Augmented Reality (AR) and Virtual Reality (VR) are reshaping our interactions with technology. Offering more than just entertainment, these innovations provide immersive experiences that blend digital and physical experiences. They offer a new way of interacting with our surroundings, extending beyond traditional uses.
The industrial sector faces a unique set of maintenance challenges. Keeping intricate machinery running smoothly is essential but often complex. Efficient maintenance solutions are crucial for maintaining productive industrial facilities — and many of these solutions incorporate AR and VR technology.
With AR and VR, maintenance practices are undergoing a significant transformation. These technologies are not just futuristic concepts. They provide practical solutions to traditional maintenance issues, like enhanced troubleshooting, training, and predictive maintenance strategies, paving the way for more effective methods.
Tip 1: Real-time Data Overlay with AR for Efficient Troubleshooting
Through AR overlays, digital information is seamlessly merged with the physical world, adding a new dimension to objects. This technology enhances users' perception by providing additional data directly in their field of view. It acts like a real-time guide, highlighting crucial information as the user completes a task.
For maintenance personnel, real-time data is transformative. It streamlines decision-making processes, allowing quicker and more accurate troubleshooting. Immediate access to essential information leads to increased efficiency and fewer errors in maintenance tasks.
Bosch and Boeing are leading examples of how AR is revolutionizing maintenance. Bosch’s innovative AR solutions offer interactive guides that simplify complex tasks. Boeing’s adoption of AR for intricate operations like aircraft wiring has resulted in faster completion times and a significant reduction in errors.
Tip 2: VR for Training and Simulation
Effective training is vital in maintenance, particularly where precision is crucial. It's the foundation of high safety standards and smooth machinery operation. Proper training equips personnel with the skills needed to confidently tackle maintenance challenges.
VR is transforming training in maintenance. By simulating real-world scenarios in a safe environment, it provides a platform for in-depth and risk-free skill development. This approach allows trainees to practice complex procedures without real-life risks, enhancing both their skills and confidence.
VR training modules are making a significant impact in fields like energy management. For instance, technicians training for wind turbine maintenance now have the opportunity to practice in virtual environments. This type of training not only ensures safety but also improves overall maintenance efficiency and preparedness.
Tip 3: Remote Assistance Through AR for Complex Repairs
AR allows for expert assistance to be provided remotely. Specialists can see what field technicians are viewing and offer real-time guidance. Distance no longer hinders access to expertise, making it easier to tackle complex repairs effectively.
This approach to maintenance greatly reduces downtime and cuts costs. With AR-enabled remote assistance, complex repairs are completed more efficiently, decreasing the need for repeat visits and reducing equipment downtime. It's an approach that not only saves time but also has a positive financial impact.
Moreover, AR in remote assistance empowers technicians to broaden their skill set by learning from experts in real-time. This continuous learning approach can potentially enhance workforce capabilities. As technicians become more adept at handling a variety of complex issues, the overall reliability and performance of the equipment improve.
Tip 4: Integrating AR and VR into Predictive Maintenance
Predictive maintenance is a strategic approach that focuses on preventing equipment failures before they occur. Utilizing data analysis, this method anticipates potential issues, allowing for timely interventions. It represents a shift from reactive to proactive maintenance, ensuring equipment operates at peak efficiency.
AR and VR have significantly transformed predictive analytics in maintenance. These technologies present complex data in visually intuitive formats, making it easier for technicians to understand and act upon. Enhanced data visualization leads to more accurate predictions and timely maintenance actions.
A significant shift toward proactive maintenance is marked by integrating AR and VR into existing practices. These technologies offer detailed insights into the health and performance of equipment, enabling technicians to foresee and preemptively address potential issues. Such integration not only reduces downtime but also extends the life of machinery, ensuring smoother operations for smart manufacturing.
Challenges and Solutions in Implementing AR and VR
While the potential of AR and VR in transforming maintenance practices is immense, implementing these technologies comes with its own set of challenges. However, with every challenge, there are viable solutions that can pave the way for successful integration.
- High initial costs and investment— Seek partnerships with tech providers, explore government grants or subsidies, and phase implementation to manage costs effectively.
- Technological compatibility and integration— Conduct thorough assessments of existing systems, choose scalable and adaptable AR/VR solutions, and ensure regular updates and maintenance of the software.
- Training and skill development— Implement comprehensive training programs for staff, use online resources and workshops, and consider hiring specialists with AR/VR expertise.
- Hardware maintenance and upgrades— Establish contracts with hardware providers for regular maintenance, stay informed about the latest hardware advancements, and plan for periodic upgrades.
Successfully overcoming these challenges requires a balanced approach that combines strategic planning, stakeholder engagement, and a focus on continuous learning and adaptation.
Addressing user acceptance and safety concerns is also important in implementing AR and VR. Prioritize creating a user-friendly experience, with interfaces that are intuitive and easy to navigate. This includes environments that are realistic yet not overwhelming, to ensure a smooth transition for technicians.
Additionally, establish clear safety protocols for using AR/VR equipment, especially in hazardous or complex work environments, along with regular feedback sessions with users.
Conclusion
This article explored four innovative methods in which AR and VR are enhancing maintenance practices. Looking ahead, the integration of AR and VR in maintenance promises a future rich in efficiency and innovation. As these technologies continue to develop, they will further alleviate maintenance challenges and minimize downtime.
AR and VR have proven to be more than just sophisticated technologies; they are critical tools that enhance both the educational and practical aspects of maintenance. Transforming complex data into accessible insights and providing realistic simulations for training, these technologies are revolutionizing not just how maintenance tasks are performed, but also the overall approach to maintenance education and strategy implementation.
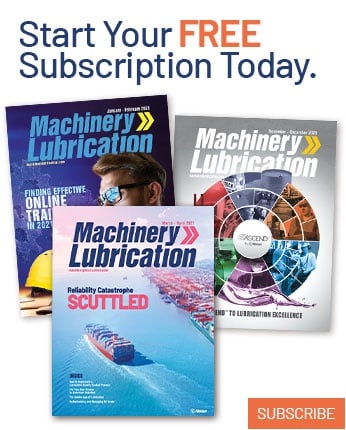