The current crop of predictive maintenance (PdM) management software now delivers instantaneous decision-making power for those engineers and plant managers charged with wringing the maximum utility from their facilities while conserving maintenance costs.
Capable of instantly analyzing and interpreting vibration data – along with ferrography, used-lubricant analysis and visual inspections – today’s PdM software not only delivers integrated and prioritized information to plant managers in their offices, but throughout the entire organization via enterprise-wide “electronic in-trays,” text messages, pager alerts and even HTML pages accessible via a common Web browser.
Predicting the repair needs of critical components in lathes, mills, turbines, fans, drills, pumps and any other rotating device allows today’s MRO executives to control the destiny of their plant’s operations by preventing unexpected shutdowns in the first place. This ability to plan for the future is no longer the domain of Fortune 500 companies, as PdM software’s power to deliver answers, not merely data, has even trickled down to small and mid-sized businesses. However, it wasn’t always that way.
Building upon the past
It wasn’t that long ago that plant engineers relied on run-to-fail (RTF) maintenance schedules – a method that almost guaranteed unscheduled process line shutdowns. Hardly satisfactory, the maintenance industry welcomed advances in computerization as a means to help prevent expensive machine breakdowns.
“When we started out doing machine condition analysis for the U.S. Navy back in 1966, the vibration work was all manual,” recalls Dean Lofall, the product development manager for Woburn, Mass.-based Azima DLI, one of the world’s most advanced suppliers of vibration analysis instruments and PdM programs.
“You’d have a group of engineers that went out on the ship for 10 days to gather all the measurements via analog instrumentation tape recordings. It would then be played back by technicians through a processor to produce a five-foot high stack of graphs. For the next three weeks, a group of engineers would go through all the data, manually categorizing all the machinery and making specific repair recommendations.”
Even the private sector “made do” with rudimentary results while absorbing huge manpower expenses. Automakers and power companies, for example, would maintain vast banks of vibration experts for the sole purpose of tracking machine life.
Perhaps the persistent vision of massive mainframes crunching data from cumbersome Winchester drives possibly accounts for the reluctance of some individuals to believe that today’s basic PdM software can run on nothing more than a first-generation Pentium desktop computer.
Yet, given the comparative low cost of entry and the gains to be had, maintenance managers of even small manufacturing facilities are now turning to full-featured PdM systems. Such are the advances that have been made over the past couple of years.
Today’s systems save money
Overly cautious, prevention-minded systems of the last decade wasted valuable maintenance resources by manually analyzing each piece of new data, whether the machines needed attention or not.
“We’ve observed that 80 percent of the machines in a typical plant will have no serious mechanical faults,” says Lofall. “So why waste time on machine parts that have no need for replacement? State-of-the-art predictiveprograms employ expert systems to weed out machine test-results that look acceptable; thus allowing analysts to focus only on those machines that may have faults. The time saved by not manually reviewing the data from every single machine in a plant is significant.”
As an example: Some 30 years after its initial work for the Navy, Azima DLI deployed its expert system of PdM software to analyze data for thousands of machines within the U.S. Navy Sealift Command. A subsequent study of 332 such machines confirmed savings of between $47,000 and $62,000 per month, as opposed to manually calculating the data with in-house engineers. The accuracy rate proved to be 8 percent greater with the PdM system, as well.
Today’s PdM systems even predict the future of new equipment
Spectacular gains in maintenance efficiency and dollar savings have resulted from integrating modern PdM systems into existing facilities. Yet, the use of PdM to predict the useful life of brand newmachines promises to save organizations even more money. In recent years, DaimlerChrysler’s Toledo North assembly plant avoided costly downtime by accurately predicting maintenance failures in newly purchased equipment.
“During the launch period of this new plant we requested evaluations via vibration analysis and infrared analysis as one of our buy-off criteria before we signed off on the equipment and took ownership,” recalls Terry Kulczak, the maintenance advisor for the Toledo plant. “We had already settled on the Azima DLI system for this task because we had good success with it at our Durango plant in Newark, Delaware.”
Kulczak explains that his team used their PdM system to evaluate more than 600 pieces of new equipment such as regenerative thermal oxidizer motors, water pumps, cooling fans and gearboxes.
