Brian Kenny, the plant manager of Paulco, teetered on the middle of a big picket fence. When does a career-making challenge turn into a career-limiting problem? Recently, he and plant lean principles expert Linda Amoroso had been charged with finding ways to increase site output 15 percent to cover a sudden sales upside opportunity.
There were four little things getting in the way:
-
They were maxed out on equipment output.
-
There was no time to buy equipment.
-
There was no time to hire and train new people.
-
The increased shipments needed to start within a month.
Other than that, they were in great shape.
"Fifteen percent is a lot," exclaimed Brian. "It's not like we're dogging it now. Everything and everyone I have is giving their all."
"I know it seems like a big hurdle," replied Linda, "but there is hope. We already decided that the Finntronics equipment was the main focus since it is the true bottleneck (see Part 2, in the July/August 2007 issue, at www.reliableplant.com). However, based on the floor diagnostic study I did a few days ago, there is waste that we can cut."
Linda showed Brian the results of her floor study (Figure 1).
Figure 1. Finntronics Floor Study Results: Percent of Total Time
"Wow!" yawped Brian. "I'm getting hungry looking at that pie … and I'm absolutely salivating at the Availability Waste slice! Let's eat that one first."
"Agreed," replied Linda. "But, let me show you some more detail (Figure 2) so that we'll know exactly where to go. You see, we spend an awful lot of downtime (44 percent) in conversion setup."
Figure 2. Downtime Components as Percent of Total Downtime
"Of course, we do," rejoined Brian. "We have many products run through the Finntronics in a given day. You're not suggesting limiting our product line, are you?"
"No, no, nothing of the kind," responded Linda. "It's not the number of conversions we do, it's the time it takes to do them. That is what we must attack. In past projects that I have led, when we apply lean principles to setup reduction, we often save 50 percent of the setup time. And, look at this equipment qualification data. That category accounts for 17 percent of our downtime."
"Hold on to your horses. That's a quality issue. We are not cutting there," asserted Brian.
"Is it?" said Linda. "When was that qualification instituted? Don't we have other product and machine measures during our process to ensure that the equipment is not drifting or producing bad product?"
"Yes, I suppose we do," offered Brian. "We put in that qualification step when we installed the machines because there were some start-up problems. I guess we never stopped it. And, yes, we do constantly check our product and equipment quality, so I see your point. Why do we need to qual every shift?"
"Exactly. So, now let's look at preventive maintenance."
"Whoa, partner!" interjected Brian. "Open any book on maintenance and they will tell you that PM is vital. Do it early and often."
"Well, you're certainly right," acknowledged Linda. "I have looked in some books from the 1980s that told me just that. Yes, we need to prevent episodes of corrective maintenance, but can we change the way that we do and trigger preventive maintenance? Do we need to do weekly and daily PMs like clockwork? Are they helping us reduce overall downtime? Are they taking too long? Maybe if we monitored the condition of equipment parameters, process outcomes, use hours, failure patterns and so on, we could more effectively use preventive maintenance. You know, it could be more condition-based. And, with conversion reduction techniques, we could also reduce PM time when we do choose to do it.
"So, now let's look at the last piece, corrective maintenance, at 21 percent. Do we know how much of that time is actual wrench repair time?"
"Well, sure," replied Brian, "You just said 21 percent."
"That is only one part of downtime," continued Linda. "What about the time to do root cause diagnosis, or the time to re-commission, or the time to recognize the equipment is down, or the time to respond once it is recognized? When we can break maintenance into the 5Rs - for recognize, respond, root cause, repair and recommission - then we can pinpoint effective action.
"Now, look at this (Figure 3). This shows our downtime by equipment copy. See anything funny?"
Figure 3. Down Hours by Individual Equipment
"Yes," said Brian. "Look at this. Three of the four Finntronics are about equal - but Finn 2 is much higher in PM and corrective hours. Hey, wait a minute … that's the one we put in late. There was no more room, so we placed it in another part of the building. Could there be some 5R issues there?"
"Sure, and possibly some training or procedural issues as well," stated Linda.
"Well, this all is great!" Brian exhaled a big sigh of relief. "Since availability is 14 percent of total lost time and we can fix all the downtime, I've only got 1 percent to go to make the 15 percent! Let's take it to the bank!"
"Well," said Linda hesitantly, "it's not that easy. I'm projecting we can cut maybe half of the availability loss. That leaves us with 7 to 8 percent to go. Tomorrow, let's talk 'speed loss'."
Mike Verdin is a principal with Aveus, a global strategy and operational change firm located in St. Paul, Minn. Contact him at 480-231-3368 or at mverdin@aveus.com. To learn more, visit www.aveus.com.
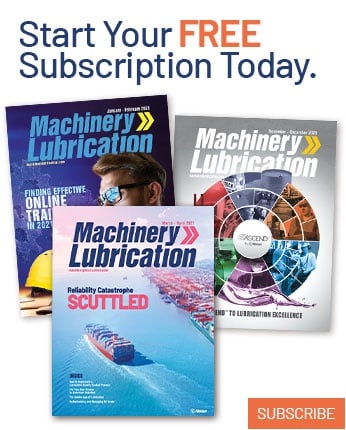