Photo courtesy of Adobe, on behalf of AMSS Consulting
Optimization of preventive maintenance (PM) practices is paramount for ensuring operational efficiency and minimizing downtime. This comprehensive case study delves into the journey of a prominent stationary equipment manufacturing company based in Central Illinois as it confronted challenges within its maintenance operations and successfully streamlined its PM programs with the strategic assistance of Advanced Management Systems & Services (AMSS) Consulting.
Preventive maintenance (PM) optimization refers to the process of improving and refining PM programs to maximize their effectiveness and efficiency. It involves analyzing existing maintenance practices, identifying areas for improvement and implementing strategies to enhance equipment reliability, minimize downtime, and optimize resource allocation.
PM optimization ensures that preventive maintenance activities are performed at the right time based on equipment condition, operational requirements, and industry best practices. It aims to balance excessive maintenance, which can be costly and unnecessary, and insufficient maintenance, which can result in increased equipment failures and downtime.
PM optimization is typically facilitated by computerized maintenance management systems (CMMS) or other maintenance software solutions. These systems help track maintenance activities, store equipment data, generate reports, and provide real-time visibility into maintenance operations, enabling informed decision-making and continuous improvement.
By optimizing preventive-maintenance practices, organizations can improve equipment reliability, reduce maintenance costs, minimize unplanned downtime, and enhance overall operational efficiency. It enables a proactive approach to maintenance, allowing organizations to identify and address potential issues before they result in significant equipment failures or disruptions to production.
Company Overview
The Business Situation
The client is a leading industrial company specializing in stationary equipment manufacturing that serves multiple global industries from agriculture to food & beverage and oil & gas. They quickly recognized that focusing on optimization of preventive maintenance (PM) would improve equipment reliability, minimize downtime, and maximize productivity. To enhance maintenance practices, the client embarked on a journey to optimize their PM programs with the assistance of AMSS Consulting.
The client faced the following challenges, including but not limited to:
Inefficient PM Practices: Existing PM programs lacked standardization, resulting in inconsistent maintenance tasks, frequencies, and documentation across equipment and departments inefficient scheduling and execution of preventive maintenance tasks.
Reactive Maintenance Mindset: The client primarily relied on reactive maintenance, addressing issues as they occurred, which led to increased downtime and higher maintenance costs.
Lack of Data-Driven Decision-Making: The absence of data analysis and performance monitoring hindered the identification and implementation of PM optimization opportunities.
Resource Allocation: Limited resources and manpower allocation resulted in inefficient PM execution and suboptimal utilization of available resources.
Measuring: Difficulty tracking maintenance costs and evaluating asset performance.
Goals
The company's primary objectives were to:
Optimize the PM process to enhance equipment reliability and reduce downtime, improve maintenance scheduling and resource allocation, and work- order management, along with increasing visibility into maintenance activities, asset history, and performance metrics to enhance cost control and better decision-making by analyzing maintenance data.
The Solution
Implementation Steps:
Needs Assessment: Existing PM practices, equipment reliability data, and organizational goals were thoroughly assessed. They identified the need to optimize their PM programs to enhance equipment performance and reduce maintenance costs.
Software Selection: After evaluating various CMMS software options presented by AMSS, the client selected a robust and scalable system aligned with their requirements. The chosen CMMS offered features such as work order management, preventive maintenance (PM) scheduling, inventory tracking, and reporting capabilities.
Data Collection and Analysis: Historical equipment-reliability data, maintenance records, and performance metrics were collected and analyzed to identify patterns, recurring issues, and opportunities for PM optimization.
PM Task Standardization: Standardized PM task lists for each equipment type and criticality level were developed. These task lists included appropriate maintenance activities, frequencies, and detailed procedures, ensuring consistency and accuracy in maintenance execution.
Risk-Based Prioritization: The client implemented a risk-based approach to prioritize equipment for PM optimization. Equipment criticality, historical failure rates, and production impact were considered to allocate resources effectively and focus efforts on high-priority equipment.
PM Interval Optimization: Utilizing data analysis and equipment-reliability information, the client optimized PM intervals to ensure tasks were performed at the most appropriate frequencies. The PM optimization helped reduce unnecessary maintenance activities and associated costs while maximizing equipment uptime.
Performance Monitoring and KPIs: Key Performance Indicators (KPIs) were established to monitor the effectiveness of PM optimization efforts. KPIs such as equipment uptime, maintenance costs, PM compliance rates, and mean time between failures (MTBF) were tracked and analyzed regularly.
Training and Skill Development: The client invested in training programs to enhance the technical skills of maintenance personnel. Training included equipment-specific PM procedures, data-analysis techniques, and the utilization of CMMS tools for efficient PM execution.
Continuous Improvement: The client fostered a culture of continuous improvement by encouraging feedback from maintenance teams and leveraging their expertise. Regular review meetings, feedback sessions, and brainstorming workshops were conducted to identify further optimization opportunities.
The Business Impact
The client closely monitored the performance of optimized PM programs. Performance data, KPIs, and feedback from maintenance personnel were collected and analyzed regularly to assess the effectiveness of the optimization efforts. This monitoring helped identify areas for further improvement and facilitated data-driven decision-making.
Benefits and Outcomes:
Increased Equipment Reliability: The optimization of PM programs resulted in improved equipment reliability. Proactive maintenance minimized unexpected failures and downtime based on standardized procedures and optimal intervals, enhancing overall productivity.
Reduced Maintenance Costs: By optimizing PM activities, the client eliminated unnecessary maintenance tasks and focused resources on critical equipment. PM optimization led to reduced maintenance costs, decreased reliance on reactive maintenance, and better allocation of resources.
Enhanced Data Utilization: Data analysis techniques allowed identification of equipment performance trends, recurring issues, and areas for improvement. Data-driven decision-making empowered the company to implement targeted PM optimization strategies.
Improved Planning and Resource Allocation: The optimization efforts enabled planning and allocation of maintenance resources more efficiently. By prioritizing high-risk equipment and optimizing PM intervals, the client ensured that resources were allocated where they were most needed, increasing operational efficiency.
Cultural Shift towards Proactive Maintenance: The PM optimization initiative resulted in a cultural shift within the organization, encouraging a proactive maintenance mindset. Maintenance teams became more engaged in preventive activities, emphasizing early detection and proactive maintenance execution.
What's Next
Through a systematic approach to PM optimization, the client successfully transformed maintenance practices from reactive to proactive. Standardizing PM tasks, implementing risk-based prioritization, and leveraging data analysis techniques allowed them to achieve increased equipment reliability, reduced maintenance costs, and enhanced resource allocation. Optimization improved operational efficiency and fostered a culture of continuous improvement and data-driven decision-making throughout the organization.
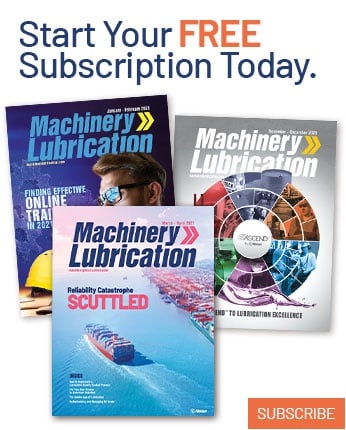