The following article features excerpts from Industrial Machinery Repair, by Ricky Smith, CMRP, CMRT, and Keith Mobley.
Several surveys conducted in industries throughout the United States have found that 70% of equipment failures are self-induced. Maintenance personnel who either choose to or do not know how to follow what are understood industry-wide as 'Best Maintenance Repair Practices’ substantially affect these failures.
To elaborate, between 30% and 50% of the self-induced failures are the result of maintenance personnel not knowing the basics of maintenance. Maintenance personnel who, although skilled, choose not to follow the best maintenance repair practices, potentially cause another 20% to 30% of those failures.
The existence of this problem has been further validated through the skills-assessment process performed in companies throughout the state of Georgia, in this example. This program evaluated the knowledge of basic maintenance fundamentals through a combination of written, identification, and performance assessments of thousands of maintenance personnel from a wide variety of industries.
The results indicated that more than 90% of personnel lacked the basic fundamentals of mechanical maintenance. This article focuses on the widely accepted Best Maintenance Repair Practices necessary for maintenance personnel to keep equipment operating at peak reliability, and companies functioning more profitably through reduced maintenance costs and increased productivity and capacity.
The potential cost savings from adopting and following best practices can often be beyond the understanding or comprehension of management. Many managers are in a denial state regarding maintenance. The result is that they do not believe that repair practices directly impact an organization’s bottom line or profitability.
More enlightened companies have demonstrated that, by reducing the self-induced failures, they can increase production capacity by as much as 20%. Other managers accept lower reliability standards from maintenance efforts because they either do not understand the problem or they choose to ignore this issue. A good manager must be willing to admit to a maintenance problem and actively pursue a solution.
You may be asking what the Best Maintenance Repair Practices are. Here are a few important ones that maintenance personnel must become familiar with:
Best Maintenance Repair Practices | ||||
---|---|---|---|---|
Maintenance Task | Standard | Required Best Practices | Consequences for Not Following Best Practices | Probability of Future Failures: Number of Self-Induced Failures vs. Following Best Practices |
Lubricate Bearing | Lubrication interval – time-based ± 10% variance |
|
|
100% → 20 vs. 1 |
Coupling Alignment | Align motor couplings utilizing dial indicator or laser-alignment procedures - laser is preferred for speed and accuracy; straight-edge method is unacceptable. |
|
|
100% → 7 vs. 1 |
V-Belts | Measure the tension of v-belts through tension and deflection utilizing a belt tension gage. |
|
|
100% → 20 vs. 1 |
Hydraulic Components | Hydraulic fluid must be conditioned to component specifications |
|
|
100% → 30 vs. 1 |
Looking through this abbreviated Best Maintenance Repair Practices table, try to determine whether your company follows these guidelines. The results will likely surprise you. You may find that the best practices have not been followed in your organization for a long time.
Adopting Best Maintenance Repair Practices at Your Plant
In order to fix the problem, you must understand that the culture of the organization is at the bottom of the situation. Everyone may claim to be a maintenance expert, but the conditions within a plant generally cannot validate that this is true.
When considering changing basic beliefs, procedures, or revamp an established strategy, the reasons why an organization does not follow these best practices in the repair of their equipment must be identified. A few of the most common reasons may include:
- Maintenance is totally reactive and does not follow the definition of maintenance, which is to protect, preserve, and prevent from decline (reactive plant culture).
- Maintenance personnel do not have the requisite skills.
- The maintenance workforce lacks either the discipline or direction to follow best maintenance repair practices.
- Management is either not supportive and/or does not understand the consequences of not following the best practices. (Real understanding must involve a knowledge of how much money is lost to the bottom line).
In order to solve the problem of not following Best Maintenance Repair Practices a sequential course of action should be taken.
1st: Identify Whether a Problem Exists: i.e., tracking repetitive equipment failures, reviewing capacity losses in production, and identifying causes for these losses, measuring the financial losses due to repair issues.
For more detail on how better to identify the problem at hand, please refer to the Nyman Maintenance Cost Iceberg© below:

2nd: Identify the Source of the Problem: this could stem from a combination of issues:
- Maintenance Skill Level – Perform Skills Assessment (written and performance-based) to evaluate whether skill levels are adequate to meet Best Maintenance Repair Practices for your specific maintenance organization.
- Maintenance Culture – Provide training to all maintenance and management relative to a change in maintenance strategy and how it will impact them individually (i.e., increase in profit for the plant, less overtime resulting from fewer equipment breakdowns, etc.). Track and measure the changes and display the results to everyone.
- Maintenance Strategy – Develop a plan to introduce a proactive maintenance model with preventive and planned maintenance at the top of planned priorities. This will provide more time for performing maintenance utilizing the Best Maintenance Repair Practices.
3rd: Implement the Changes Needed To Adopt Best Maintenance Repair Practices at Your Plant and Measure the Financial Gains.
Everyone should be aware that financial rewards can be great, but we must also understand why they can also be hard to achieve. Several reasons why implementing a program of change, such as the ones discussed here, can be doomed to failure could include:
- Management is not committed.
- Lack of discipline and direction
- Lack of management commitment and accountability
- Momentum becomes slowed or changes direction.
- Lack of an adequately skilled workforce
- No gap analysis or specific action plan to guide the effort to close the gaps
-
Conflict between emergencies and performing maintenance following Best Maintenance Repair Practices; this does not mean all “emergent” repairs must be performed to ‘as built’ specifications the first time, but it does mean that the repair, especially temporary fixes, will be corrected during the next outage of the equipment.
Reaping the Rewards of Best-Practices Reliability
To conclude, as many as 90% of companies in the United States do not follow Best Maintenance Repair Practices. The 10% that do follow these practices realize the rewards of a well-run, capacity-driven organization that can successfully compete in today’s and tomorrow’s marketplace.
Remember, the use of the Best Maintenance Repair Practices might just become a mandatory requirement for the future success of an organization in today’s economy. By becoming familiar with the tips and outline in this article, you'll be that much more prepared to implement these best practices at your plant.
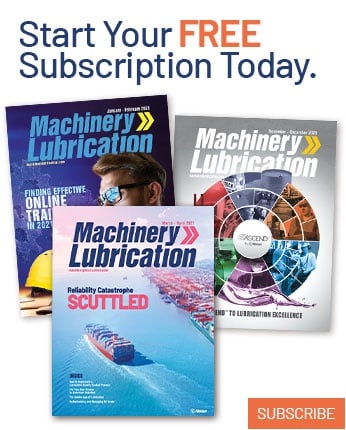