Here's a situation that's not uncommon. As a maintenance manager or plant manager, you know there's something wrong with maintenance. You see two or three tradespeople doing work that requires only one, people hanging around the storeroom or leaving early, work being done that's of questionable value, and no one can give you a good work schedule. Reliability is fine, but you suspect that it’s costing more than it should to achieve.
Your immediate thought is that the planning and scheduling of maintenance work needs to be improved. However, by improving planning and scheduling, you know that your tradespeople will become more productive. So if nothing else changes, more work will get done, more materials will be used and costs will go up.
You also recognize that if you try to balance the increased productivity by reducing your maintenance workforce, the reaction will wipe out any gains you are trying to make. In fact, you may already have committed to no layoffs.
So how do you reduce costs by moving to a more professional approach to maintenance management through better work planning and scheduling without reducing your workforce? One way is to reduce manpower through attrition. Most maintenance departments are concerned about the impending loss of experienced tradespeople as they retire and are having difficulty finding skilled replacements. The option is to improve the effectiveness of a smaller workforce to achieve the same results as your current level of manpower.
Unfortunately, attrition takes time. It may be five years or more before you reach the new target manpower level. In addition, it is almost impossible to match the rate of improvements in efficiency to stay in balance with that reduced manpower over such a long period of time.
There are alternatives. The most successful approach is to make a sudden reduction in the number of tradespeople available for maintenance work by assigning a significant number to an "untouchable" project crew. This project crew is assigned only to work that would otherwise have been executed by a contractor.
This takes careful planning, experienced supervision and some special training. However, when you consider the savings that can be achieved by avoiding contractors, any costs associated with these actions will have a good return.
The introduction of this new crew may also provide an opportunity to address any restrictive trade practices that are not protected by union agreements.
As with any change, some resistance can be expected, so strong leadership is essential. However, resistance is unlikely to come from your good tradespeople, many of whom will have been frustrated by having to find ways to get through the day without getting too bored. Most tradespeople in the new crew will find that their project assignments are more interesting than many maintenance routines and provide learning opportunities.
The greatest resistance will come from the union, because the change will eventually result in a reduction in their membership and their revenue. Of course, it is necessary to respect any agreements that are in place, but those agreements usually provide considerable freedom for improving performance.
There may also be resistance from some supervisors and planners, because they will quickly see that they will be expected to change the way they work (perhaps substantially) and that the focus will be on them. They must be involved in all aspects of this change.
It goes without saying that the introduction of a project crew and the corresponding reduction in maintenance tradespeople must be preceded by training and (perhaps) organization and system changes to provide the required level of professional work planning and scheduling.
There are other opportunities to reduce costs by assigning tradespeople to activities that have value but do not use any materials. Examples include training, updating and improving the preventive maintenance program, eliminating obsolete stock from your storeroom, renaming stock items so tradespeople can easily find them, preparing standard job plans for repetitive work, and developing standards for equipment rebuilding.
However, most of these "projects" will have an end, so if attrition is expected to occur at a reasonable rate, the schedule for completing these activities should balance the anticipated manpower reductions.
There may also be other opportunities to reduce the cost of outside services, e.g., by carrying out some equipment rebuilds in-house.
If you are contemplating improving work planning and scheduling, it is important to think the process right through to the end so you have an answer to the basic question, "How will this affect the bottom line?" and a plan to complete the change process.
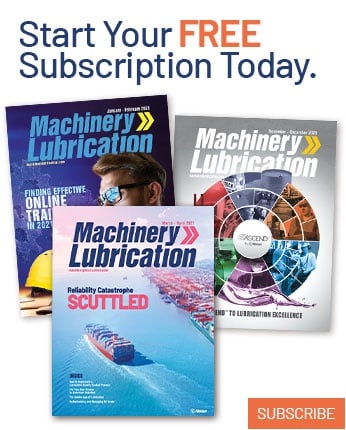