"How do I quantify my PdM finds? Where do I go to establish my credibility?"
Grow a thick skin, fast. You have to develop some way of bringing some sense to the finds you have made in your predictive maintenance program.
Now that trust has been established and your routes are being executed, you wonder if the work you are doing is worthwhile. Are there any finds to report on to show you are doing a good job? How do you quantify the finds that have been reported, and put a dollar sign to the finds, to prove the system is working to the benefit of the company or department? How do you show that you are saving money, and that the trust you have been afforded is well founded?
Nobody teaches us how to do this. It is one of the most difficult processes you have to establish in your PdM program. But, it's essential to justify your program's existence. My way of quantifying a good find is simply to use a delay avoidance process. I take the cost per hour of rolling time and multiply that times the number of hours saved by not having to shut down. There are a lot of fancy systems out there where this figure multiplied by that then divided by something else gives you a number. Why should it be so complicated?
My first find saved four hours. Instead of being down for seven hours, we were down three hours. Infrared thermography showed a differential between the four pistons in the project block. I selected the bottom right cylinder, and it was correct. Hooray! Repairs were made to the cylinder, it was pressurized and there was no leak. We came ahead and rolled for the duration on the repaired system. The cost avoidance was 4 x $40,000, or an avoidance of $160,000. Through this find, my infrared camera was paid for, my wages were taken care of for the rest of the year, the system worked, and I finally realized that what I was doing was the right thing. This showed that the PdM program could be very successful and a value-added exercise.
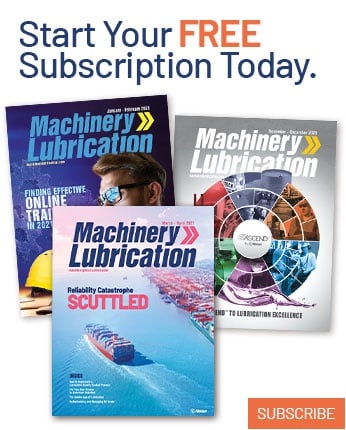