“Using the software, we found that there were some machines out there that weren’t up to spec,’” says Kulczak. “Some had bad bearings, alignment problems and improperly sized shims, which led to excessive vibration. These had to be changed out, and it was all done under warranty.”
At least 106 pieces of equipment needed adjustment or new parts. In his report to management, Kulczak estimated that the maintenance costs to repair these defects – had they not been detected in advance – would amount to at least $31,000, with a possible maximum cost of $112,000. Production losses due to failed machinery would have resulted in even greater losses to the plant’s bottom line.
“The software analyzed the data and spit out the summary sheet, so you can go back into the data and decipher it a little more closely if you want,” says Kulczak. “From what I understand, older software out there did not have these features. A lot of the contractors questioned our calls, and they didn’t use DLI. But we showed them the data and it turns out we were right.”
Gains made possible through improved data collectors
The above-mentioned, bottom-line savings earned by investments in maintenance management have occurred through the continuous evolution of each element of the PdM chain. Progress has been achieved at every step, beginning with technological advances in field instrumentation that measures torsional vibration, torque and horsepower, motor current, structural vibration, shaft alignment, and acoustics with every increasing accuracy and fidelity.
Even more important, an emphasis on portability has placed condition monitoring into the hands, literally, of production floor personnel. As proof, Azima DLI’s DCX pen-tablet handheld computer can host a replica of an entire condition monitoring database – capabilities previously reserved only for high-end desktops. With analysis tools and automated diagnostics onboard, the user enjoys a tremendous advantage in obtaining immediate answers while in the field.
“With today’s versatile and portable data collection systems, we’re basically doing EKGs on machines,” notes Lofall. “Just like when you go to the doctor, an EKG will detect any early problems. Similarly, machines will give off precursors, or early indicators, of future problems.
Enhanced processing tools
The next-greatest boon for plant managers can be attributed to the manner in which this data is now processed with almost real-time speed to deliver intelligent answers regarding machine condition.
For instance, Azima DLI’s vibration analysis software uses an empirical, rule-based logic system that utilizes order-normalized data, spectrum analysis, cepstrum analysis, demodulated data analysis, and other proprietary algorithms to deliver information with an emphasis on providing a straightforward user interface. All data and functions are made available from a single-layer intuitive screen that is quickly organized via a built-in setup wizard.
“If you have a failing machine, then today’s software can tell you the severity with a hierarchy rating system, like a five out of 10,” says Lofall. “It’ll give you the actual fault or faults. It might be a bad roller bearing in addition to an imbalance. It should also tell you the repair recommendation based on whatever faults it finds.
That is why the system is so useful to plant managers; they don’t necessarily need to get into all the details. The system automatically does that for them by simply presenting credible information upon which they can base their decisions.”
The real dollars-and-cents gains of utilizing PdM software come from employing these systems to continuously evaluate machine conditions.
“With continuous monitoring, an engineer can keep a much closer eye on operations, which brings about the real savings of predictive maintenance,” says Lofall. “For example, there always will be a small percentage of machines, say 4 to 5 percent, where you can see that it is not even going to last six months down the road.
So you had better take care of any problems immediately. On the other hand, the most common thing we note is that most machines are running just fine. That’s important, because without such predictive information a lot of people would tear down the machine every three years just based on the calendar. But the PdM software would indicate that this machine is still doing fine; no repairs are needed.”
Gains in integration
While maintenance success stories rely on ever-more powerful data collection and process tools, the breakthrough benefits result from the integration of this important maintenance data into one seamless source of concise information.
For example, Azima DLI’s Voyager is an integrated environment that combines vibration analysis, used-lubricant analysis, infrared thermography libraries and even visual inspections (input via portable data collection instruments) to provide a single view of the maintenance status of a plant’s machinery. By utilizing one common platform to combine and compare various data sources, a cross-technology scoring can be achieved.
This yields a prioritized ranking so that facility managers can schedule plant-wide repairs in order of urgency. Reports can be customized to include detailed plots and images to justify comprehensive, program-management decisions.
Integration of PdM software recently proved itself at Tri-State Generation & Transmission’s Escalante generation station. Azima’s vibration diagnostic software, ExpertALERT for Voyager (EAV), recently saved Tri-State money by taking machines out of service for necessary repairs based on their condition instead of waiting until they fail, but it was the thorough dissemination of this information that helped make the program a success, according to Joe DeSoto, a results specialist at Tri-State.
