In many organizations, the focus on maintenance tasks is too general in nature, trusting the craftsperson to do the right thing. While we should trust our people, most of whom are highly competent and skilled, we also should set the expectation for the work to be accomplished in a precise manner. Otherwise, how do we improve if there is no one method of "standard work"?
Recognize that if we leave it up to individuals, we will have as many methods as we have individuals who do the work. As a team using the continuous feedback process, we want to determine the most effective and precise method to perform any given task.
Why, might you ask? Using precision maintenance, you reduce or avoid early life failure due to resonance, unbalance, soft foot, contamination (i.e., moisture, chemical, particle), poor lubrication, excessive heat or friction, looseness, imbalance or misalignment. Remember that roughly 89 percent of failures occur in early life or during the constant failure period.
Rather than just "Check belt" as a task, use "Check belt for tightness (using a belt tension device), fraying, cracking or damage." More specifically, what should the tension be? With other components, what should the torque be on the fasteners? What should the gap, clearances or tolerances be? What is the maximum vibration allowable on the installation of new equipment? Where is the precision alignment? Do you use sheave gauges to determine wear? How much wear is acceptable prior to replacement?
Do you perform "standard work" in your maintenance tasks? If not, give it a try. You just might like the results.
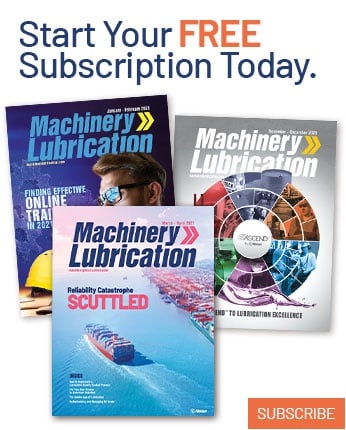