Many of the vibration data collectors of today have the capability to support two or more sensors gathering data simultaneously. With this capability is the ability to select cross-channel phase as an analysis tool.
Other than the analyzer and cable with a sensor used for normal vibration routes, the only additional tool needed to perform cross-channel phase is another cable and sensor. Cross-channel phase analysis can enable the discovery of sources of structural looseness, some structural integrity issues, misalignment conditions and even structural resonance conditions.
How Does It Work?
Normal route data acquisition captures multiple sine waves and separates them according to frequency. It then displays them as separate frequencies with their individual amplitudes in spectral format.
Phase analysis picks a single sine wave (single frequency) and detects how that vibration source is moving relative to something else. The “something else” could be a spot on the shaft, such as reflective tape or a key phaser, or another vibration signal as in the case of cross-channel phase.
So there are two signals that are compared: the vibration signal and a tachometer pulse triggered by the passing of the reflective tape, or pulse from a key phaser, for example. A tachometer pulse creates a square wave, while the vibration signal sends a sine wave.
The peaks of the two sources are compared for timing, and the time difference between the two peaks is displayed in degrees, since both sources are related to rotational motion. This works perfectly for balancing rotating equipment, because from the pulse from the leading edge of the reflective tape, the peak of vibration (or high spot) occurs so many degrees later, indicating the likely heavy spot on the shaft. (This article does not address conditions that can cause the heavy spot to be different from the high spot of vibration. Just be aware that can be the case.)

With two sensors being used in cross-channel phase, the comparison is the peak of vibration of each signal. Analyzers that have the ability to do cross-channel phase also allow you to specify the particular frequency to monitor. Most often the shaft-turning speed is selected as the frequency of interest.
A typical starting point is to place sensor A at the outboard vertical end of the motor and sensor B on the motor foot to see how those points are moving relative to each other. It is common to keep one sensor in the same place, i.e., position A to compare to several other points. For the following examples, we will assume sensor A is reading zero degrees.

If sensor B is reading zero degrees (+- 30 degrees), then they are moving together or in unison, which is a normal condition that is expected. However, if sensor B is 180 degrees (always +- 30 degrees), then it is moving in the opposite direction or out of step. This means part of the motor housing is moving in an upward direction while the foot is moving in a downward direction. This is caused by a crack in the motor housing somewhere, allowing parts to separate. Most often, the crack is at or near the foot. Document your findings.
Now move sensor B to the foot bolt. If sensor B reads zero degrees, the plate the bolt is fastened to is moving in unison with the top of the motor, interpreted as the bolt is tight.
However, if the foot is zero degrees and the bolt is 180 degrees (or 180 degrees out of phase), there is looseness there between the foot and the mounting plate.
The same process can be determined for the base and the floor. If all these read the same as sensor A, there is no looseness between any two of these locations.
Next, move sensor A to the motor inboard position and perform all the same checks on that end of the motor. Once that is completed, move sensor A across the coupling to the pump inboard end and then the pump outboard, performing checks there. Be sure to document your findings at each position for later reference and analysis as needed.

