Findings from recent catastrophic events, such as the oil spill in the Gulf of Mexico, have revealed that information relating to asset health was readily available but not properly managed. Analysis of the Gulf of Mexico event indicated that there were conditions in critical assets that could have impaired performance prior to and after the accident.
A routine testing and maintenance program should have detected these conditions. This is an easy statement to make after a catastrophic event occurs. What is much more difficult is to navigate the overwhelming number of specifications and standards available to corporations on management systems and develop an asset management model that provides the transparency to asset health.
The first step is developing a management system standard that adequately addresses six key elements:
- Policy
- Planning
- Implementation and operation
- Performance assessment
- Improvement
- Management review
This (and all other standards and specifications relating to management systems) follows the plan-do-check-act methodology of continuous improvement.
Now think of all the management systems we have relating to our business — quality management systems, asset management systems, performance or production management systems, environmental, health and safety management systems.
We need to integrate these systems to ensure common elements are leveraged to manage the requirements and the data that provide us the transparency we require in risk identification and decision-making.
Figure 1 illustrates the common requirements, such as information and information technology. Proper integration of these standards yields the following benefits:
- Improved business focus
- Holistic approach to managing business risk
- Less conflict between systems
- Reduction in duplication and bureaucracy
- Effective and efficient internal and external audits
Figure 1
The next step is to have a risk-based asset management system in place like that depicted in Figure 2. This management system, like the others, follows the plan-do-check-act methodology. Following this methodology is critically important. When accidents occur, like the one in the Gulf, it’s often because the management systems addressed the “plan,” “do” and “check,” but lacked the “act.”
Figure 2. Risk-based Asset Management System
One of the shortcomings of management systems is a key common element — information management. Once we appropriately classify our assets to determine those critical to our value stream, we then perform the analysis and develop the control strategy to mitigate or eliminate risk.
These control strategies are requirements, and executing these control strategies generates data. Here lies the most important point to this discussion. The investigation report from the Gulf accident stated that a routine testing and maintenance program should have detected these conditions.
This is not a simple statement. The information contained in the data that is generated from these requirements is collected and stored in numerous locations on various IT systems.
Figure 3 illustrates the complexity of management information at a refinery. The boundary of the Purdue Reference Model (shaded in gray) is that information relevant to asset management.
Figure 3. Enterprise-control System Integration
We need to ensure that we have identified how the data generated from our control strategy will be integrated to determine asset health and provide the transparency needed to identify, mitigate and eliminate risk. Figure 4 is an example of an asset management information system model.
Figure 4. Asset Management Information Model
From this model, it is clear that until we map the criteria to the condition, integrate the information and provide it in a portal or dashboard, we will not have an accurate indication of asset health and therefore will remain at risk.
As technology advances, there are new and innovative ways to perform these functions. However, until we address these significant gaps, we will continue to have the information we need but not use it to create value.
About the Author
Mike Poland is the director of Life Cycle Engineering’s Asset Management Services group. With more than 25 years of engineering and maintenance experience, Mike specializes in reliability processes and systems engineering with an emphasis on defect detection and elimination through root-cause analysis and risk-based inspections. His approach to risk-based asset management and the elimination of limiting factors for clients provides greatly enhanced asset utilization at a much lower total cost of ownership. Mike can be reached at mpoland@LCE.com.
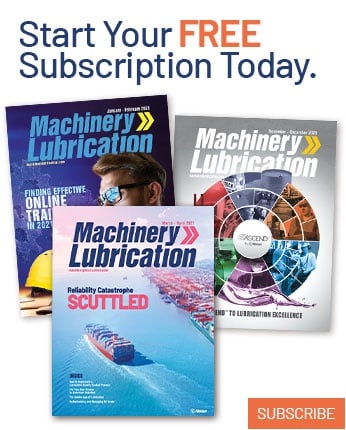