Manufacturing is grappling with a major challenge: a growing skills gap driven by high attrition rates. According to the Deloitte 2025 Manufacturing Industry Outlook, nearly 60% of manufacturers in the National Association of Manufacturers (NAM) outlook survey cited the inability to attract and retain employees as their top challenge. Furthermore, in a 2024 survey of more than 600 manufacturing professionals, over 80% said that labor turnover had disrupted production.
As seasoned workers retire and younger generations pursue diverse career paths, maintenance and reliability teams in these organizations are increasingly strained, struggling to service equipment on time and keep operations running smoothly. To bridge this gap, organizations must consider technology-driven solutions that automate routine tasks and provide critical insights to support leaner teams.
The Technology Gap: Why Manufacturers Are Falling Behind
While many industries are embracing technology to drive efficiency, manufacturing has been slower to adopt advanced tools, particularly when it comes to maintenance teams who operate with legacy systems and manual processes. Resistance to adopting newer tech often stems from budget constraints and a lack of training.
Additionally, many organizations struggle with change management—the structured process of guiding teams through transitions to new technologies, systems, or workflows. A combination of factors, including a lack of clear communication, fear of job displacement, and uncertainty about the return on investment contribute to this struggle. Without strong leadership and a structured approach to change, employees may be hesitant to adopt unfamiliar tools or processes, even when they offer clear benefits.
How Prescriptive Maintenance Helps Teams Work Smarter, Not Harder
For maintenance teams hesitant to adopt new technology, predictive maintenance (PdM) tools such as vibration sensors provide an easy entry point by delivering tangible, actionable results. Rather than relying on abstract predictions, PdM offers real-time insights into equipment health, pinpointing when and where failures are likely to occur. However, PdM on its own only tells teams what might happen—it doesn’t always offer the guidance needed to take action.
That’s where prescriptive maintenance comes into play. By building on predictive insights, AI-powered and expert-led prescriptive maintenance goes beyond PdM to filter out unnecessary alerts, prioritize equipment failure risks, and provide timely, data-driven recommendations on the best course of action to address issues before they escalate. It doesn’t just highlight problems—it offers specific steps to resolve them, helping teams optimize their response times, reduce downtime, and allocate resources more effectively, all without the need for additional manpower. Ultimately, prescriptive maintenance allows teams to work smarter, not harder—making it an essential tool for organizations looking to maximize the potential of their existing workforce.
Implementing prescriptive maintenance requires more than just advanced technology; it demands a culture shift within organizations. Maintenance teams need support, both internally and from a full-service partner, to adopt new processes and fully take advantage of the insights provided by these tools. Organizations that prioritize training, provide access to user-friendly technologies, and foster an environment where data-driven decision-making is encouraged are more likely to succeed in this transition.
Empowering Teams Through Technology: Keys to Success
Successfully leveraging technology to tackle challenges in the workforce requires more than just adopting new tools—it’s about creating an environment where teams can confidently embrace innovation. Here’s how organizations can achieve success:
1. Choose the Right Technology Partner
A partner with Dedicated Condition Monitoring Engineers (CMEs) provides recommended actions based on collected data.
Selecting the right partner is a crucial step in successfully implementing predictive maintenance. Unlike traditional PdM solutions that place the burden of AI implementation on internal teams, AssetWatch provides dedicated experts to handle AI model training and data interpretation. This ensures your team can leverage advanced predictive analytics without needing specialized expertise or diverting valuable resources away from daily operations.
Beyond predictive maintenance, partners like AssetWatch take it a step further with prescriptive maintenance, translating raw data into clear, actionable recommendations. Rather than relying solely on AI to alert teams to potential failures, AssetWatch’s Condition Monitoring Engineers (CMEs) filter out unnecessary alerts and provide specific corrective actions, helping maintenance teams prioritize tasks and address issues before they escalate. By eliminating guesswork, organizations can make informed, data-driven decisions that extend equipment life, prevent costly unplanned downtime, and optimize maintenance schedules.
2. Implement Effective Change Management
Organizations must foster a mindset of innovation by helping teams see the value of predictive analytics as a tool that enhances their work, rather than replacing it. Clear communication is key to overcoming skepticism, ensuring employees understand how these technologies support their efforts by reducing unexpected failures and making maintenance more efficient.
To build confidence and encourage adoption, companies should provide hands-on training that allows employees to become comfortable with new tools in a practical setting. Additionally, showcasing quick wins—such as early detections of potential failures—helps demonstrate tangible benefits, reinforcing trust in the technology and motivating teams to embrace a data-driven approach.
3. Prioritize Continuous Improvement
To fully realize the benefits of predictive maintenance, it’s important to focus on alignment with business goals by tracking KPIs that clearly demonstrate the value of your PdM program and the progress you’re achieving. As operational needs evolve, a full-service partner can help you refine and scale your solution to help you accelerate operational gains. Aligning technology adoption with broader business objectives—such as reducing downtime, extending equipment life, or lowering maintenance costs—helps maximize return on investment and makes sure predictive maintenance remains a valuable asset.
By selecting the right vendor and implementing strong change management strategies, organizations can successfully adopt predictive maintenance and empower their teams to do more with less.
The Path Forward
For manufacturers looking to thrive despite high attrition and limited resources, embracing smarter technology is essential. By moving beyond predictive to prescriptive maintenance and leveraging AI and human expertise, maintenance teams can increase efficiency, reduce downtime, and improve overall productivity.
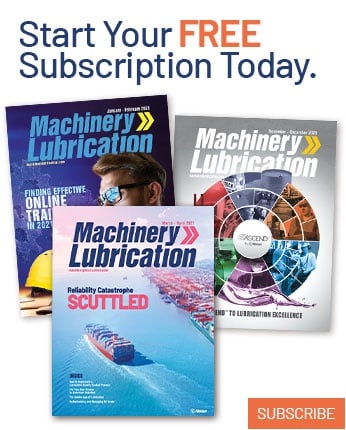