One of the issues with overall equipment effectiveness (OEE) is that it is an output process metric (speed performance x quality x uptime). It’s great as a process metric for measuring machine performance, but it ignores the resources consumed in the process. Given enough money, I can improve any or all of the factors and reach any machine OEE goal on which I am measured.
In past articles, I’ve pointed out the fallacies of equal weighting of the three factors of OEE and explained one plant’s efforts to make the cost impact of quality an impact on OEE by increasing a quality change by seven-fold. A 1-percent decrease became a 7-percent penalty.
I submit that the rework cost was, therefore, rolled into the equation; however, it’s still a performance metric. OK, so what if it is a performance metric? Would this be a metric taught to a finance person, an accountant or the treasurer of your company? What meaning would it have? How does it relate to the resources (dollars) required to get it? If I were to mention miles per gallon, board feet per log, pieces per work hour or other outputs per input, maybe you would see where I am going.
You wouldn’t go to the plant manager and say, “I want another mechanic for the ‘A’ line; it will increase the OEE by 4 percent with a resulting reduction in unit product cost of 8 percent.”
I have developed a new measurement that incorporates costs and OEE. I believe line performance should be tracked by this metric.
Total costs = Cost per unit produce
Units produced x OEE
A new metric has just been added to your dashboard that will allow you to measure the effect of reliability change on the bottom line. I submit that even the finance types and the production types will understand this new use of OEE. If you change the input, you expect an output change.
In the formula, if you increase the denominator or decrease the numerator, the final cost per unit produced goes down. In this case, you saw the need to apply maintenance resources to reduce the need for operational resources of labor and/or materials.
However, at a staff meeting, the industrial engineer makes a critical observation: “The two factors in the denominator are not independent variables. If I increase OEE by 4 percent, I would expect production to go up by 4 percent, thereby the cost per unit would drop by 8 percent.” The idea has merit, and we can begin to manage with OEE by recognizing the impact of each OEE factor.
The industrial engineer follows up with an alternative in which the unit’s denominator becomes the designed throughput and a constant. Costs are driven by changes in OEE.
Total costs = Cost per unit produce
Designed throughput x OEE
The staff meeting continues with enthusiasm from all attendees as the formula now focuses on the causes and costs of production. Yet we now have a metric that can be understood by the line personnel, top management and even the financial types.
It has become a key performance indicator, recognizing that change comes from paying attention to the details. OEE is no longer owned by maintenance and operations; it is now capable of tying purchasing, finance and human relations to the production floor through understanding of costs driven by the OEE factors.
Think about it. How hard is it for you to justify an increase in maintenance resources? I’ll let you ponder its practicality. For one thing, it becomes a metric understood and useful to all direct and indirect plant functions.
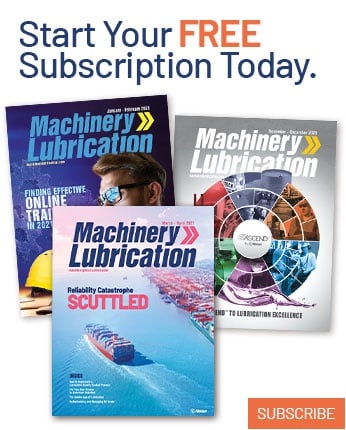