The next step is to compare readings along the machine train from one end to the other. This should be done in the vertical sensor direction as well as horizontal sensor direction. Some questions arise as to why both directions. That can be answered with another question, “Is it possible for a machine to be in alignment vertically but not horizontally?”
Let’s look at scenarios with sensor B moving from bearing to bearing along the machine train in the vertical direction.
Again, assume sensor A is stationary and is reading zero degrees for all these measurements, roam with sensor B. The first B position is motor inboard vertical. If sensor B is zero degrees, then this position is as it should be with no problems. However, if sensor B reads 180 degrees, this end of the motor is moving down while the A end is moving up. This is not a good condition. One condition that can cause this angular misalignment.
To verify angular misalignment, move sensor B to the pump inboard position. If it reads 180 degrees there, then it is very likely an angular misalignment condition, because in angular misalignment the shafts move in unison across the coupling. Assume for this example we do have the indications of angular misalignment. What is the pump outboard bearing expected to be reading?
Moving sensor B to the pump outboard bearing location, we expect the reading to be zero to confirm the angular misalignment. In the absence of a misalignment condition, we expect all the bearings to be in-phase or reading zero.
The same checks can be made in the horizontal direction by positioning the reference sensor, sensor A, to the motor outboard horizontal direction. Do the comparisons, documenting all readings and moving sensor B from bearing to bearing in the horizontal direction on the same side of the machine. What happens when the sensor is placed on the opposite side of the machine?
What useful information would axial direction phase readings provide? Let’s consider the possibilities. Place sensor A in the axial direction at the motor inboard bearing and sensor B at the pump outboard position in the axial direction, and compare the phase readings. If they are in-phase, this is as expected. However, if they are 180 degrees out of phase, that points to an angular misalignment condition where the shafts are pushing against each other as they rotate. Just as in normal vibration readings, axial phase measurements can be used to confirm a misalignment condition.

A similar phase reading comparison method can be used to check the structural condition of the machine base to see how it is moving. Typically, the A sensor is mounted in the vertical direction on the motor outboard bearing and sensor B is used to roam along the base.
Beginning at the motor end of the base place, sensor B is near the front corner of the base. The phase reading will likely be in-phase with sensor A if all the vertical readings at that location were in-phase. Now move sensor B along the front of the base near the edge in 2- or 3-inch increments recording the phase readings. If they are all in-phase, there is no flexing problem.
Next, move sensor B to the back side of the machine and repeat the measurements along the base there. Again, if everything is in-phase, there is no problem with the base flexing.
But what is going on if along the length there is a 90-degree or 180-degree phase shift in the region between the motor and pump? There could be a 180-degree phase shift or a 360-degree phase shift between one end of the base and the other end. What could this indicate?
What would be indicated if there is a 180-degree phase shift from a measurement along the front side to a corresponding positon along the back side? Would it be a problem? Why or why not?
What About Amplitude?
Phase readings typically have two components that are available. One is the actual phase reading at a frequency in degrees, which has been introduced here. The other component is the vibration amplitude. In some analyzers, the selection for setting up for phase readings is called peak and phase, the peak amplitude of vibration and the phase reading. The phase reading indicates the direction it is moving, but the amplitude indicates how much it is moving.
In the illustration below, there are circles along the base with a tic mark on the outside of the circle. The tic mark indicates the phase direction. Inside the circle are vibration values in velocity, the typical vibration reading for that frequency. Notice that starting from the left, the vibration amplitude is 0.114 inches per second. As it progresses to the center of the baseplate, the amplitude rises to about 0.954 inches per second. The amplitude decreases again as it moves along to the right. The phase stays constant the entire distance. Is there a problem?

Yes, this points to a base stiffness problem that allows it to move more in the center. Is it grouted the way it is designed to be? Get an engineer involved to design a way to stiffen the base that does not adversely affect any other areas.
There are those who would say that the increased vibration in the area indicates it is in a resonant condition. However, any time resonance conditions or natural frequencies are involved, there is a phase change. With essentially zero phase change, the resonance is ruled out.
Summary
Cross-channel phase is a valuable tool built into most two-channel analyzers that enable the technician/analyst to find or verify some machinery problems. An understanding of how the machine should move is very helpful in diagnosing/confirming the conditions.
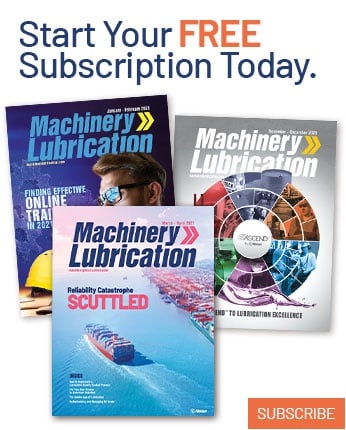