As many of us strive to improve the reliability of our plants, several comments bemoan how challenging that is to do in an era of continuous deep cost cutting. They say that in their operation, maintenance is seen as a cost, and is one of the first things to arbitrarily cut.
Some think their operations have cut too far! What they seek is a way to justify a strong maintenance capability.
I submit that one approach is to speak of maintenance as an "investment in capacity." Use the language that plant managers, controllers and senior management understands: capital investment and return on investment (ROI).
“When you substitute your own estimates, the resulting comparison will be different in the details, but it will almost always favor an approach that improves reliability.”
Before I continue, this article is NOT intended for factories with clearly wasteful practices. We do need to cut costs where doing so will not hamper our operations. Future blogs will share some approaches for reducing costs.
This blog is for those that have cut too far or have never "invested" in the first place.
Begin by gathering some basic data. What is your plant's or your company's total capacity? What is your "efficiency"? This may be an established metric like overall equipment efficiency (OEE), or you can approximate it by taking the actual production in a day divided by the theoretical production if everything ran at maximum speed for all of your operating hours.
Next, look at the capital costs of adding new capacity. If you have four production lines, what would it cost to add a fifth? If your company has six factories, what would it cost to add a seventh? What is the operating cost in labor and utilities to run that new line or new plant?
Now the fun part begins, where you get to do some math! If you are running at 40 percent efficiency and you believe you can improve that by 10 points to 50 percent with "more maintenance," that will result in a whopping 25 percent gain in capacity!
[(50% - 40%)/40% x 100% = 25%]
The numbers work out similarly if you are starting at 60 percent, but now a 10-point improvement increases capacity by 18 percent.
Would your plant invest $100,000 or some other figure annually in "more maintenance" to get the same capacity increase as a new line that will cost half a million or more to install and $200,000 annually to staff and run?
When you substitute your own estimates, the resulting comparison will be different in the details, but it will almost always favor an approach that improves reliability. This is especially true for a growing organization that is investing in machinery to prevent being capacity constrained.
What If you are not growing and capacity constrained? The same reliability improvements illustrated above will reduce your operating labor, utilities and machinery wear and tear by 18 to 25 percent. Put that in your ROI calculator.
Alas, I have been long-winded again. Let me close with just a few salient points:
Yes, many operations with unstructured maintenance programs do run as poorly as 40 to 60 percent (see my blog on what our plants have failed to learn in 25 years).
If you run above 80 percent, the math still works but the gains are smaller, just like adding more insulation to an already well-insulated attic.
Yes, it is usually easy to improve a poorly running operation by 10 points. I inherited one facility running at 35 percent uptime, and had improved it to 65 percent in one year using many of the preventive maintenance (PM) and predictive maintenance (PdM) approaches described throughout Reliable Plant magazine. This nearly doubled our capacity, even while we had room for much more improvement. You must have some ideas of your own about how to improve your place, and I will add some of my own in future blogs.
Finally, yes, you must make some estimates, develop plans, sell your proposition and in the end be accountable for the results if an "investment" is to be made. This is just the same as for a project manager who is building a new plant or line.
Please add your comment below on your own level of efficiency or throughput. If you had more resources, what would you add, what would it cost you, and how much do you think you could improve your throughput? Finally, how does this compare with the capital cost of adding a similar amount of capacity?
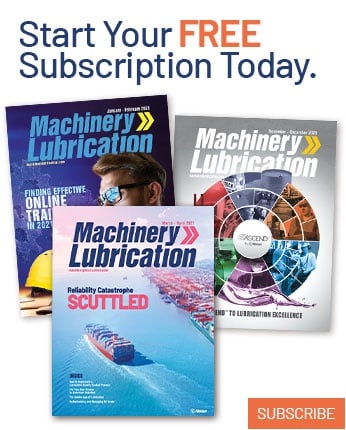