Foam materials made from rubber and plastics are a ubiquitous part of modern life, serving as indispensable components in everything from advanced medical and aerospace applications to everyday consumer items. A wide variety of foam materials has been developed that effectively and reliably serve many different functions, including sealing, temperature insulation, sound attenuation, vibration damping and shock absorption.
However, when foam products fail, it may not be because of a deficiency of the foam material, but because of problems with the adhesive system. All too frequently, adhesives do not stand up to the rigors of the end-use application, or they break down during transport and storage, prior to the foam component being finally affixed. Inadequate adhesive systems also cause problems during the fabrication and conversion of foam products, resulting in product damage and waste, and in disruptions of the manufacturing process.
Engineering a reliable adhesive system is not easy. Imagine a foam component that is die-cut from a sheet that must lay flat and remain in place while being transported a thousand miles in a hot, humid truck. Then imagine that the release liner on the foam component must remain intact until it is removed from the foam part and the part affixed to a car door, where it must resist grease, solvents and ultraviolet light, as well as the stress of the door being slammed hundreds of times at 40 degrees below zero.
Engineering a Reliable Adhesive System
Typically, production engineers and product designers will select foam material(s) and then subsequently seek an adhesive system that works with the chosen material. Foam manufacturers may recommend a type of adhesive for each of their products, but unfortunately, in practice, there are no “one size fits all” solutions that will work for all applications of a particular foam material.
Many factors must be considered when engineering an adhesive systems, including the chemical composition and mechanical properties of the foam(s) and all other substrates that will be bonded – which could be anything from glass, plastic, metal or painted surfaces to human skin. Of course, the adhesive system must be designed to meet the particular performance requirements and environmental conditions of the end-use application.
The engineering of foam adhesive systems is further complicated by the fact that most foam applications require one or more release liners to protect the adhesive during transport and storage, and during the various converting and assembly processes. Engineering the release liner system can be a notoriously difficult balancing act, because release liners, by design, are only temporarily affixed, and they are subjected to conflicting demands.
On one hand, release liners must remain securely attached during interim stages of the process, but on the other hand, they must be easily removed at a later stage. In other words, the system must have a so-called “tight release” during various laminating, printing and cutting operations, as well as during transportation and storage, but conversely, they must also have a sufficiently “easy release” to enable automated or manual removal. In some cases, the release must also be engineered to be easy enough so as to avoid damage to fragile foams like melamine when the liner is removed.
The Challenges of Foam Substrates
The engineering of an adhesive system starts with the analysis of the foam materials. A large variety of foam materials are available and new formulations are continually introduced: melamine foams for thermal barriers, low permeability urethane foam for automotive HVAC applications, polypropylene foam for medical diagnostic pads, EPS and cross-linked PE foams for engineered packaging, PE foams for construction applications, and PVC foams for sound attenuation and vibration damping.
Various types of foam place different demands of the adhesive systems. Surface texture ranges from smooth to rough. Foams with low surface energy, such polyethylene, polypropylene and many extruded foam products, have a slippery, smooth surface and require special adhesives for bonding. For such materials, it is sometimes necessary to utilize surfaces treatments such as abrading or corona treating to enable a good bond.
Sometimes converters want to bond to “skived” foam where the cellular structure of the foam is exposed and other times they want to bond to the “skin” of the foam. Skived foam represents additional challenges as there is less surface area for the adhesive to contact and the adhesive will tend to “bridge” over the open cell structure.
Foam with the skin intact presents its own set of issues. The skin may contain release agents or other surface contaminants that can interfere with the ability of the adhesive to bond effectively. The skin will also have the highest concentration of ingredients that could migrate to the skin surface and cause bonding problems.
Some adhesive materials contain solvents and monomers that can swell and collapse particular types of foam. Destructive chemical reactions can also occur in the opposite direction, because polymeric materials contain additives that can migrate to the surface and destroy the adhesive bond. Adhesives must be formulated to resist chemical interaction with surfactants, plasticizers, waxes, oils and other substances – sometimes a challenging task as foam manufacturers continually improve and otherwise alter the chemical composition of their products.
Another important factor in engineering an adhesive system is the foam’s compressibility which dictates and limits how much pressure can be applied by the converter when the PSA is applied to the foam and the material travels through the laminating equipment. EPS and other similarly stiff materials hold up to considerable pressure. Many highly compressive foams cannot recover from applied pressure. Other highly compressive materials have good memory characteristics, such as polyethylene foam and can withstand significant pressure.
Selecting the Optimal Adhesive System
With all these factors to consider, designing an adhesive system for foam materials is a complex undertaking that often requires expertise in addition to that of many fabricator/converters and of even the largest foam manufacturers.
A few companies specialize in the development and the production of adhesive systems for foam substrates. One such company, Adchem Corporation, of Riverhead, N.Y., has conducted extensive research and created a matrix rating the performance of more than 20 different formulations of rubber, acrylic and hybrid adhesives, with film, paper and transfer carrier systems, against commercially available foam products, ranging from natural rubber and neoprene, to ester urethane and vinyl nitrile.
Clearly, production engineers and product designers should give as much attention to the selection of the adhesive system as they give to the choice of the foam material.
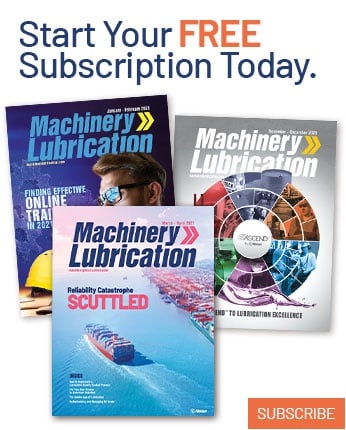