Supporting data reveals that as much as 22 percent of reliability problems faced in manufacturing is caused by uncontrolled changes (1). These include process and equipment configuration changes such as alterations, modifications and new installations. Evidence of this correlation was apparent from as early as the 1960s, which led to what was then referred to as Configuration Management. The initial focus of this management methodology was on changes to asset configuration and how components interact together as a system. Over the past few decades, more emphasis has been placed on not only controlling equipment changes, but more holistically understanding change control needs, which among other things included changes to procedures, process steps and administration. This is what we have come to know today as management of change (MOC).
No systematic process would be complete without the 3 Ps (Principle, Policy and Practice) of such a process engrained in the culture of the business. An MOC process is no exception, and to fully integrate it into a business can be a large undertaking, but not prohibitively so. It, therefore, stands to reason that a business manager contemplating the value of this process should be provided with a few good supporting arguments. There are at least four good reasons that I can cite for the implementation of a systematic MOC process: 1) It prevents accidents; 2) it increases/sustains asset reliability; 3) it ensures traceability of changes; and 4) it ensures the proper evaluation of alternatives.
An MOC process prevents accidents
With growing global concern for personal safety and the environment, increasing regulation has underscored the need for manufacturers to resolve and prevent the root causes of accidents. As previously stated, a large subset of the latent issues leading to such incidents has to do with various forms of uncontrolled changes. Organizations without systematic MOC processes often end up with sub-optimized risk management systems which don’t proactively recognize perils and hinders follow-up on previously identified hazards. Quite simply, unless changes are properly evaluated, one will not be able to fully understand how best to treat their associated risks.
An MOC process increases asset reliability
I should further expand this reason category to include product quality and reliability, which are often both impacted by the reliability of the manufacturing assets. Without MOC, uncontrolled changes often lead to:
- The improper operation of assets, which is one of the leading causes of failures.
- