LafargeHolcim recently announced that it will launch a new “Plants of Tomorrow” initiative to upgrade its production fleet for the future. Targeting a global network of more than 270 integrated cement plants and grinding stations across more than 50 countries, the company will be utilizing automation technologies and robotics, artificial intelligence, predictive maintenance and digital twin technologies for its entire production process. The four-year program is one of the largest roll-outs of Industry 4.0 technologies in the building materials industry.
A “Plants of Tomorrow” certified operation will show 15 to 20 percent of operational efficiency gains compared to a conventional cement plant. LafargeHolcim is presently working on more than 30 pilot projects covering all regions where the company is active. The company’s integrated cement plant in Siggenthal, Switzerland, will be the lighthouse where the integration of all relevant modules will be tested for the global initiative.
“Transforming the way we produce cement is one of the focus areas of our digitalization strategy, and the ‘Plants of Tomorrow’ initiative will turn Industry 4.0 into reality at our plants,” said Solomon Baumgartner Aviles, LafargeHolcim’s global head of cement manufacturing. “These innovative solutions make cement production safer, more efficient and environmentally fit. We are moving to fully data-driven operations in order to support further profitable growth as part of our Strategy 2022 – ‘Building for Growth.’”
Among the technologies to be implemented are predictive operations that can detect abnormal conditions and process anomalies in real time. This will reduce maintenance costs by more than 10 percent and significantly lower energy costs. Digital twins of plants are created to optimize training opportunities.
Automation and robotics are another important element of the strategy. Unmanned surveillance is being performed for high-exposure jobs in the plant. Partnering with Swiss start-up Flyability, the company is using drones that allow the frequency of inspections to increase while simultaneously reducing costs and improving safety for employees by inspecting confined spaces. The concept is now being rolled out to several markets including the United States, the United Kingdom, Switzerland, France, Germany, Canada, India and Russia.
LH MAQER, the company’s new platform to identify the most impactful technologies and target start-up technology companies, also aims at establishing new partnership models with both manufacturing and software companies.
“Our global manufacturing expertise in cement is second to none,” said Philipp Leutiger, LafargeHolcim’s chief digital officer. “Now, with our LH MAQER platform, we open up our operating model to the creativity and ingenuity of some of the world’s most gifted and talented digital minds. We are already seeing the success of this approach in many of our operations globally.”
LafargeHolcim has already launched technology to track performance centrally and allocated resources to support the plant network in real time. More than 80 percent of the company’s cement plants are already connected to its technical information system that provides data transparency at the plant, country, regional and global level. Some country operations have more than a decade of historic technical data available. Other systems allow the remote control of certain parts of the operations through online condition monitoring systems. Since its implementation in 2006, this system alone allowed for more than $80 million in savings and an additional 3 million tons of cement sold through less breakdowns.
For more information, visit www.lafargeholcim.com.
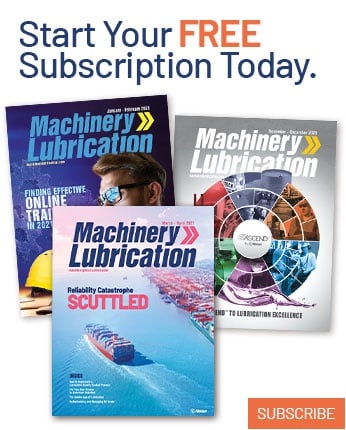