In 2019, the Plant Engineering Department of McKee Foods Corporation in Collegedale, Tenn., started an initiative to improve equipment reliability which we dubbed McKee Maintenance Excellence (MME). MME included many of the typical elements of a maintenance improvement program such as: work execution, preventive maintenance optimization (PMO), root cause analysis (RCA), and precision and predictive maintenance. As we began, we put together a plan on what we needed to do to get our foundation right.
This effort began by documenting how work was currently accomplished and comparing that to what world-class looked like. Focus teams consisting of people from departments across the company were put together to start building these processes. Assessing our progress a couple of years into the implementation, we felt we weren't where we should have been.
So, in this article we are going to look at why this process stalled, and why you might be the problem.
Problem Statement
Have you ever heard of the “Flavor of the Month”? Most improvement initiatives began with great expectations and a lot of energy. Usually they are driven by some KPI that is not trending or tracking the way it should. Sadly, most of those initiatives end in the “Flavor of the Month” club.
We were bound and determined not to let our reliability journey follow the same path that most other programs had. So, we asked ourselves, "Why do most initiatives fail"? The answer was simpler than you might think.
Could it really be because of me? Our inability to set clear expectations could, in fact, be the very reason our initiative is failing.
Desired Vision
If you are going to set clear expectations you need to know what the end vision is. It is hard to set clear expectations if you do not know where you are headed. The easiest way to start with the end is knowing the desired results, and that is usually something that can be easily measured. I also like to think about it as the “What You Want" phase.
The example we will follow through in this article has to do with our technician’s not using closeout notes on their work orders. We first started the implementation by training all our people on how to use the processes created and our software called iWork. We showed the technician’s what we wanted done and how to do it.
So, why wasn’t everyone following the training later on? It turns out we never really set clear expectations because we didn’t start with the end in mind. We never clearly defined the vision.
How did we correct it? Well, we found that it is never too late to set expectations. We brought everyone back together once we saw what was going on and adopted different training methods and explained things a different, more detailed way.
When retraining, we used the software as we did before but added more hands-on training, ensuring that everyone physically completed each process.
We also laid out the end results in a simple, consise way and defined what success would look like. More specifically, the metric we established was that all work orders must also have a closeout note. Before we set this expectation, we were only getting around 37% of our work orders with close out notes. After tweaking our plan, we are closer to 85% on closeout notes, as seen from the graphs below:
Team Behaviors
The next step in the process of setting clear expectations concerns the technician’s behavior. This step is where you actually tell the technicians how they should behave in the future. This is the “How I Want It Done" phase.
For our example, this was focused on demonstrating how to enter closeout notes. We had the techs complete closeout notes, helping out anyone that struggled with the process, as part of our hands-on initiative that was part of our newly defined retraining process.
When you describe the exact method and metrics you expect them to use, there is no doubt about what your expectations are. It also gives you chance to correct any misinformation that may be floating out there and the opportunity to answer questions about specific situations that may arise in a facility.
Culture
The next step in our improved reliability plan deals with the culture of your department. We've described why we were retraining and why closeout notes were so important. Our reasons for why had to do with our current CMMS becoming obsolete, and the new software we were trying to replacing it with.
Many users then came forward and explained that since they understood what was going on they were much more open to changing and trying the new software. This also gave us a chance to describe how this fit with the bigger picture of being proactive and not reactive.
We also explained that closeout notes are our way for the technician to send information back to the reliability group or planners when something is wrong. This was very important for them to understand, which also gave them a chance to vent about instances when they had used the notes but didn’t see any change.
Leadership Behavior
The last step in the process of setting clear expectations. This has less to do with the technicians and more to do with the management in the department. Which management behaviors will help build the culture that drives team behaviors to reach the desired vision? So what can leadership do?
In our case, we challenged management to conduct daily reviews of work orders that had been completed. We provided them with a dashboard they could use to check if the techs had entered their closeout notes, labor, and parts. This verification step helps round out the circle of the expectation.
We have found through this process that this is also a critical step that can’t be underestimated. I am not sure about all other facilities, but in our plant, everything lives and dies with frontline supervision. They set the tone for the culture. So, it is important that they are clear on expectations and what it may involve to reach them.
Conclusion
Setting expectations is the foundation of what a healthy reliability program is built on. These expectations will guide you through the tough times when you are transitioning between being reactive to being proactive. Start with your desired vision and what the technicians' behaviors will look like in order to accomplish the vision.
Make sure to give the why behind the expectations and train your management on any adjustments to their process to better reflect the improved company culture. Missing anyone of these steps could cause setbacks in your reliability implementation plan. And that starts with you.
So, take a little time to make sure you're not the problem.
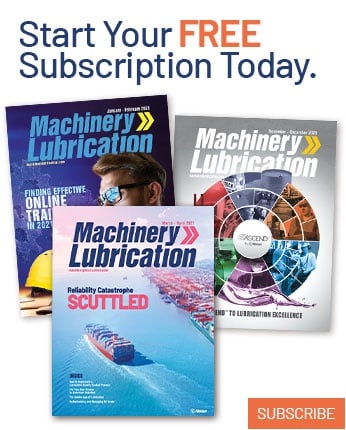