Technologies for monitoring machine-vibration levels have been around for decades. The further development of such technologies has been relatively slow, but the rapid advancement of digital component technologies in recent years has brought new opportunities. The innovative HD vibration technology from SPM Instrument breaks new ground in more ways than one.
Vibration Data Like No Other
Thanks to highly advanced and patented digital algorithms, the game-changing HD ENV® vibration-enveloping technology is extremely sensitive to changes in vibration levels, making it possible to identify very early-stage gear and bearing faults and closely monitor their continued development. There are cases where this technology has provided up to three years’ forewarning time of deteriorating mechanical condition in critical assets. HD vibration data has become a tried-and-true enabler for optimized maintenance scheduling, enhanced asset integrity, increased productivity, and higher profits.
Driven by Technology – Enabled by Curiosity
The extraordinary data quality is the hallmark of SPM Instrument’s HD vibration technology, taking vibration analysis into the age of high-definition resolution. When collecting data for condition-monitoring purposes, a wealth of additional information comes with it. By carefully monitoring, examining, and following up on data patterns not connected to well-known mechanical machine problems, SPM engineers were able to conclude that these patterns can reveal details about machine or process performance and efficiency.
This discovery has opened up a whole new area of application for the high-definition data of the HD ENV® technology.
Beyond Condition Monitoring – Using High-Definition Data for Process Optimization
Keeping the production equipment up and running smoothly and without mechanical issues is paramount in any process plant, that goes without saying, and this is the justification for condition monitoring. However, many other factors influence productivity and results beyond staying on top of asset reliability.
Process optimization aims to produce the greatest amount of output with the highest possible quality at the lowest possible amount of input resources. Equipment and processes performing at a sub-optimal level can cause production inefficiencies, quality problems, and higher-than-necessary energy consumption, to name but a few adverse effects. The opportunity to gain actionable insights beyond the mechanical condition of critical machinery based on vibration data brings significant potential for data-driven process improvements.
Process optimization solutions with the HD ENV® technology enable process industries to enhance new areas of their production, thereby contributing to:
- Increased production speed
- Increased raw material yields
- Maximized availability
- Enhanced plant condition
- Health, safety, and environmental improvements
SPM’s R & D Manager Johan Nilsson: “Compared to conventional vibration monitoring technologies, HD ENV® knocks it out of the park. Our process optimization solutions build on a legacy of well-proven, field-tested technology, and we are continually exploring new opportunities to truly put our customers’ vibration data to work for them. By employing process optimization, companies can boost the bottom line and enhance their competitive edge.” Process optimization data are presented in clear and visually appealing web-based dashboards and can be integrated into control systems via REST API or OPC UA.
Process Optimization and Reliability for Smart Mines
As SPM Instrument now turns its extensive technical expertise into process optimization, the mining and mineral processing sector is the first to take advantage. This heavy-asset, energy-intensive industry stands to make considerable gains from process optimization. Below are two examples of HD ENV® process optimization capabilities that greatly benefit the mining industry.
Maximizing Grinding Efficiency and Throughput in Tumbling Mills
A critical success factor in optimizing the efficiency and performance of the grinding process is mastering the toe position of the mill charge. Toe-position monitoring is a process optimization tool for detecting the early onset of an overload condition in tumbling mills. It provides insight into charge dynamics and enables operators to optimize comminution efficiency. Even a slight increase in throughput can impact the bottom line dramatically.
The overall purpose is to keep the mill running as close as possible to maximum working capacity while at the same time avoiding the risk of mill overload, underload, and freewheeling. Providing high-resolution toe position data with exceptional accuracy, the solution effectively allows operators to determine the ideal feed rate for optimal grinding conditions.
Optimizing the toe position also positively impacts particle size distribution, an essential parameter for the efficiency of the separation stage.
