Although Maintenance and Reliability (M&R) and Maintenance, Repair, and Operations (MRO) specialists intuitively understand the value of applying Asset Management best practices to their Manufacturing sites, the majority of Production leadership speak a different language and do not understand the value of implementing targeted M&R and MRO solutions to aid in resolving what is typically viewed as operational challenges.
This article combines the experience and expertise of two seasoned professionals, one from manufacturing and one from maintenance, as they identify and address ten common production/operational challenges with specific M&R/MRO best practices.
This real-world approach in "Connecting the Dots" breaks down the language barrier between Manufacturing Leadership and Maintenance and Materials Management Specialists, providing value-added insights that can be directly applied to operations.
Top 10 Manufacturing Challenges
There are many proven M&R and MRO best practices that have been proven time and again to effectively mitigate a variety of issues, including the top ten challenges often faced in manufacturing, including:
- Extended Plant Downtime
- Recurring Equipment Repairs
- Poor Maintenance Craft Utilization
- Under & Over Stocked Parts Inventory
- High Operational Costs
- Soaring Operational Inefficiencies
- Poor Communications Between Production & Maintenance
- Lack of Equipment Knowledge & Ownership by Operators
- Previous Failed Attempts at Implementing Operational Excellence
- Reduced Operational Profitability
By understanding the challenge, the applicable improvements and solutions can be identified, allowing facilities a holistic way of addressing and mitigating these issues.
Challenge #1: Extended Plant Downtime
Problem: Waiting for Spare Parts
Solutions | Results |
---|---|
Ensure a Work Management code of “Waiting for Parts” is adopted. | By attributing this Work Status code, insights can be identified, and mitigating action can be taken before the situation becomes an emergency. |
Adopting a Point-of-Use (POU) storage philosophy where practical. | The Mean Time to Repair (MTTR) and overall downtime are decreased by storing certain critical spare parts near where they are used. |
Ensure all storeroom parts being withdrawn are "Checked Out." | Accurate on-hand quantities are reflected in the system, and reordering will occur to avoid future stock-out issues. |
Implement storeroom access and security measures. | These measures will help decrease stock-outs and ensure parts are checked out, reordered, and available in the future. |
Implement an Inventory Data Integrity Review (IDIR). | By adopting an IDIR, missing information in the inventory module, such as Vendor or Lead Time, can be proactively identified and mitigated, reducing future equipment downtime and MTTR. |
Perform physical spot checks. | By performing physical spot checks, erroneous on-hand counts will be proactively identified. This will allow stock to be reordered and replenished, decreasing the likelihood of extended equipment downtime. |
Conduct periodic cycle counting. | By cycle counting MRO inventory, out-of-stock events are prematurely identified, and the likelihood of increased equipment downtime is reduced. |
Implementing a Bill of Materials (BOM) effort. | Proactively capturing inventory items that should be stocked vs. waiting until a machine breaks down to reactively see if they have ever been identified, ordered, and placed in inventory will reduce inefficient searching for unstocked parts and additional idle machine time. |
Problem: Inefficient Timing of Maintenance Activities
Solutions | Results |
---|---|
Adopting Maintenance Planning & Scheduling. | Equipment downtime and craft efficiency will be reduced as your site matures in its adoption of Maintenance Planning and Scheduling. Ensuring the optimal production window is selected and having the right crafts, permits, spare parts, and special tools identified and pulled minimizes the overall time required. |
Incorporating Predictive Maintenance (PdM) technologies. | By adding PdM and condition monitoring to your maintenance strategy, the site will have a more accurate understanding of actual equipment health, thereby having the opportunity to take corrective action before the equipment condition becomes an emergency. |
Problem: Recurring Equipment Failure
Solutions | Results |
---|---|
Adopting a Comprehensive Maintenance Training Program. | It is essential to ensure that the maintenance technicians are properly trained so that they can perform maintenance activities in a "do it right the first time" way. Sharpening diagnostic and troubleshooting skills prevents the staff from becoming "parts changers" until they get it right. |
Challenge #2: Recurring Equipment Repairs
Problem: Poor Maintenance Troubleshooting and Repair Skills
Solutions | Results |
---|---|
Implement an effective maintenance training program. | Equipment will fail less when maintenance technicians are trained in their respective fields with basic, intermediate, and advanced technical courses and diagnostic and troubleshooting. When it does need to be repaired, the likelihood of repairing it properly exponentially increases. |
Problem: Performing Proper Maintenance Diagnostic and Repairs Is Not Emphasized
Solutions | Results |
---|---|
Implement a precision maintenance program with the “do it right the first time” approach. | A precision maintenance program continuously emphasizes performing the right work in the right way at the right time. This maintenance strategy adopts the tools, training, and philosophy required for achieving less waste, scrap, and overall rework. |
Problem: Rework Is Not Tracked
Solutions | Results |
---|---|
Implement active metrics and associated targets measuring recurring asset downtime. | By adopting asset management and reliability metrics, rework will be one of many key indicators of the efficiency and effectiveness of the equipment care activities occurring at the site, allowing for any required course correction to occur. |
