Introduction
Change is often recognized as the only constant, but it’s crucial to understand that successful change is measured by its sustainability. Lasting change depends more on careful planning and intention than merely on the passage of time.
Sustainability requires change, and changes must be maintained to ensure long-term sustainability. A Venn diagram effectively illustrates the interconnected nature of intention, change, and sustainability, showing how these elements overlap to create sustainable intentional change.
Sustaining an implemented change creates a robust foundation for subsequent changes and a conducive environment for continuous improvement. This is the essence of sustainability – not change just for the sake of it.
In industrial settings, implementing changes to assets typically aims to:
- Maximize efficiency
- Improve reliability
- Optimize costs
- Meet regulatory obligations
Areas most often subjected to changes are planning, scheduling, material storage, processes, process environments, and team member coordination.
While intentional changes in these areas can produce desirable outcomes, too often, changes are only temporarily maintained, resulting in regression or a call for another change. Sometimes, these secondary changes cause a facility to revert to old standards. With any of these outcomes, the initial objective of the change is jeopardized.
To understand these challenges, we'll explore common changes in industrial plants, why they often fail, and how to effectively address these issues.
Plans
Changes to plans are more often spoken about than implemented. This results in a partial or disconnected implementation comprising bits and pieces from multiple phases and versions of different plans. Maintenance and production plans are typical examples of this.
Changes driven by consumer preferences, supply chain disruptions, or technological advancements require flexibility. However, the need for structured planning can lead to rigid and hasty decisions. Stockouts and late supplies turn into unplanned production action plans, breakdowns evolve into overhauls, upgrades turn into replacements, and decommissioned items are relied on to save the day.
In this cycle, the solution becomes the problem.
Schedules
A common cause for changes in scheduling is a poor understanding of a problem’s root causes. There is a tendency to increase or alter frequency through broader autonomous maintenance (AM) and tighter preventive maintenance (PM); in most cases, the results are largely undesirable and non-beneficial, creating unnecessary disruptions, over-maintenance, overstocking of spares (high working capital), and poor morale amongst the implementation team.
Alternatively, schedules can be under-delivered, producing detrimental results. While technology has greatly advanced with the revolution of intelligent, smart systems, especially where Artificial Intelligence (AI) is concerned, not every system has been fully upgraded to utilize these technologies' capabilities. The human element is still overriding much of the decision-making process.
As an example, let’s say we have a reactive lubrication schedule on manual or semi-automatic systems. On systems with lubrication triggers, we have bypasses and resets that chase a short-term “bigger priority,” such as volume output, or to satisfy a lead time condition without interruption to service.
The way around this is to understand the bigger picture, be intentional on the macro level, and take massive action on the micro level to ensure that the macro will not be compromised or sustained by hopping from one short-term priority to the next.
Materials and Knowledge
Materials are easily overlooked, particularly due to an incorrect understanding of their impact. Lubricants are a prime example of this, from the way they are procured, used, substituted, and disposed of.
In tribology, even a single differing property between two lubricant types can make them unsuitable for the same application. But because the impact is not always immediate, they continue to be interchanged, substituted, replaced, and sometimes even mixed. The price to be paid in the long run is much higher than the discipline required to stick to the researched and documented recommendations.
Most organizations at the highest level of the hierarchy would easily sign up their employees for training and development in electronics, IT, and similar “in-your-face” courses, not so much on tribology items or other “background” programs. However, the background deterioration of infrastructure due to tribology problems typically results in CAPEX-type requirements for equipment.
Tribology is mostly cost-optimal when done correctly, but not a low priority, and ignorance of this can lead to much higher costs in the long run and even catastrophic safety incidents.
Lubricants tend to get the most attention regarding disposal at the end of their lifecycle. The bigger change and sustainability effort required here is a mindset shift of the users toward responsible disposal and recycling through upskilling and using the channels already available and provided by product manufacturers and suppliers.
Noria is an example of such an entity offering intentional end-to-end solutions for lubrication materials’ full life cycle.
Processes and Environment
Technological advancements, consumer preferences, and regulatory requirements are leading causes of change in the processes and environments of industrial settings. Governing standards continue to be developed and updated to guide processes and protect the work and external environment from our activities.
While most of these usually focus on a particular output, such as an environmental goal, a quality goal, or a workplace Occupational Health and Safety (OHS) role, the one sure way to make them effective and sustainable is full-circle critical stakeholder consultation.
We often have a standard that addresses one element and creates a gap on the other end, compromising the entire nature of sustainability. For these changes to be meaningfully and intentionally sustainable, equal emphasis on consequence management should also be placed on education and consultation.
People
The good thing about people is our dynamic human nature and the ability to learn, unlearn, and relearn. People change frequently, either of their own accord or for a structured cause. With the right education, stakeholder involvement, realistic expectations, target stretching, and honesty, there is nothing more than being human to inspire, effect, and sustain change.
Scientific tools such as Human Error Root Cause Analysis (HERCA) and The Way To Teach People (TWTTP) are beneficial elements when objectively used in implementing and sustaining change, as that is the softer side that technological advancements may never be able to fill, at least in the foreseeable future.
A focused approach, well-rounded and supported by skills from focus groups and subject matter experts, can fully achieve and sustain the desirable results of maximizing efficiencies, reliability, and optimizing costs.
While usually the hardest, regulation should be easy, as it is based on intention. It is also imperative to know that change is a journey of better discoveries, not a destination of perfection. As such, partners of sound research standing are essential.
Experience is essential to avoid repeating mistakes, and a realistic approach is the foundation of effective planning. Expertise is vital for the right materials, processes, and the deployment of technologies to prevent unsustainable half-baked solutions that get abandoned, creating undesirable waste, costs, and commercial liabilities that no one is willing to pick and service.
A suitable investment in solution development is the only way to optimize costs and keep them within the governance threshold. Cadence is the way to keep the change alive and firmly on a course of sustainability, regular revisits, and reviews of defined milestones while being sensitive and responsive to flexibility triggers.
For lubricants, Noria is a prime example and leading option of intention to inject the step change that sustainably keeps the motion side of industrial things reliably smooth, safe, efficient, cost-effective, and meets the regulations of the different industries around the globe.
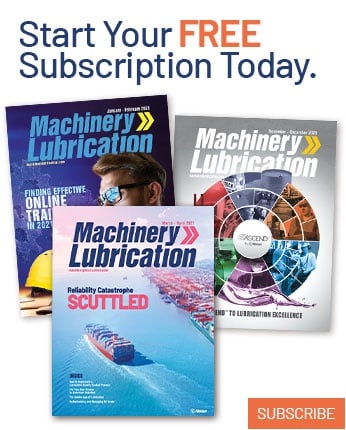