In one of the first comprehensive studies of skill-based pay plans, a management researcher at the University of Arkansas found that such plans are more successful and sustainable in manufacturing facilities than in service organizations. The research also revealed that support among supervisors and employees for the innovative plans consistently predicts their success and survival.
“Our results show that facility characteristics - manufacturing or service, for example - and supervisor and employee support are consistently related to the success of skill-based pay plans,” said Nina Gupta, a management professor in the Sam M. Walton College of Business. “This was especially true with productivity and cost-effectiveness, two important measures of success.”
Compared to conventional job-based compensation, skill-based pay rewards employees for acquiring new skills. In a manufacturing environment, these skills may be as simple as training all employees to operate a forklift or punch press, but usually the skills are tied to specific processes and technology within an individual manufacturing plant. For example, in the pharmaceutical industry, a company may train workers to perform processing tasks such as capsule and tablet production and packaging tasks such as labeling and materials handling, as well as warehousing and quality control tasks.
Conventional systems pay each worker to perform one job all the time. With skill-based pay plans, the goal is to have all workers know all jobs so that they can move from job to job as needed. Employees are given a pay increase for learning and demonstrating proficiency in a new skill, regardless of whether they actually use that skill on the job. Usually connected to an organization’s strategic mission, skill-based pay plans are often part of broad changes that affect many facets of an organization. Hundreds of Fortune 1,000 companies have adopted these plans for at least some of their employees. Many of these companies report improvements in workforce flexibility and productivity, but, until now, these benefits have not been thoroughly tested by independent, empirical research.
Gupta and three colleagues, professors at the universities of Kentucky and Northern Iowa and a management consultant, examined skill-based pay plans as implemented at 97 facilities in the United States. They focused on three critical aspects of skilled-based pay plans - design characteristics, supervisor/employee support and facility characteristics - to determine overall success as measured by workforce productivity and flexibility, cost-effectiveness and survival.
Many companies have adopted skill-based pay plans based on the assumption that they are ideally suited for organizations that emphasize technical innovations. The researchers’ findings, however, did not support this assumption. Companies seeking new and different types of business or those focusing on technical innovations frequently need to modify the definition, training, assessment, maintenance and compensation of skills necessary within their organizations. Because skill-based pay plans require considerable investment in all of the areas, frequent modifications would be too expensive, Gupta said.
Also, skill-based pay structures necessitate precise specification of skills, which is more feasible when production processes vary minimally, are well understood and are easily separated into components. This helps explain the plans’ success in a manufacturing environment.
“Skill-based pay plans promote workforce flexibility, but only in the context of precisely defined skills,” Gupta said. “Productivity and flexibility gains from these plans may be wiped out if production or service-delivery technologies are constantly changing.”
Gupta said that regardless of organization type, managers should not view skill-based pay plans as supremely effective or successful. In isolation, they are no more effective than other types of compensation systems.
“It is not simply whether a particular compensation system is used,” Gupta said, “but rather the specific components and characteristics within that broad approach that predict effectiveness. The particular way the system is implemented and fits within the organizational context is critical.”
The researchers published their findings in the Journal of Management.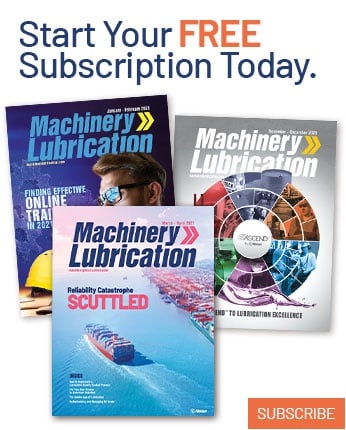