The people who work for the Transportation Security Administration (TSA) in airports know what it is like to be in a fishbowl. They always perform to an impatient, critical, assessing audience, as most of us are forced to watch them work for much longer than we want. Of course, if you’re just standing in line impatiently waiting, then observing and criticizing is really all you have to do (or you can talk loudly on your cellphone).
Most of us standing there usually can identify some individual who might be better suited to another line of work. Some of the frustrated folks standing around me have been pretty obnoxious and verbal about this on occasion. There are, however, many TSA workers who clearly feel that they’re dealing with customers and try to make the process smoother, quicker and even friendlier for them.
This started me thinking about all the various plant maintenance and manufacturing assessments I’ve been involved in over the years, and the success (or not) of the various improvement efforts tied to them.
After reading the book “How We Decide” by Jonah Lehrer, I was surprised to find that all of the supposedly rational judgments I thought I was making over the years were really mostly emotional. The emotional part of the brain is just tremendously more capable and can deal with vastly more information than the puny little rational part. I guess I started to realize maybe how I really was making these assessments.
Basically, the actual assessment really doesn’t take very long – just enough time to walk around the place, observe and talk to some people. What takes time is compiling the evidence to support the assessment and using that for the discussions that help the plant build its improvement plan.
Thinking about it, in judging a plant, the emotional brain is getting a fix on two things — intensity and respect.
Intensity is the overall purposefulness that people display, a sense that they value their time and their function as important, and they need to do the most with it.
The other would be respect in its many forms – respect for the product, respect for the equipment, respect for the facility, respect for each other, respect for their customers, respect for managers and managers having respect for employees (an absence of “us” and “them” statements and behavior on both parts).
One of the places I always make a point of visiting is the plant washroom. This is where the overall level of respect (in its many forms) is pretty much immediately evident.
Going a step further, the intensity really comes from the respect. If you value what you’re doing, then you tend to do it well. If the value is not there, then doing it well is difficult.
The third thing would be the work processes (or lack of them) that are in place. We can work all we want on the actual processes that just do the work, but if the intensity and respect are not there, the very best we can hope for is mediocre. However, if we incorporate feedback mechanisms into these work processes to routinely involve and develop people, then the respect and intensity will come. This is how we truly get on the road to excellence.
About the Author
Currently working as a consultant, John Crossan retired after spending 30-plus years with the Clorox Company. His roles for much of the past 14 years were mainly focused on improving operations by fostering the installation and ongoing implementation of basic manufacturing and maintenance procedural mechanisms across 30 varied plants in the U.S. and Canada. Prior to Clorox, John also held operational and engineering roles with Johnson & Johnson and the Burndy Corporation. He can be reached via e-mail at john@johncrossan.com or online at www.johncrossan.com.
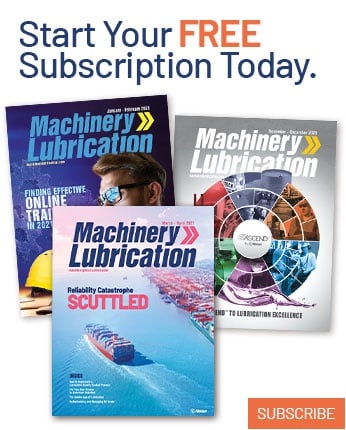