From previous surveys and depending on the audience responding, either everyone (upward of 90 percent) or a minority (less than 40 percent) has an effective preventive maintenance (PM) program. With the range so broad, let’s dig a little deeper to determine what it takes to have an effective PM program. For the purposes of this article, I also am including condition-based monitoring activities such as inspection.
What is the strategic and business case for your PM activities? Why are you doing the PM activities, and how did you come to choose those activities? Did you just pull them from the equipment manual? What value is the program providing you? No, I’m not talking about the “perceived” value. What is the measured value that you can prove to your partners? If they stop operating the equipment to give you a window to do PM activities (condition-based inspections and so forth, not necessarily component replacement activities), what do they get in return?
Yes, I understand those partners get “improved” reliability, but why did the equipment fail two days later after the PM was completed? What was improved about that? Oh, infant mortality again, right? OK, I’ll get to the point.
An effective PM program requires a solid foundation; a bedrock that begins with an asset life plan. That is a strategic maintenance plan that begins with the business case and equipment operational life expectancy at the top level. It must include the operations scheduled use. At the bottom level, you must understand the equipment function, the consequences of failure and address the failure modes. You have to blend all of this together to find potential failures and proactively restore the equipment prior to functional failure. It is a comprehensive strategy, not just simply copying the equipment manufacturer’s recommendation from the manual.
Needless to say, it requires top-level management support. In addition, you will not be effective if you don’t have a partnership, especially with your operations partners. You need to measure the value the effort brings and effectively communicate those to your partners and your own group. Where is your continuous improvement loop to optimize the findings from the activities? Are you capturing good information from your technicians back into the work order system? What about your root cause analysis effort that feeds the optimization even more? An effective planning and scheduling function is a requirement as well. The PM activity requires procedures written to a specification with the focus of standardized work and precision maintenance. It includes capturing that “tribal knowledge” and ensuring it’s the right knowledge. From the front-line supervision, there has to be an auditing component from a craft development perspective. Do we have the skills required to perform the work?
If not, how are you going to develop them? How can you determine success? Where are your measures that show the value? You need an inclusive set – not around work measurement that creates animosity, but around the processes. Remember, the product is always a result of the process. Lastly for this article, what is your communication plan?
What other items would you add to those above as part of a comprehensive preventive maintenance strategy that includes condition monitoring activities?
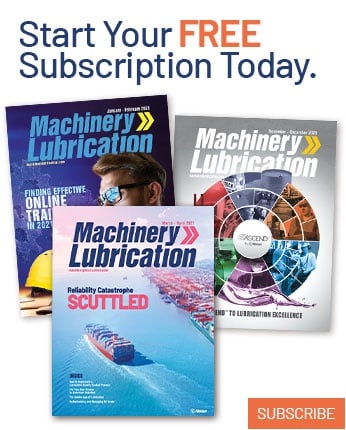