ineffective this has been.
As one director of manufacturing at a plant with an excellent error-proofing program said, "I can see the value of this non-penal system, but if the screw-up was big enough … someone would still have to go."
Let us assume that your company has one of the few problem-solving methodologies (RCA, etc.) that produces documented multiple root causes that also include the latent and systemic issues (even though the team is impotent in initiating corrective actions). What is next?
Insight No. 6 — Having achieved awareness of a primary issue, you need a formal program of error-proofing. The methodologies are applicable across all four silos, and the training involved should go a long way toward eliminating the existing silo mentality.
Developed in the aviation industry and rapidly adopted by the nuclear and health-care sectors, these techniques are saving billions of dollars each year. My experience is that using formal error-proofing techniques can produce some amazing improvements.
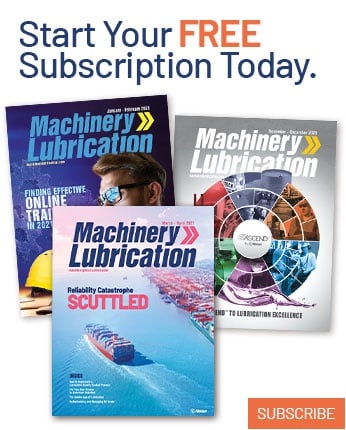