Challenge #3: Poor Maintenance Craft Utilization
Problem: Excessive Time Spent Searching for Spare Parts
Solutions | Results |
---|---|
Implementing a logical Design, Organization, and Layout plan in the maintenance storeroom. | By implementing this plan in the maintenance storeroom, team members can locate parts more quickly. |
Performing a lighting project and conducting regular cleaning/housekeeping tasks. | Team members can locate parts more quickly and efficiently. |
Labeling each shelf or drawer, as well as the specific bins. | Parts identification occurs more quickly and accurately. |
Adopting a storeroom map and incorporating signage identifying where various MRO parts are stored. | Maintenance technicians can locate their required parts much faster. |
Utilizing a standardized naming taxonomy in the material item master. | Those looking up parts in the system or printed-out stock catalogs can locate needed spares quickly. |
Adopting Kitting and Staging. | Depending on the number of jobs a given craftsperson completes each day, their time spent inefficiently in the storeroom looking for parts at the beginning of each job improves craft utilization by 10-25%. |
Utilizing a parts reservation plan as part of planning and scheduling. | Reduction in the percentage of craftspeople turning up to perform a job only to discover the parts are not in stock is reduced by 10-15%. |
Problem: Inefficient Time Spent Performing Non-Value Adding Preventive Maintenance
Solutions | Results |
---|---|
Conduct a PM/PdM review and optimization. | By periodically reviewing your site's PMs activities, you can save untold hours and, therefore, money spent on ineffective PM activities. |
Challenge#4: Under- and Over-Stocked Inventory
Problem: Under-Stocked Inventory
Solutions | Results |
---|---|
Implementing a regular cycle count program. | By cycle counting MRO inventory, out-of-stock events are prematurely identified, and the ability to replenish inventory proactively is greatly enhanced. |
Implement storeroom access and security measures. | Addressing storeroom security will reduce shrinkage and stock-outs, resulting in rush freight charges and potentially increased unscheduled equipment downtime. |
Implement storeroom inventory withdrawal process. | By adopting a formalized storeroom inventory withdrawal process, fewer stock-outs will occur. |
Utilize automated reorder reports. | Utilizing the inventory module's automated reorder report function will allow parts to be ordered, consequently received, and replenished more promptly, reducing expensive stock-outs. |
Problem: Over-Stocked Inventory
Solutions | Results |
---|---|
Performing an obsolescence study. | An obsolescence study can reveal that up to 30% of a site’s current inventory is unnecessary, which, after being properly disposed of, requires less time to clean, manage, cycle count, etc. By identifying unnecessary inventory, items may be disposed of properly, resulting in less property tax exposure at the end of the fiscal year. |
Adopting proper obsolescence disposition alternatives. | Utilizing one of the optimal ten disposition options available, the site will reduce inventory in a fiscally responsible method. |
Inventory standardization and cross-referencing. | By performing inventory standardization and cross-referencing, "like" items can be consolidated, reducing the amount of inventory dollars tied up, the space required to store them, and the confusion on behalf of the parts consumers. The benefit of reducing on-hand inventory dollars alone is estimated to be between 3-5% of inventory value. |
Utilizing a standardized naming taxonomy in the material item master. | By implementing this best practice, duplicate inventory items will be identified and weeded out of the inventory over time. |
Challenge #5: High Operational Costs
Problem: Excessive Rush Freight Expenses
Solutions | Results |
---|---|
Implementing a regular cycle counting program. | By cycle counting MRO inventory, out-of-stock events are prematurely identified, and expensive premium freight is decreased by an average of 20-25%. |
Adopting a period minimum/maximum evaluation. | By periodically reviewing inventory minimum/maximum levels using Economic Order Quality (EOQ) and other automated software, the occurrence of expensive premium freight can be significantly reduced. |
Implement an Inventory Data Integrity Review (IDIR). | By adopting an IDIR, missing information in the inventory module, such as long lead times, can be proactively identified, minimum/maximum levels updated, and premium freight costs avoided. |
Problem: Excessive Maintenance Overtime
Solutions | Results |
---|---|
Adopting a proactive maintenance model, including the use of maintenance planning and scheduling. | Using a mechanism to get work completed correctly in a proactive manner and coupling this with precision maintenance will lead to longer equipment life and a less reactive culture, minimizing overall downtime and overtime. |
Challenge #6: Soaring Operational Inefficiencies
Problem: Warehouse and Storeroom Space Limitations
Solutions | Results |
---|---|
Utilizing high-density cabinetry storage solutions. | By adopting high-density cabinetry, space-saving carousels, and state-of-the-art warehouse racking, the required footprint shrinks, making raw materials and MRO inventory spare parts more manageable and parts more quickly and easily found. |
Adopting automation tools. | Cycle counting can be performed quickly and accurately by incorporating productivity enhancements, such as bar coding and scanning, and inventory receiving, withdrawing, and returning. |
Utilizing vendor-managed inventory (VMI). | By utilizing VMI, on-site storeroom personnel will spend less time cycle counting, freeing them up to perform other value-added activities. |
Adopting the use of free issue areas. | By identifying select items that should not require storeroom personnel to be tied up (e.g., handing out personal protective equipment or safety items every day), they can be freed up to perform other MRO duties. |
