Manufacturing plants are facing a convergence of extreme challenges: an aging workforce coupled with the transfer of knowledge, increased demands for higher quality products utilizing fewer resources and the pandemic. Navigating these issues is critical to maintaining ongoing operations and controlling costs. If something additional happens, such as unplanned equipment downtime, the results can be a logistical nightmare and financial disaster. But it’s certainly not all doom-and-gloom. The adoption of innovative technology is playing a critical role in mitigating unexpected problems and staffing challenges.
Manufacturing Workforce
U.S. manufacturing is in the thick of an expected shortage of two million workers between 2015–2025, according to a report from Deloitte and the Manufacturing Institute.[1] A 2017 industry study sponsored by Advanced Technology Services found that the leading cause of unscheduled downtime within respondents’ facilities was aging equipment (42 percent), followed by operator error (19 percent) and lack of time needed to perform necessary maintenance (13 percent). Of all the core disciplines affected by the shortage of trained personnel, machine maintenance may be the most troublesome for manufacturing plants. Thirty-five percent of U.S. manufacturers are currently seeking maintenance technicians, and an even higher percentage are shifting at least some maintenance responsibilities to operating personnel—a potentially dangerous tactic at a time when equipment is becoming increasingly automated and complex.
According to the National Association of Manufacturers’ most recent outlook survey, attracting and retaining a quality workforce constitutes one of the top challenges facing the manufacturing industry.* This industry faced a labor shortage exacerbated by the aging of the [manufacturing] workforce and gradual retirement of the baby boomer generation—as of 2017, nearly one-quarter of the sector’s workforce are age 55 or older. Additionally, 97 percent of respondents reported that they feared losing institutional knowledge when [older] workers depart. The study also examined the innovative approaches manufacturers can use to extend older workers’ productivity and help transfer institutional knowledge to the next generation.
Manufacturing jobs are becoming more complex, including the maintenance of the hi-tech plant equipment. However, the answer to the labor shortage and transfer of knowledge may be rooted in additional technology.
Unplanned Downtime
Millions of dollars are invested each year in capital improvements to facilities and equipment to increase product safety, protect employees and reduce costs, which is important since equipment in a typical food processing plant, for example, may run 16 to 20 hours a day, every day. Equipment failure is the most common cause for downtime. Unplanned downtime can cost a food processing facility an astounding $30,000 per hour[2] and, according to analyst firm Aberdeen Research, manufacturing facilities in general an astounding $260,000 per hour.[3] A Deloitte industry report cited recent studies that show unplanned downtime costs industrial manufacturers an estimated $50 billion annually. However, downtime can cost a company more than just money – it can be a logistical nightmare.
As the world grapples with the effects of COVID-19, manufacturing plants are under more pressure than ever to maintain ongoing operations. In the United States, many industries have been deemed essential, and state and federal authorities are working to keep supply lines intact. However, given that maintenance worker shortages existed even before the pandemic, what can plants do to mitigate unplanned downtimes?
Remote Monitoring
One strategy to help resolve this is for manufacturing plants to invest in technology for areas with worker shortages, such as sensors that monitor whether a machine is working properly instead of having someone possibly crawl under equipment to check out a problem. Another way is using remote alarm notification software, which allows fewer people to monitor many more assets using devices that people already have, such as smartphones and tablets. Uninterrupted remote availability is essential to ensuring systems can be continuously monitored, even without staff onsite or with fewer people working at the facility.
WIN-911 remote monitoring software utilizes a variety of communication platforms to send notification from the plant equipment to the person responsible.
Remote monitoring of critical plant systems has been extended beyond email, texts and phone calls to include apps that feature time-saving tools like real-time alarm acknowledgements, team chats to troubleshoot and resolve plant problems, and detailed reporting for preventing future incidents. Not only does this mean fewer emergency shutdowns, but also fewer resources spent on overtime and maintenance. A mobile alarm notification app is software that seamlessly integrates with the SCADA or HMI software of an industrial operation, allowing an employee to monitor, receive and acknowledge plant and machine alarms on their smartphones or tablet, freeing them up to work from home or any other remote location.
Image Caption: Push notifications let workers quickly see what is wrong, send an acknowledgement, and monitor alarm condition changes in real-time, right from a smartphone.
Hardware and software are available that can constantly monitor equipment and, by applying machine learning to historical data, warn when a breakdown or other problem is imminent. Bolstered by wireless technology and IIoT, these customizable systems have the potential to bring predictive maintenance to a new level.
The benefits of utilizing a remote monitoring and notification software system via a mobile app include:
- Streamlines decision making. Push notifications let users quickly see what is wrong, send an acknowledgment, and monitor alarm condition changes in real-time, right from smartphones.
- Promotes team problem solving. Chat helps the entire team converse, brainstorm, and share solutions on-the-fly, from anywhere — whether in the plant, at home, or on the road.
- Work more efficiently. Team Visibility shows who has seen an alarm as well as who has acknowledged it, reducing guesswork and redundant responses.
- Multiple communication channel support. Ensuring resiliency through voice notification and SMS messaging in the event of internet connectivity issues.
Image caption: Chat helps your entire team converse, brainstorm, and share solutions on-the-fly, from wherever they are—whether in the plant, at home, or on the road.
Critical Need
Manufacturing plants in a variety of industries have become more critical than ever before. For example, pharmaceutical companies manufacturing COVID-19 vaccines, medical refrigeration manufactures, food processing plants, and other industries that are retooling and manufacturing under the Defense Production Act are all essential during these unprecedented times. Through the installation of remote alarm notification software, manufacturers can move from reactive to a more controlled, prescriptive maintenance approach.
* The study was conducted prior to the pandemic at which time the country was experiencing an extended economic expansion and record-low unemployment.
[1] Rose Shilling, “Worker shortage has processors scrambling to hire and keep good employees,” Food Engineering, May 22, 2019.
[2] https://www.wipfli.com/insights/blogs/manufacturing-tomorrow-blog/170628---the-real-cost-of-unplanned-downtime (accessed January 16, 2020).
[3] “The Actual Cost of Downtime in the Manufacturing Industry,” November 14, 2018, IIOT World.
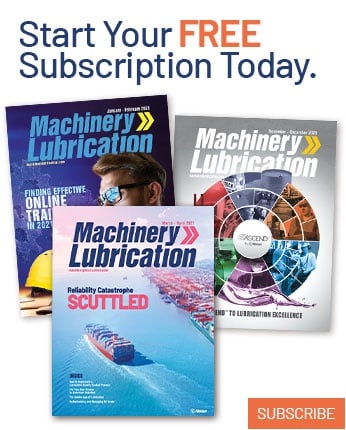