What is Condition Monitoring?
IoT in Condition Monitoring: A Perfect Match
Benefits of IoT-Driven Condition Monitoring
- Increased Equipment Uptime: One of the most significant advantages of IoT-enabled condition monitoring is extending equipment uptime. Real-time monitoring allows teams to predict failures and carry out maintenance during scheduled downtimes, minimizing unplanned outages that can cripple operations.
- Cost Savings: Proactive maintenance strategies help organizations save significant costs. IoT-driven condition monitoring eliminates the need for unnecessary routine inspections, reduces the occurrence of emergency repairs, and ensures that parts are only replaced when necessary. This helps companies avoid over-maintenance and the high costs associated with unscheduled downtime.
- Improved Safety: Machinery malfunctions can lead to dangerous situations for workers, especially in manufacturing, oil and gas, and mining. IoT sensors provide early warnings of potential safety hazards, allowing operators to take corrective action before a problem escalates. This proactive approach leads to a safer work environment and reduces the likelihood of accidents caused by equipment failure.
- Data-Driven Decision-Making: IoT sensors continuously collect data that can be used to identify trends and improve decision-making. By analyzing this data, companies can optimize their maintenance strategies, enhance asset performance, and make informed decisions regarding equipment upgrades or replacements. IoT-driven analytics give businesses a deeper understanding of their operations, which helps them stay competitive in a constantly evolving industrial landscape.
- Sustainability and Energy Efficiency: Condition monitoring through IoT saves money and promotes sustainability. By maintaining machinery at optimal performance, companies can reduce energy consumption and prolong the lifespan of their equipment. Furthermore, fewer emergency repairs mean less waste in terms of broken parts and resources used in replacements.
Real-World Applications of IoT in Condition Monitoring
- Manufacturing Plants: In large-scale manufacturing facilities, where equipment operates around the clock, unplanned downtime can lead to significant revenue losses. IoT sensors monitor real-time machinery conditions such as temperature, vibration, and pressure, alerting maintenance teams when something deviates from the norm. This proactive maintenance strategy has successfully prevented breakdowns and kept production lines running smoothly.
- Oil & Gas Industry: For offshore platforms and refineries, equipment reliability is paramount. IoT-powered condition monitoring enables companies to remotely monitor critical assets, such as pumps and compressors, in hazardous or hard-to-reach locations. With real-time data available through cloud-based platforms, maintenance teams can address issues quickly and efficiently, avoiding catastrophic failures.
- Wind Turbines: Wind turbines are exposed to harsh environmental conditions, and their components endure constant stress from high winds and variable weather. IoT sensors monitor vibrations, rotational speed, and other key indicators to detect any turbine performance abnormalities. This allows wind farm operators to schedule maintenance when necessary, minimizing downtime and optimizing energy output.
Overcoming Challenges
The Future of Condition Monitoring with IoT
Supplier Spotlight
Noria Academy 1328 E. 43rd Court, Tulsa, OK 74105 800-597-5460 | Noria.com/Academy
Obtaining certification can be a challenge; new terms, concepts and topics can overwhelm even the most experienced reliability professionals. Training experts all agree that extending the learning beyond the classroom dramatically increases knowledge retention. To aid in this retention and create an innovative student experience, Noria is pleased to offer the Noria Academy app.
RelaWorks 1328 E. 43rd Court, Tulsa, OK 74145 918-392-5058 | RelaWorks.com
Finding the right products can be difficult. Every industry and application is unique. Over-spending and guess work is common. At RelaWorks, we help reliability professionals solve this challenge. Our mission is to provide products for your unique needs and budget. Backed by Noria Corporation’s expertise and legendary customer service, we’re excited to help your reliability program succeed.
LubePM 1328 E. 43rd Court, Tulsa, OK 74105 800-597-5460 | LubePM.com
As a Lubrication Management System (LMS) engineered by lubrication professionals, LubePM helps an organization create accountability to ensure that every lubrication point is carefully maintained, inspected and measured. Ready to take your facility’s Lubrication Management System to the next level with LubePM? We’re ready to help. Simply request more information or schedule a demo.
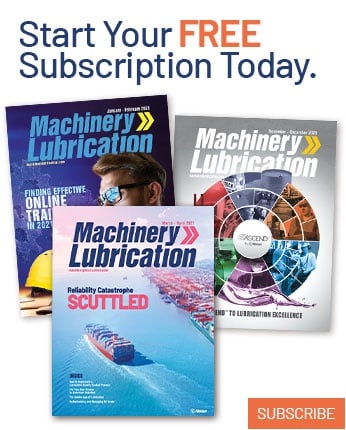