Embracing Change: A Necessity in the Modern Industrial Landscape
Key Strategies for Embracing Change
- Continuous Learning and Development: To stay ahead of the curve, professionals must commit to ongoing education. This includes attending industry conferences, participating in training programs, and staying informed about the latest research and development in lubrication technologies.
- Implementing Predictive Maintenance: Predictive maintenance technologies, such as condition monitoring and oil analysis, allow for the early detection of potential issues, reducing unplanned downtime and extending the life of machinery. This proactive approach saves costs and supports sustainability by reducing waste and conserving resources.
- Collaboration Across Departments: Change often requires breaking down silos within an organization. Maintenance and reliability teams should work closely with environmental, safety, and operational departments to ensure that changes are implemented effectively and sustainably.
The Role of Sustainability in Maintenance and Reliability
- Selecting Environmentally Friendly Lubricants: The choice of lubricant plays a significant role in sustainability. Biodegradable and non-toxic lubricants are increasingly being used to minimize environmental impact. These lubricants reduce the risk of contamination and are often derived from renewable resources, making them a more sustainable choice.
- Extending Lubricant Life: Proper storage, handling, and filtration practices can significantly reduce waste by maximizing the life of lubricants. Advanced filtration systems, for example, can remove contaminants and extend the life of lubricants, reducing the need for frequent oil changes and disposal.
- Reducing Energy Consumption: Proper lubrication can reduce friction, lowering energy consumption. This leads to cost savings and contributes to a company's overall sustainability goals by reducing its carbon footprint.
The Interconnection of Change and Sustainability
Overcoming Challenges
Steps to Overcome Challenges:
- Leadership Commitment: Change starts at the top. Leaders must demonstrate a commitment to change and sustainability by setting clear goals, providing the necessary resources, and recognizing and rewarding successful initiatives.
- Employee Engagement: Engaging employees at all levels is crucial. Providing training, encouraging feedback, and involving employees in decision-making can help reduce resistance and ensure that changes are implemented smoothly.
- Long-Term Vision: It's easy to get caught up in the immediate pressures of the business, but sustainability requires a long-term perspective. Companies should set ambitious sustainability goals and continuously monitor their progress to ensure they are on track.
Conclusion
Supplier Spotlight
Noria Academy 1328 E. 43rd Court, Tulsa, OK 74105 800-597-5460 | Noria.com/Academy
Obtaining certification can be a challenge; new terms, concepts and topics can overwhelm even the most experienced reliability professionals. Training experts all agree that extending the learning beyond the classroom dramatically increases knowledge retention. To aid in this retention and create an innovative student experience, Noria is pleased to offer the Noria Academy app.
RelaWorks 1328 E. 43rd Court, Tulsa, OK 74145 918-392-5058 | RelaWorks.com
Finding the right products can be difficult. Every industry and application is unique. Over-spending and guess work is common. At RelaWorks, we help reliability professionals solve this challenge. Our mission is to provide products for your unique needs and budget. Backed by Noria Corporation’s expertise and legendary customer service, we’re excited to help your reliability program succeed.
LubePM 1328 E. 43rd Court, Tulsa, OK 74105 800-597-5460 | LubePM.com
As a Lubrication Management System (LMS) engineered by lubrication professionals, LubePM helps an organization create accountability to ensure that every lubrication point is carefully maintained, inspected and measured. Ready to take your facility’s Lubrication Management System to the next level with LubePM? We’re ready to help. Simply request more information or schedule a demo.
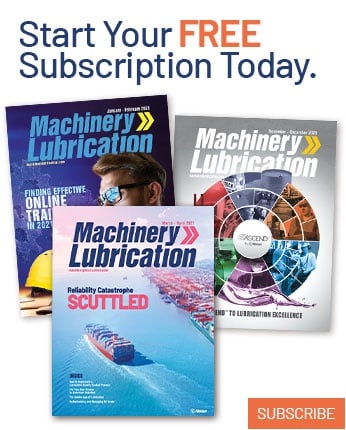