Thermal scanning, automatic balancers and levelers, predictive equipment, fluid scans, ultrasonic testing, PM programs, reports and logs, more reports and logs, and yet even more reports and logs. These are all great ways to track, detect or predict possible real, and future failures. I know many companies that have these items, and a host of others have them at their disposal, but, yet, these companies do not run any more efficiently than the companies that may not have access to these resources. Why is that?
I believe that the key to success in plant reliability is not in the tools we use, nor in the methods with which we choose to measure performance. Success in plant reliability is in the hands of the people who actually do the work. Managers can tell their employees what to do, when to do it, and how to do it, but if the people do not take ownership in what they are doing, and if there is not a culture of "This is MY plant, I need to do whatever it takes to keep this plant running today, tomorrow and into the future, and in a cost-effective manner", then the company is just as doomed as a neglected bearing. Sure, it will run for a while unattended and not greased; but in time, we all know the outcome. One day, the bearing will "unexpectedly" cease, lock up, destroy the shaft, the housing, cause unwanted downtime, and will result in a loss of revenue generation. In some cases, it will cause a work stoppage that results in lost time for the employee(s) until necessary repairs can be made. But, really, come on, was this really "unexpected"? Quite the contrary. Why wouldn't you expect it?
Is it tough to get your crew in this mode of self-ownership? You better believe it! Look up and down the management aisles in the bookstores. They are packed with: "how to get the most out of your people" books, "leadership" books, "getting things done" books, "team-building" books, and the list goes on and on. In comparison, assembling, fabricating, laboring, planning and scheduling are easy. But getting the right people to do the right thing at the right time is the most difficult process of all. Not to say that it is always difficult. I believe that once you embark on the journey of getting the right people to do the right things at the right time, it becomes like the flywheel concept in the book "Good to Great". The momentum these "right people" create when doing the right things at the right times will make this process easier and easier every time, until finally your business, process or plant is running on auto-pilot, headed to plant reliability.
If you were the owner of a professional sports team and you brought in a high-priced manager/coach to take your team to the championship game, you wouldn't find a great manager/coach, bring that person in, pay that person a lot of money, and then tell that person how to do the job. You brought that person in because you believed he or she already knows HOW to do the job (win) and can take your team to the championship game. You want that person to get the right people in, get the right people in the right spots doing the right things at the right times, develop and unveil the plan, determine what tools will be needed and obtain them, implement the plan, review progress, and take necessary action where determined (the Plan-Do-Check-Act cycle). But it all starts with people.
I call this approach P-FIRST: People First Indicates a Reliable, Successful Team.
The key to reliability is in the hands of people - the right people doing the right job with the right tools at the right time. It is our job as managers and leaders to manage these four key aspects if we are to succeed at being a reliable plant.
What are your thoughts on this subject? Please post your questions, comments, and own stories of maintenance and reliability success factors. Let's get the conversation rolling.
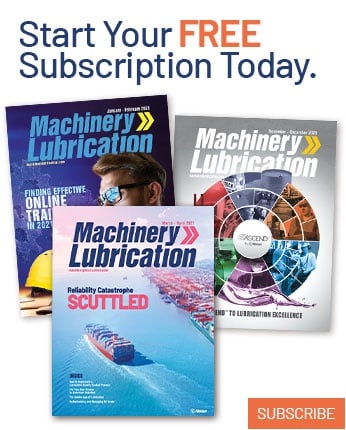