Here is a problem I discovered on a recent gemba walk. After I noticed a damaged box with components spilled onto the floor, I called the first employee I saw, a warehouse team leader, to show him. He looked at me with mixed emotions that I took for a combination of mainly embarrassment (since I found something wrong in his area), a bit of grief (here’s another problem to deal with first thing in the morning) and a dose of frustration (this was not a planned action item on today’s to-do list). More than likely, he was also little angry, however he did not show any of it to me.
So, can you guess his response?
A) “I didn’t do it, it must have happened on second shift.”
B) “I’ll find out who did it and fire the #^@%*$!”
C) “I am so sorry. I’ll get it cleaned up immediately”
D) “It happens all the time, but it’s not a big problem.”
E) All of the above.
While I have heard all of these responses, in one form or another, many times before in my manufacturing experience, Answer C is the most common response. Most employees will promptly get help to salvage the parts and clean up the mess as soon as possible. Once the mess gets straightened out, the problem is solved and we get back to manufacturing our products.
But was the problem really solved?
Well, that depends on your idea of the problem and your definition of solved. Yes, the mess was a problem and, yes, the mess got cleaned up, which is the proper initial action.
However, the true problem I discovered on my gemba walk was not a damaged box in a warehouse. The true problem is that our response was only reactive and failed to include any real corrective or preventive actions, not to mention failing to record the damaged box condition (for kaizen). We think that simply cleaning up the mess quickly and scraping out the parts is all that is needed. In effect, the problem of box damage remains hidden.
We did not ask the five whys. We did not list the broken box on a kaizen newspaper. We did not look for other damaged conditions in the warehouse. We did not change a single process. There was no kaizen, so we are doomed to repeat this cycle another day, over and over again.
How would employees in your company respond? Are you doomed to repeat the same cycle?
About the author:
Mike Wroblewski started his lean journey with instruction in quick die change from Shigeo Shingo. Mike is president of Victory Alliance Technologies, a Greensburg, Ind., firm that specializes in lean implementation. He writes a blog called "Got Boondoggle?" featuring lean and Six Sigma topics. Mike can be reached by e-mail at mwroblewski@victory-alliance.com.
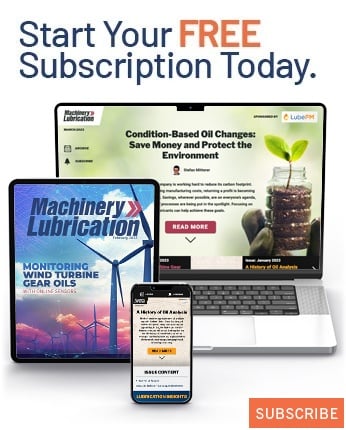