In an industrial setting, reliability is the "product" of maintenance, so it's very important that it be measured. Maintenance is expensive, and you should know what it is buying you.
There are many ways to measure reliability, and the measurements should provide information that is useful for reliability management. The measurement process should also not take too much time or effort.
The best way to make reliability measurements useful is to record losses at the "equipment location" level, which is normally the level at which individual items of manufacturing or processing equipment are identified and numbered.
"Losses" are the units of production that were not manufactured (or were not of saleable quality) but could have been if all had gone as planned.
Losses may have a number of causes, including insufficient incoming inventory, too much outgoing inventory, raw material quality, equipment breakdowns or slowdowns, lack of trained operators, etc.
The best way to record losses is to:
-
Establish the maximum production rate for each major manufacturing unit (usually a manufacturing operation, which has some incoming and outgoing storage for process inventory) for each product or product grade.
-
Establish a target production for each manufacturing unit for each product (e.g., 90 percent of maximum production) for each shift worked.
-
Account for all losses below this target using a simple recording system, as described below.
-
Review all losses for each shift and ensure that they have been recorded in a way that will allow the information gathered to be used to identify opportunities for improvement. There should be a position, such as a reliability or process engineer, with the responsibility for these daily reviews.
-
Regularly analyze loss records and use the information to develop and maintain a program of continuous improvement, always focusing on the highest value opportunities.
Losses should be recorded as soon as they occur, usually by the department operator because that's the one position that is always there and knows about each event.
A simple paper form could be used, but an electronic log is preferred so that the information does not have to be re-entered for analysis. Some maintenance computer systems have the functionality to record losses, but most do not. A suitable log can be designed and built for your operation.
The information to be recorded by the operator for each event as soon as it occurs should include:
-
The name of the manufacturing unit
-
The date and time the event started
-
The date and time the event ended
-
The number of production units lost
-
The cause of the loss (if known)
-
The equipment number and description if the loss is caused by an equipment problem
-
Any other information that may be of use in future analysis
The daily assessments by the operating specialist should review the information, confirm the cause and assign responsibility, e.g., operations, mechanical, electrical, etc.
Please note that the department to which the loss is assigned should be the department that is in the best position to ensure it does not happen again. It is not the department that is "to blame."
The graph below shows one result of using such a loss recording system. After analyzing two years of production loss records, it was determined that 87 of 12,000 equipment items contributed 80 percent of all unscheduled downtime.
A preventive maintenance program focusing on these 87 items and similar equipment resulted in the loss reduction shown in the graph.
There are other ways of measuring reliability, such as automated overall equipment effectiveness (OEE) instrumentation, that may well be justified in certain circumstances.
Reliability is the most important and useful key performance indicator (KPI) for maintenance and should be reported regularly, with the ability to filter for each operating department and maintenance discipline. The results form the basis for a program of continuous improvement.
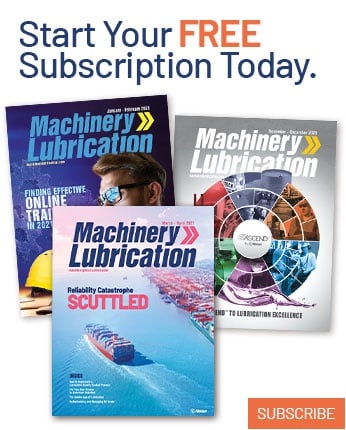