Further benefits include the monitoring of the following:
- Inlet/outlet toe position – outlet blocked; difference inlet/outlet
- Wear-and-tear on the liner and lifters
- Density
- Big rock occurrence
- Easy and robust installation (two vibration sensors and one tachometer – no hardware attached to the shell)
- Early detection of fault modes
The toe-position monitoring solution measures the position of the charge toe with exceptional accuracy, using vibration measurements with patented HD condition-monitoring technology. The toe position usually differs at the inlet and discharge ends of the mill. This solution is unique in that it measures vibration at both ends rather than at a single position.
The installation is straightforward and robust, without any equipment attached to the mill’s rotating shell. A single vibration sensor on each side of the mill’s main bearings measures the lifter signature, while a tachometer provides a reference signal. Charge-toe position data is displayed in a dashboard, updating the information approximately every fifteen seconds.
The update interval varies depending on the mill’s rotational speed. As an added benefit, the dashboard also indicates the charge-toe area density.
Unique, Data-Driven Optimization of the Screening Process
For mining operators, productivity, safety, and environmental impact are ongoing challenges. At the heart of a mineral processing operation, the vibrating screen is a critical piece of equipment, the performance of which can influence all these factors. For optimal screening performance, uniform movement of the screen corners is crucial. The motion of the corners in relation to each other highly impacts throughput and production rates.
The vibrating screen-performance monitoring solution is a process-optimization tool for visualizing screen motion. It provides insight into the dynamics of the screening process and enables operators to optimize its efficiency.
The screen-performance monitoring solution detects unfavorable screening conditions that can cause various problems, including:
- Plugging and blinding
- Mechanical stress
- Excessive energy consumption
- Process capacity losses
A well-functioning vibrating screen limits the wear rate, extending its working life and reducing downtime costs for manually cleaning the screen decks. The screen-performance monitoring solution provides a clear picture of the screen’s orbital motion of the four corners.
It also measures the maximum deviation across all corners, providing important information about potential structural stress. The solution is useful for finding out if the screen performs at full capacity and is an excellent aid to help maintenance and production personnel troubleshoot and get the most out of this essential piece of equipment.
The screen-performance monitoring solution collects vibration data from each corner of the screen, using vibration measurements with patented HD condition-monitoring technology. Measuring results are displayed in a dashboard as easily understood orbit plots and trend graphs. The hardware installation comprises a single triaxial vibration transducer with sealed connectors and cable protection conduits installed in each corner of the screen, with an inductive proximity switch on the exciter shaft.
The transducers are connected to a high-performance, 16-channel online system unit. The remaining four channels can be used to monitor other parameters.
A portable monitoring solution is also available for service providers or plants with multiple vibrating screens. Orbit data is stored in SPM’s analytics and diagnostics software database, locally or in the cloud, from where it can be integrated into process control systems or remote data centers.
Process Optimization and Condition Monitoring – A Winning Combination
Using high-definition process data to boost manufacturing processes ties in perfectly with condition monitoring and is a winning strategy. In industries with high production costs, combining the benefits of condition-based maintenance with those achieved through process optimization is a formula for success in the quest for higher profits.
A well-designed, well-implemented condition monitoring program paired with successful optimization of critical processes brings out the best in both assets and production, thus enabling plants and operations to leverage new opportunities for increased profitability and business growth. The opportunity to gain actionable insights beyond the mechanical condition of critical machinery based on vibration data brings significant potential for data-driven process improvements. Moreover, manufacturing and process industries can achieve this in two strikes with one pitch because it is done with the same leading-edge technology and solutions used for condition monitoring.
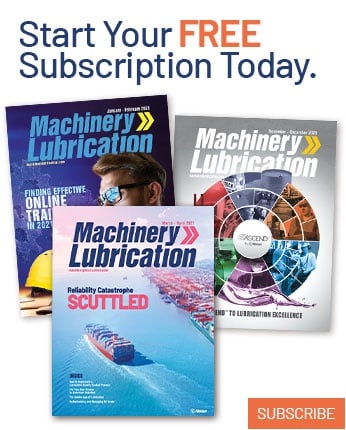