Many people may have gravitated to the maintenance and reliability industry because of the desire to work with machinery. I was trained in engineering and understand how machines operate and work.
Machines behave in logical ways. They all follow the mechanical and electrical laws of nature. Engineers are immersed in those laws in their years of schooling. People in the maintenance field thrive on knowing that machinery works and behaves in logical ways.
In a previous article for Reliable Plant, I pointed out the thought similarities between an organization’s safety improvement effort and a maintenance and reliability improvement effort. The idea that zero injuries are possible is a key concept for any safety effort to gain momentum, but how does a plant or an organization really improve safety results?
What I have experienced over the past 30 years is a continual and steady safety improvement effort. In the early years, much of the emphasis was on identification and elimination of unsafe conditions. The focus was on the machinery and the physical facility. The elimination of unsafe conditions was a normal and comfortable task for many in plant operations, production and maintenance. It was easy to identify and fix defects in machines and facilities that could cause an injury.
Our efforts in these areas were successful and improved safety. However, we still experienced injuries. Many of these injuries were not caused by unsafe conditions but by the unsafe acts of our employees. As our organization recognized this fact, more work and concentration was put on preventing injuries due to unsafe acts.
We have used various programs to improve our results in the past. Several of the programs used were the STOP program and TAKE 2 program, both created by E.I. DuPont.
For the past several years, we used a program that concentrated on people’s behaviors by enlisting these people in observing each other. These observations help remind everyone to think and behave safely. The emphasis was on changing the culture and attitude of the organization as well as on the people and how each person behaves. We have seen substantial improvement in safety results over the past few decades due to this focus.
There is a similarity in leading a maintenance and reliability improvement effort and a safety improvement effort. Today, many of these maintenance and reliability improvement efforts are solely concentrating on the machinery. The program leaders may become enamored with the new technical tools that have exponentially become more capable and less expensive in the past 30 years.
The condition-monitoring tools and precision-maintenance tools have dominated the industry’s attention in the past several years. Many others have focused on the analysis processes such as reliability-centered maintenance and root-cause analysis. All of these tools and programs are fairly technical and logical in nature. The tools and their application are very comfortable to maintenance and reliability leaders, managers and employees.
Certainly, any effort needs to have competency in these technical skills. The need to understand how machinery operates, how it can fail and how to prevent failure is extremely important and foundational to any improvement effort. However, this aspect is the easiest part to lead an organization in the maintenance and reliability improvement effort.
I believe the most difficult but most beneficial aspect of leading the maintenance and reliability improvement effort is managing the change process in organizations. The behavior change process from a reactive state to a proactive state is a challenging transition. Leadership of this change process needs to focus on each employee’s attitudes, beliefs and behaviors.
This certainly is not a comfortable action for most leaders. Employees must believe that machine failures can be prevented by proper design, operation and preventive maintenance strategies. This attitude change is facilitated by continual education on the fundamentals of maintenance and reliability principles.
Over a period of time, success leads the organization eventually to believe that zero failures are possible. When this belief takes hold, the organization begins to accelerate toward a true proactive state. Each person in an organization is important to enlist in this change endeavor. It happens one person at a time through various stimuli.
Changing an organization’s behaviors and actions on a daily basis is one of the key areas that will accelerate the maintenance and reliability process. Are you and your organization’s leaders educated in change management principles and ready for this needed behavior change effort?
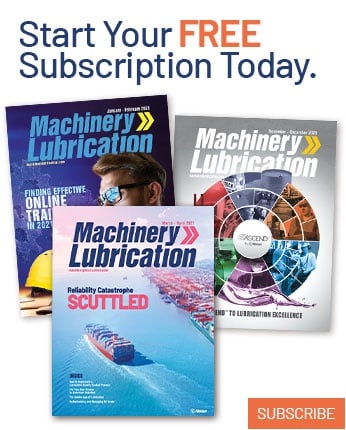