Challenge #7: Minimal Teamwork Between Production and Maintenance
Problem: A Siloed Culture with Poor Communication
Solutions | Results |
---|---|
Regular quality communication with production socializing equipment care is needed. | Production personnel have access to create a maintenance work request and have been trained on how to complete this process properly so that notifications of needed equipment care can be communicated, planned, scheduled, and executed. |
Maintenance collaborating with production on equipment work needing to be performed. | As the maintenance planners and schedulers meet with production to negotiate time for maintainers to access equipment care and life extension to critical assets, communication is enhanced, and schedules can be developed and adhered to. |
Maintenance communicating to production once the work is completed. | By maintenance team members notifying production they have completed their maintenance activities, production can immediately begin their start-up routines to get the process back up and running, minimizing equipment downtime and increasing throughput. |
Production personnel providing much-needed input on equipment repair activities. | By the production staff sharing input regarding equipment behavior upon unplanned machine failure, the MTTR will be greatly reduced. By participating in Root Cause Failure Analysis (RCFA) events, future asset downtime may likely be minimized if not avoided. |
Challenge #8: Lack of Equipment Knowledge and Ownership From Operators
Problem: The Misperception That Asset Care Is Not Their Job
Solutions | Results |
---|---|
Culture change and transformation. | By addressing the culture with events, such as best practices awareness training, production personnel will learn the role that their counterparts in highly function companies have adopted and that, like safety, equipment uptime is everyone's responsibility, thus instilling a sense of site collaboration. |
Total Productive Maintenance (TPM) | Adopting TPM or operator care entails the production staff getting an education on critical processes and assets and being tooled up and trained in performing equipment care inspections and light maintenance activities, freeing up maintenance to perform essential tasks and enabling operators to better operate and preserve their machinery. |
Root Cause Failure Analysis | By implementing a thorough, team-based approach to mitigating future equipment failures, organizations adopting RCFA will gain insights from a host of different perspectives. The input from the cross-functional team will ensure asset life extension and a greater understanding of how to better install, operate, and maintain essential equipment. |
Challenge #9: Previous Failure in Implementing Operational Excellence
Problem: Absence of a Strategic, Long-Term Plan
Solutions | Results |
---|---|
Best practices gap assessment and reliability roadmap. | By thoroughly reviewing the site's current engineering and maintenance reliability programs compared with industry best practices, the identified gaps can be prioritized, and a strategic improvement plan will be developed and pursued, serving as a roadmap to operational excellence. |
Socialization and education of what good looks like. | To aid in pursuing an effective improvement process, site leadership must share with the masses what operational excellence looks like. This includes collaboratively developing and communicating the organizational mission, vision, and values, as well as what maintenance and reliability excellence practices are being committed to and what everyone's roles are in pursuing them. |
Measurement and accountability. | One critical success factor in achieving an effective operation and operational improvement plan is sharing expectations, including desired results and timelines, communicating progress, discussing and mitigating roadblocks, measuring performance, and holding the stakeholders and champions accountable while giving credit where credit is due and celebrating successes that are realized. |
Challenge #10: Reduced Operational Profitability
Problem: Reduced Production Throughput
Solutions | Results |
---|---|
A host of targeted and well-implemented asset management best practice initiatives. | Whether the site is struggling to meet customer demands, production schedules, OEE targets, or reduce overall costs, there is an M&R best practices element that will aid in achieving these goals. By performing a comprehensive asset management assessment, speaking with all organization representatives, and mining the maintenance system database for recurring work and elevations in parts used, a more precise understanding can be had of the right M&R activities to pursue. By mapping out the improvement initiatives to undertake and committing to performing thorough project management, including good communication and measuring performance improvements, the site can be assured that production will enjoy many benefits from adopting these M&R activities. |
Summary
Those of us tasked with effectively, profitably, and safely managing industrial or manufacturing organizations recognize that the disruptions to those efforts come in numerous forms. Although this article has not attempted to list them all, hopefully, some of the common ones you face have been addressed and, as a result, have introduced potential solutions you may not have employed before.
As a growing community of practitioners, the industry will only benefit from being transparent in sharing "nuggets" of wisdom that may help provide creative solutions in a variety of areas, including Maintenance and MRO Materials Management. In doing so, facilities adopting these solutions can effectively decrease costs and reduce the amount of unmet deadlines while increasing communication, collaboration, productivity, and profitability. At the very least, these ideas, if put to use, will avoid a headache.
We wish you every success in identifying and applying asset management best practices to your manufacturing challenges!
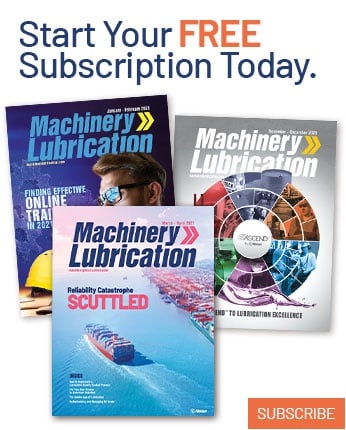