Modern manufacturing plants are implementing an ever-growing assortment of asset condition monitoring technologies in production and facility equipment. Several of these technologies incorporate diagnostic sensors built into or connected to production equipment via a network.
While these technologies can detect problems and notify maintenance staff, many facilities lack a coherent method of addressing the information and creating actionable plans to correct problems. By utilizing predefined preventive maintenance (PM) and repair procedures linked to specific error codes within a computerized maintenance management system (CMMS), you can automatically initiate repair work and resolve issues quickly.
Evolution of CMMS
Computerized maintenance management systems were originally developed to identify and define the procedures needed to be performed on assets to assure continued operation. The planned maintenance procedures defined the tasks, resources, parts, tools and instructions required to complete the procedures.
Schedules were defined and linked to procedures to determine how often planned maintenance work was performed. Time- or calendar-based schedules eventually were expanded to include counters or meters that could more closely define the actual use of an asset. Odometers and machine or line counters were the next method of scheduling planned maintenance work within a CMMS.
After World War II, numerous studies were done on the effectiveness of scheduled preventive maintenance work over time. The results of four major research projects became the basis of reliability-centered maintenance (RCM). All four studies arrived at the conclusion that calendar- or meter-based PM scheduling was only effective in reducing 10-30 percent of all failures. This meant that 70-90 percent of unplanned failures were not prevented by scheduled PMs.
During the 40 years since RCM was defined, technology has created an amazing array of methods and devices capable of identifying potential equipment failures. Vibration sensors, accelerometers, infrared scans, oil analysis and other devices and tests are now available to help pinpoint potential equipment failures.
In particular, analog and digital sensors are either built into or permanently installed on machinery to monitor specific components and conditions while in operation. The challenge for maintenance managers is how to put all of this data to use to reduce.
CMMS was among the first applications developed after the advent of personal computers (PCs). CMMS software allows maintenance managers to identify all the assets they are responsible to maintain and define the procedures, tasks, parts, resources and schedules needed to perform preventive maintenance work.
CMMS was originally designed to distribute PM tasks on paper work orders that were returned after completion and registered on the CMMS system. The paper work order paradigm is rapidly changing with the advent of laptop PCs, tablets and smartphones. Even today, a preponderance of all work orders generated by CMMS systems are for calendar- or time-based preventive maintenance procedures.
Condition Monitoring
Sensors can detect wear, temperature, vibration, etc., and PMs can be triggered based on data they send from the assets. By knowing what data the sensors can provide, you can determine when and what preventive or corrective procedures should be done. Using condition monitoring sensors, it’s now possible to send sensor data directly to a CMMS to initiate preventive or corrective work orders.
To simplify this concept, imagine your car is idling roughly and you’re pretty sure something is wrong with the engine. The check engine light then turns on in your car. The next step is to connect a scanner to the onboard diagnostic harness and read the error codes. For any given error code, a repair or maintenance procedure can be created in a CMMS system to fix the cause of the code.
Procedures include all the parts, tools, tasks and instructions required to correct the problem. If you were able to connect a scanner to the CMMS, you could automatically generate work orders to address any specific error code.
In a factory environment, machine sensors are connected to programmable logic controller (PLCs) through a network (or the internet) and supervised by applications that can communicate with the CMMS to generate preventive or corrective work orders.
To get started, first identify all your critical assets that have condition monitoring devices and determine what condition monitoring data can be used to trigger a preventive or corrective work order. Next, define the threshold parameters that will be used to trigger preventive or corrective work orders and determine the types of procedures needed to address the condition monitoring data.
Finally, create preventive or corrective procedures in the CMMS system to address the conditions and link the data collection network to the CMMS either directly or via middleware.
Linking Data from Sensors to CMMS
Identify the assets that have condition monitoring capabilities, whether they be mechanical, analog, digital, etc. The example below is for a robotic welder.
Once the assets are identified, define the sensor or condition code output that you want your CMMS system to use to trigger a PM or corrective procedure.
While most CMMS systems are utilized to schedule and perform preventive maintenance procedures, many allow users to define various types of procedures limited only by your imagination. Typical procedure types needed to address incoming sensor data include inspection, safety, planned maintenance, corrective maintenance, troubleshooting/diagnostic, calibration and auto-generated by trouble code.
Create Procedure Types in Your CMMS
Once you’ve defined the types of procedures to address your anticipated conditions, start creating procedures for each condition code in your CMMS. Procedure definitions include tasks, resources, parts, tools, instructions, pictures, videos, diagrams, hyperlinks to web resources, schedules for calendar-based PMs and trigger conditions for condition-launched procedures.
Define Procedures in Your CMMS
After the assets are identified, code parameters established and procedures defined, the CMMS must be linked to the condition monitoring network or application. There are many ways to link networks and systems.
In the example above, special software was used to connect and convert PLC/SCADA data into a format that Microsoft applications can read. Microsoft Task Manager was also utilized to define the frequency the CMMS would poll the condition monitoring network/application to update the current code status.
Once a code is received that falls within the range to trigger a procedure, the CMMS can be programmed to wait for a specified amount of time before the procedure automatically launches a work request in the CMMS system.
The benefits of linking condition monitoring data to your CMMS include quicker repairs, saving time and money by fixing only the part that needs to be repaired, less downtime, reducing unnecessary PMs, and extending the time between PMs, which increases available maintenance tech time for other work.
In the future, sensors will become much smaller, less expensive and include expanded capabilities. More manufacturers, machine owners, technicians, schools, etc., will also be contributing condition monitoring information, creating an even larger big data pool for analysis. Finally, improvements in artificial intelligence (AI) will allow more incoming sensor data and even more precise diagnostics.
This article was previously published in the Reliable Plant 2019 Conference Proceedings.
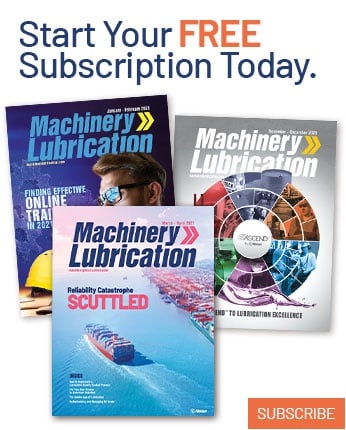