In 1838, the Martin family began dyeing and finishing canvas for applications such as luggage, awnings, boxing ring covers, theater curtains, hunting apparel and medical bandages. To satisfy so many different customers, the family’s company has designed and built a wide range of custom machinery. But when a machine breaks down, Martin Corporation engineers and technicians cannot simply call in a service engineer from the manufacturer. They must fix it themselves, as soon as possible.
The Martin Corporation has been passed from father to son for nearly two centuries. It was founded in Philadelphia and moved to its current location in Bridgeton, N.J., in 1949. Plant engineer Thomas Martin, son of the current owner, states that the company has long developed its own production equipment. That’s partly because the machinery can be customized to exactly fit its production needs, and also because the company dyes and finishes canvas for a wide variety of applications, many in niche markets. Thus, its equipment requires a level of flexibility that most equipment suppliers overlook in favor of designing more specialized machines.
“The fact that most of our production equipment has been engineered and manufactured in-house has allowed us to remain flexible to our customers’ needs and competitive in the very challenging global textile market,” Martin said.
The company’s dyeing machines, or jigs, have two rollers that move the fabric back and forth as it passes through a bath of dye liquor or washing solution at a speed of 150 to 250 yards per minute. “Some of our machines date back to the 1950s, but we are continually upgrading ... their control and actuation systems,” Martin said. Each roller is powered by a hydraulic motor with electrohydraulic controls. Electric motors are used to drive the pumps that power the hydraulic system. The electric motors are controlled by variable frequency inverter drives, and the hydraulic pumps are controlled by electronic displacement controllers (EDCs) with ramp functions that prevent the rollers from being started or stopped too quickly. Encoders are integrated into the rollers to provide feedback to the EDCs.
Figure 1. The textiles plant has many motors, and they all get serviced and rebuilt in the in-house shop. Tom Martin uses the Fluke 1587 Digital Insulation Multimeter to test the motor’s internal windings and check their condition.
You break it, you own it
Of course, the fact that the company builds its own equipment means that it bears complete responsibility for maintenance and repairs.
“We have always had an exceptionally large maintenance department,” Martin said. “Our equipment operates continuously under very demanding conditions – including corrosive liquids, high temperatures and high levels of humidity – so breakdowns are a regular occurrence. And even when something is not broken, our maintenance department is busy trying to improve it.”
The company’s early efforts to automate its equipment failed, in Martin’s opinion, because the company did not have the expertise to troubleshoot equipment in a timely manner.
“Fixing broken production equipment does not satisfy customer orders, so for a long time, automation and electrical improvements were put on the back burner to improving overall mechanical reliability,” Martin said.
To keep production rolling, the maintenance staff would override the automation systems so production could continue. Then, approximately five years ago, Martin took over responsibility for maintenance of the electrical system and initiated new electrical troubleshooting methods that have greatly improved the plant machinery’s electrical reliability – and the company’s ability to quickly and effectively troubleshoot and resolve problems as they arise.
Figure 2. Martin uses the new Fluke 233’s remote display to look at the supply voltage of one of the drive motors on the textile spooling machine. The remote display allows him to work at a safe distance from the moving machine parts and live voltage. To operate this machine and monitor live voltage would have been a two-person job in the past.
‘Seeing’ electricity
“I by no means consider myself a professional skilled test tool user, but rather a mechanical engineer who relies on my test tools to ‘see’ electricity,” Martin said. “I use Fluke tools because they work so well. Most of the measurements we take arise in the process of solving problems or making an improvement. Now, when a machine stops operating because of a control system problem, instead of just overriding the system and operating the machine manually, I begin a troubleshooting process with the confidence that we can get the machine back into full automated operation quickly enough to avoid affecting our production targets. It is much more productive to troubleshoot and resolve a problem than to override automation – making changes that will need to be reversed when the actual problem is addressed.”
Martin typically begins by looking at the minus-200- to plus-200-milliamp signal that controls the servo on the hydraulic pump.
“The Fluke 337 Clamp Meter is the first tool I use when, for example, an operator tells me that a machine seems to be slowing down, even though he has not touched the controls,” Martin said. “I throw it around the wire on the servo. If the servo is receiving current, this indicates the problem is in the servo or the pump. If the servo is not receiving current, then the problem is upstream, in the control system or wiring. In a matter of seconds, I can identify the general area of the problem. I can move the meter to the electric motor that drives the hydraulic pumps, and the amp reading gives me a general scale of how much tension the fabric is under. If the amperage is high, I would start looking for a mechanical problem, such as a bad bearing. If it is low, I would immediately suspect a problem in the control system.”
If the servo and pump are ruled out, Martin uses a Fluke 189 digital multimeter (DMM) to check the EDC. “I am waiting to replace the 189 with a 289, but it will just not die,” Martin laughed. He checks the output of the EDC to see if it is delivering a run signal. If so, then the problem most likely lies in the wiring between the EDC and servo. The next step is usually checking the resistor-capacitor circuit that ramps the EDC signal. He measures the capacitor and resistor with the 189, too.
