Let us share a few words about wrench time: What is it? Why is it important? And, how do we measure it?
What is wrench time?
Wrench time is a measure of crafts personnel at work, using tools, in front of jobs. Wrench time does not include obtaining parts, tools or instructions, or the travel associated with those tasks. It does not include traveling to or from jobs. It does not include time spent obtaining work assignments.
Obviously, it does not include break time. These non-wrench time tasks are often necessary to get work done, but are not "wrench time." The craftsperson is in a delay situation. We should also ask ourselves whether the crafts personnel perform tasks efficiently while they are on tools in front of jobs. This is a legitimate question, but not answered by wrench time. Nonetheless, if we increase the time employees are "on the job," we should get more work done.
In addition, planning should increase the efficiency of a craftsperson while on a job if the plan provides helpful instructions and provides a time standard for a good technician performing the expected work without unanticipated delays.
To define something as wrench time or not, I find it helpful to consider what I would be willing to pay for if I hired someone to do a job. Would I be willing to pay for someone getting a part? No, I would have wanted them to have that part available to begin with.
Why is wrench time important?
Industry experience shows that typical workforce wrench time is between 25 and 35 percent. Planning and scheduling can help raise this rate above 50 percent. One of my earlier Reliable Plant columns stated what this means in monetary terms. For now, accept that increasing a workforce at 25 percent up to 50 percent would double the labor. A 30-person workforce would perform the work of 60 people. You can see this is a vital issue.
My sixth principle of planning states that wrench time is the primary measure of planning and scheduling effectiveness. The purpose of planning and scheduling is to increase productivity. It's not to prepare job plans or operate the CMMS. Planners might prepare job plans or operate the CMMS, but that's not the purpose of planning. The job plans and CMMS help the planners in their goal to increase productivity. Wrench time best measures this productivity.
How do we measure wrench time?
Before we discuss how to measure wrench time, let me first say that formally measuring wrench time isn't a requirement to implement helpful planning and scheduling. Wrench time studies are easily seen as obtrusive and heavy-handed. Implementing a fundamentally sound system that plans most of the work and schedules each crew with a weekly goal of work improves wrench time whether it is measured or not. In addition, the metric of work orders completed per month shows a dramatic increase when the scheduling effort takes off.
Nonetheless, plants can measure wrench time in-house with reasonable accuracy with a limited number of days and in a manner acceptable to crafts personnel. First, use an agreeable, in-house supervisor as the observer who knows everyone. This avoids putting numbers on hats or other perceived demeaning methods to identify people.
Second, announce the study ahead of time to the crafts during breaks or other convenient settings. Frame the observations as finding out what delays are hindering work, not as measuring whether people are lazy.
Third, use a sampling method, sequential or random, to insure each person has an equal chance of selection.
Fourth, five days of sampling two people each half-hour of an eight-hour shift produce accurate enough results to confirm a 35 percent wrench time with a plus or minus 7 percent accuracy. Often, this result makes the study worthwhile as the plant discovers it does not have 80 percent wrench time as commonly thought. Plus or minus 7 percent is also accurate to confirm a productivity increase.
A plant might move from a range of 28 to 42 percent to a range of 43 to 57 percent, a definite improvement. (Certain statistical tests also exist to confirm improvement even if the ranges overlapped.) In addition, a study would quantify delays such as parts, tools, instructions, traveling, etc. with better accuracy than plus or minus 7 percent because delay areas are smaller. E-mail me to receive a sample wrench time study that compares delay areas. If you just have to do a wrench time study, I'd recommend such a mini-study.
Doc Palmer is the author of the “Maintenance Planning and Scheduling Handbook.” He is a CMRP and has nearly 25 years of industrial experience as a practitioner within the maintenance department of a major electric utility. From 1990 through 1994, he was responsible for overhauling the existing maintenance planning organization. The resulting success played a role in expanding planning to all crafts and stations owned and operated by the utility.
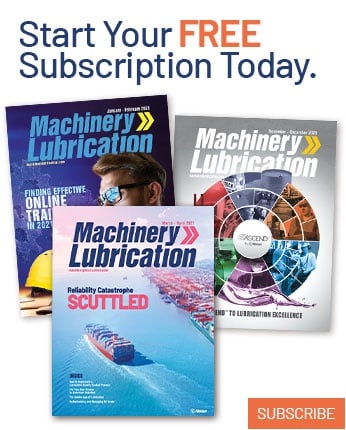