Being one of the biggest single container terminals in the world brings certain expectations from the operators and customers alike. Professionalism, reliability and efficiency are three of the most important and, coupled with a high regard for safety, are major focus areas for the Yantian International Container Terminal (YICT), in Shenzhen, southern China.
With 74 mammoth sized cranes lining the five deep water berths and about 10 million 20-foot equivalent unit (TEU) containers a year coming in and out of the terminal, it is an extremely complex task to keep everything running smoothly and safely. But the management of YICT have followed a Total Quality approach to their terminal from the early planning stages through the construction phase and into the running of daily operations.
Today, Six Sigma is a guiding tool for process improvement to many things, including the entire maintenance strategy and operations, and their Quay Crane maintenance manager is a Six Sigma black belt. At the YICT Engineering Control Centre he has an ultra modern overview, via CCTV and other monitoring technologies, of many of the equipments and machinery, down to individual electric motors, needed to keep the terminal operating 24 hours round the clock .
Wide-ranging maintenance strategy
YICT has applied and included all the various technique and technology in their maintenance strategy starting with time based, then adding condition-based (CBM) and Reliability-Centered Maintenance (RCM) that now ensure the right balance, from a cost and effectiveness viewpoint, for the vast array of equipment and systems under his supervision.
One example the company gives is that a CBM approach to a particular gearbox allowed a solution to be made within 2 weeks, compared to 2 months at a port where a similar gearbox, operating on a time based maintenance program, failed unexpectedly. So although they had a potential failure to deal with, the financial and operational damage was only one quarter of that experienced at another port.
One of the ultimate techniques within a CBM and RCM program is continuous online monitoring, implying that the earliest signs of potential failure are recognized, and fast and adequate corrective action can be taken. It is not the answer to all maintenance concerns, but used wisely it is a very good investment to protect operationally critical or safety critical equipment.
And this is an area that YICT has been moving into regarding their quayside cranes. They have now completed a three-year test period with SKF online monitoring technology on gearboxes on two cranes.
Safety – a key concern
The monitored gearboxes are positioned 100 meters above ground in the ‘workhouse’ of the huge dockside cranes. The gearboxes drive the roll drums that lower the heavy duty wire cable that is used to lift the heavy containers on and off the ships and container transport lorries.
The number one concern here is safety. A sudden failure or seizure of a gearbox could cause a container to swing away from its intended path of movement or drop some meters before the automatic braking system could hold the cable and container in place.
With so many people constantly moving around the terminal such gearbox failures are a high priority to avoid. Additionally with a ‘suspended’ container and an “out of commission” crane, there would be the loss of productive and throughput capacity to the terminal operators, the container owners and the end customers, who are waiting for the container goods to be delivered.
Critical components continuously monitored
A major potential cause of gearbox failure is some kind of failure of the bearings that support the gear shafts. Although bearings are high performing mechanical systems, like all machine components and systems they can wear or become damaged over time depending on various conditions of operation, loading, operating environment, etc. If left too long before replacement a catastrophic bearing failure can result that could lead to a gearbox failure and the potential dangers mentioned earlier.
The SKF online system monitors the health of the gear shaft support bearings via vibration sensors placed at specific places on the outside of the gearbox housing. Bearings have particular vibration “signatures” when working well, working poorly or suffering from wear. And these signatures differ for different bearing types, sizes and loading conditions.
So it is important to “trend” and study each bearing and its operating cycle separately to get a reliable picture of the health of each one. To do this, vibration data is sent to and stored on a server in the Engineering Control Center for later analysis.
By constantly monitoring the vibration signals YICT has been able to confidently asses the health of the bearings and, with it, the potential of increasing or excessive bearing wear and associated gearbox failure. So far they have been able to happily continue running the gearboxes and no failures have occurred.
Because the loading and speed conditions of the gearbox varies during operation it requires special skills and knowledge to interpret the vibration signals correctly.
SKF provided close support and advice to YICT engineers during the first year of running and remained on-hand during the next two years of operation. Additionally, YICT engineers attended SKF courses on condition monitoring to improve the own knowledge and skills levels.
Moving on with confidence
Equipped now with fully trained condition monitoring engineers and three years confident experience, YICT is keen to expand the condition monitoring to more cranes and will investigate SKF’s latest technology.
With 32 analogue channels and 16 digital channels, the new system will allow bearing, gearboxes and motors to be monitored at the same time, saving a lot of maintenance costs in the process. And this will be another step in YICT’s continuous process improvement Six Sigma-driven program that delivers professionalism, reliability, efficiency and safety to its port’s machinery and its customers.
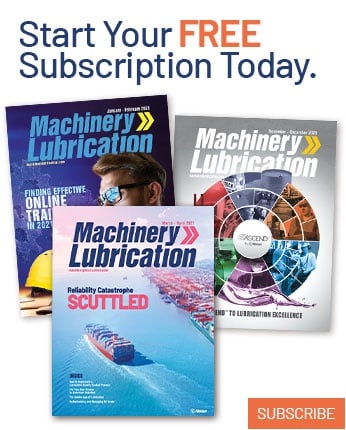