As a maintenance technician, do you believe having responsibility for specific equipment is the best way to perform your job? By responsibility, I mean you are the only one that conducts preventive maintenance tasks and major repair work on that specific equipment. Do you believe it’s the right answer for the organization? As a maintenance manager, is this approach to equipment ownership the right answer for you or your stakeholder partners like operations? In all of my time in engineering and maintenance, this facet of maintenance has been a struggle for many maintenance organizations.
When I was part of a team that built a pet food facility in Columbia, S.C., a few years back, the maintenance organization was modeled after similar organizations in the company. There were two maintenance technicians that covered each of three shifts and rotated across those shifts. Ideally, one was mechanical and the other electrical. Then, there were five or six day-shift maintenance technicians that had system ownership. There was one technician for the receiving, grinding, extrusion, drying, packaging and controls areas. Each of these maintenance technicians decided the day’s priorities, performed the preventive maintenance, handled the longer-term strategic improvements and capital work. Obviously, they were the “go to” guys or system “experts” for any issues or work in their areas. They truly owned the equipment and took pride in the work they did. From a technician perspective, it was great as they called the shots and the business benefited. If they needed help doing something, they might ask another system technician to lend a hand or they may write a work order for some contractor resources to help.
But this model is not always as rosy as it appears from a maintenance management perspective. Consider Fred who has been the extrusion system technician for six years. This area is not for the faint hearted as it has 300-horsepower motors and large equipment with complex support systems. Fred was working on his daughter’s car at home and injured his back. He’s going to be out for three months, at a minimum. Since Fred is the only one who works on it, no one else has any expertise. Now what do you do? Let’s look at some other items. While a maintenance planner existed, the system technicians decided the priorities for their work. That was by individual system areas, not the overall factory needs. The thought was, “Just because it was a priority for one area didn’t mean it was a priority in my area.” So there was no real overarching priority matrix that was enforced. Trying to get people to work on equipment outside their areas was like pulling teeth at times. Some guys didn’t agree with the approaches and methodologies that other guys used in their areas; so consistency was a factor. So, rather than one cohesive factory, you ended up with six silos each marching to their own drummer.
I have seen some organizations encourage ownership and try to overcome the expertise issue by using an approach called “secondary skills”. If the technician learned a skill outside his normal work area, then the business would compensate the individual with additional pay per hour. It was a management responsibility to make sure the people used those “secondary skills”. Often, that never happens on a frequent basis. So, time goes by, possibly years, and the technician “forgets” how to do the work. The increased pay did not stop, however, and one day the call comes to send the technician over to apply those “secondary skills”. The maintenance technician isn’t too keen on the idea since its Fred’s area and they haven’t touched that equipment in three years. Up comes the safety flag and 10 reasons why they aren’t the right person for the job. Maybe they are right; you decide.
Conversely, if management makes the technicians constantly rotate across the areas, you never build any expertise on any equipment – and you don’t build any ownership, either. Many organizations face this struggle today. If the work gets complicated, they have to call the factory representative to come do the work, or it’s outsourced. If the equipment has been modified, the factory rep smiles and says, “Sorry, but that’s not our equipment.” It’s not just skills related to production equipment, but consider someone with machinist skills inside maintenance organization. When the equipment is down and you need it, you generally need it now. Many shops don’t have mills or lathes anymore, not to mention the skilled people to run them.
Some of this is driven by how you align the maintenance organization as well (i.e. centralized or de-centralized). What’s a maintenance manager to do? How do you strike a balance between equipment ownership and building the skills through cross training, and having the ability to get the work done all the time? Is it based on the culture of the organization?
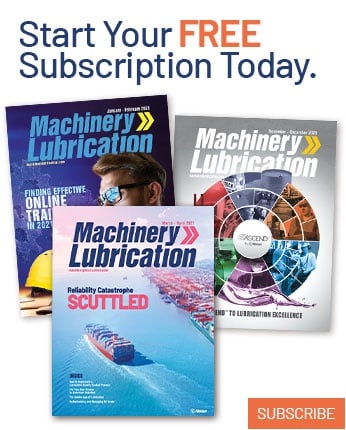