“The DLI Diagnostic Data Collector includes EAV on a tablet-style computer platform that you can take out of the office,” says DeSoto. “It shows your maintenance people what’s happening to the machine in real time and helps explain where the problem is and why.”
DeSoto stresses that providing such information on the production floor is crucial to gaining the confidence of the maintenance staff. Showing them ExpertALERT’s diagnostic capabilities in action helped develop trust in the tool throughout the facility and boosted the credibility of the entire PdM program.
Advances in communications
“All hardware products should use a common software and database platform, so they can pass along and process information seamlessly,” suggests Lofall. “However, establishing common lines of communication with the business system of any given plant is becoming just as important. This type of information-distribution is now expected in the very latest iterations of PdM software.”
In essence, the latest PdM communication tools excel at “bringing the mountain to Mohammed” by abstracting data from insular condition monitoring applications, and then placing it at the feet of maintenance decision-makers.
“Today’s new networking technologies offer more power and transparency,” notes Lofall. “XML, OPC and Microsoft’s DCOM and .NET are breaking down the barriers of integration and distributed computing.”
For instance, in conjunction with diagnostic software, Azima DLI’s online software permits facility managers to ascertain the status of wired machinery simply by logging onto their network to view real-time vibration data or obtain a complete diagnostic analysis. Under such topology, the online system is simply another node on the plant’s LAN. An Active-X component can even be installed on selected computers so that maintenance alert messages automatically pop-up on the screen. Additionally, electronic “in-trays” can be configured so that only the status of critical, process machines will be delivered to the user.
“Connectivity is a big part of making PdM pay for itself, as it doesn’t do any good to have the information unless it gets to the right people,” says Lofall. “Certainly, the bulk of managers still get written reports, but now we have the technology to send results over the Internet and through electronic wireless connections like digital cell phones and pagers.”
Taking things a step further, Azima DLI offers a unique means of distributing maintenance information by automatically generating machine status summaries in HTML, so that these pages can be accessed via a common Web browser. This allows a traveling engineer to determine machine status, even from outside the company WAN.
Modern PdM communication software also allows a significant amount of customization.
“With today’s systems, you could get the condition of a machine right on your digital pager or cell phone with a text message,” adds Lofall. “Or, you could set it up so that your cell phone would ring every time a machine of your particular interest, reached a critical state of maintenance need. To go another step further, different ring tones can be assigned to different incoming numbers, so an engineer can immediately tell which piece of equipment needs attention. It’s simply a matter of preference.”
These improvements in communication are even becoming available to small organizations that lack integrated business systems. Azima DLI, for instance, operates an online monitoring center on a 24/7 basis, providing worldwide coverage of wired machines. The monitoring program can be set up to deliver maintenance information over a wide range of time frames, from monthly reports all the way to immediate-alert messages.
The future
And so, the story of PdM has come a long way from the early days of RTF. Innovative PdM tools now help engineers accurately track the condition of their assets, whether they’re using a stand-alone PC system in a small job shop or an enterprise-wide system for a multi-plant industry.
DaimlerChrysler’s Kulczak summed up the modern state of affairs when he observed, “RTF is not only just a memory, but an impossibility here. We simply can’t afford to do that. For us, PdM software proved to be a very useful tool.”
Because today’s modern PdM systems enable increased uptime, energy savings, and reduced maintenance costs for organizations of all sizes, it has earned recognition as a contributor to profitability. Those plant engineers who have taken the next step from time-based or reactive drills to proactive condition-based planning on both existing and newequipment, are laying the groundwork for even further advances within the field of maintenance management.
For more information about Azima DLI and its line of predictive maintenance products and services, visit www.azimadli.com or call 800-482-2290.
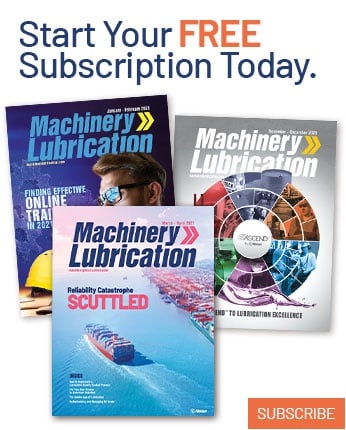