Understanding the Dilemma
Tools for Workforce Development
- Comprehensive Training: One of the most effective methods for developing and advancing a deep knowledge of both technical and soft skills crucial for team success. Technical training can include aspects such as maintenance and reliability best practices, proper machinery lubrication, data analytics, and specialized courses on specific technologies. Soft skills training includes leadership and communication, problem-solving, and collaboration, all of which help team members work together and navigate an ever-evolving workspace.
- Specialized Upskilling: Specially designed programs that enhance team member abilities to help them integrate new technologies into their work routines and create increased performance standards. These opportunities often revolve around technologies, such as AI, IIoT, robotics, and data analytics and come in several forms, including workshops, seminars, and online courses.
- Institutional Collaboration: As a forward-thinking initiative, many vocational schools, community colleges, and universities are partnering with facilities across all industries to ensure that their curriculum aligns with growing industry demands. This helps ensure students entering the industry workforce will have the appropriate skills and mentorship opportunities to more quickly and easily integrate into facility life.
- Leveraging Technology: While technology is causing confusion in some respects, it is widely recognized that the younger workforce is technologically savvy in many areas. Because of this, advanced technologies have increasing potential to positively impact the way skills are being learned in the facility. Technologies like virtual reality (VR) and augmented reality (AR) have tangible benefits, teaching real-world scenarios in a simulated environment. This allows team members to practice varying skills in a safe setting without real-world consequences for human errors.
- Developing a Culture of Continuous Improvement: One of the largest factors of team member success and perseverance is company culture. By developing a culture of continuous improvement, leaders champion the importance of continuing personal advancement by creating an environment where employees feel empowered to ask questions, learn new skills, and invest in their professional development. By promoting and rewarding this type of cultural initiative, facilities help team members become more adaptive, resilient, and collaborative.
Conclusion
Supplier Spotlight
AssetWatch 60 Collegeview Rd., Westerville, OH 43081 844-464-5652 | www.assetwatch.com
Predictive maintenance has never been easier or more cost-effective, thanks to end-to-end condition monitoring from AssetWatch. With remote wireless sensors, advanced AI, and CAT III+ experts—all for a low monthly subscription—your team will have the power to conquer unplanned downtime for good. Try us risk free for 30 days, and start seeing value on day one.
RelaWorks 1328 E. 43rd Court, Tulsa, OK 74145 918-392-5058 | RelaWorks.com
Finding the right products can be difficult. Every industry and application is unique. Over-spending and guess work is common. At RelaWorks, we help reliability professionals solve this challenge. Our mission is to provide products for your unique needs and budget. Backed by Noria Corporation’s expertise and legendary customer service, we’re excited to help your reliability program succeed.
LubePM 1328 E. 43rd Court, Tulsa, OK 74105 800-597-5460 | LubePM.com
As a Lubrication Management System (LMS) engineered by lubrication professionals, LubePM helps an organization create accountability to ensure that every lubrication point is carefully maintained, inspected and measured. Ready to take your facility’s Lubrication Management System to the next level with LubePM? We’re ready to help. Simply request more information or schedule a demo.
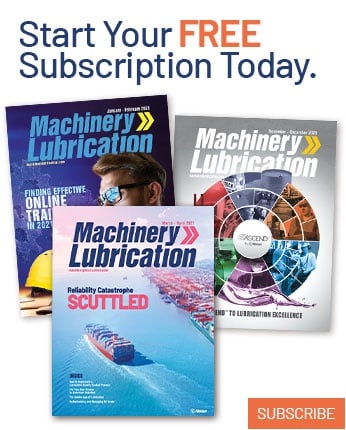