Figure 3. Martin uses the Fluke 568 to look at the temperature of the drying drums in between fabric runs. The operator can dial in the temperature on the cans by setting the steam pressure. The typical temperature range is 215 to 275 degrees Fahrenheit.
The jig operator control panel also controls a number of electronic solenoid-operated water valves on each machine that deliver hot and cold water to the baths and provide cooling water to the hydraulic system. The valves have an internal pilot valve that opens and closes a small orifice that in turn opens and closes the main valve.
“In the past, we had no way to diagnose problems in the valves, so we would usually replace the whole valve and take it back to the shop for more extensive testing,” Martin recalled. “This involved a considerable amount of downtime. Now we can diagnose the valves in place and, in most cases, fix them with much less downtime because the min/max mode of the 189 is fast enough to provide a meaningful measurement of the voltage transient of the valves.”
For example, the valves sometimes get stuck in the on or off position. Martin troubleshoots that problem by energizing the valve that he wants to open or close and then uses a 189 DMM to measure the peak of the voltage transient when the valve is de-energized. “These are 24-volt AC coils, and when a valve is working properly, there is typically only a measurable transient peak of 80 volts AC,” he said.
The mechanical movement of the pilot inside the valve prolongs the transient spike but reduces the peak voltage measured. When the 189 indicates, for example, that the maximum voltage is 170 volts AC, it is a clear indication of a mechanical problem on the pilot side of the valve.
“While, at first, even I thought measuring the transient spike was a useless measurement except for designing suppression circuitry, my 189 has proved to me that it has the performance and repeatability to provide meaningful information that can be used to troubleshoot mechanical performance inside a solenoid valve,” Martin said. “That one strange measurement has completely changed our ability to troubleshoot, diagnose and repair installed solenoid valves throughout the entire plant.”
Recently, two temperature controllers failed. Operators normally address this type of failure by powering the controller down and sending an on/off signal to the steam valve operators manually. Instead, Martin used a Fluke 1587 Digital Insulation Multimeter to perform low-voltage insulation tests. These showed that the units were not shorted; rather, the problem was isolated to a single card that could easily be exchanged.
Martin uses a Fluke VoltAlert to check whether wires are live or dead for personal protection before starting many troubleshooting tasks. He also uses the 189 meter for troubleshooting the variable frequency drives on pumps, electric solenoid valves and level sensors in the system used for recovering heat from the plant’s wastewater.
Figure 4. Martin uses the 773 Milliamp Process Clamp Meter to check the 4 mA to 20 mA signal between an electronic temperature controller and an electric-to-pneumatic pressure transducer that operates a steam valve. He compares the output percentage reading on the 773 with the output that the electronic controller displays in a diagnostics mode.
Automation closes the loop
Martin wants to incorporate more automation into the production equipment. He is developing a PC-based control system for the entire plant and all production equipment. The company has already installed humidity sensors to provide data for the new system. To calibrate and troubleshoot the sensors, Martin purchased a Fluke 971 Temperature Humidity Meter. “The 971 has quickly become a valuable tool for monitoring electrical enclosure temperatures,” he said.
Martin views a PC-based system as the way to close the loop between the company’s production equipment and wastewater heat recovery systems.
“I am designing the system to be easy to override in a non-permanent way to allow production equipment to operate reliably in a state with automation bypasses,” he said. “I decided a PC-based control solution was the best way to integrate multiple systems with quick and easy logic adjustments or overrides, without the need for physical wiring changes.”
Martin said he wouldn’t have been able to implement such a system without the ability to accurately and efficiently diagnose electrical problems. “Fluke meters fulfill that need and provide a window into what is going on at the plant. They provide a visibility that enables me to quickly diagnose problems and then direct others to solve them. This saves the maintenance team time and, more importantly, enables us to keep production machinery operating with minimal interruptions to achieve higher levels of throughput and quality.”
His most recent controls investment? The new Fluke 773 Milliamp Process Clamp Meter, for troubleshooting 4 mA to 20 mA signals. “While I previously had to break the circuit and use my DMM for inline current measurement, the clamp meter is a really slick little tool that definitely gets the job done.”
For more information, visit the Fluke Corporation Web site at www.fluke.com.
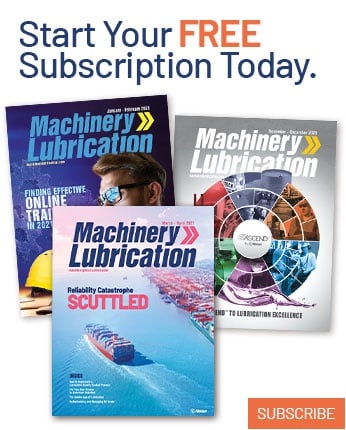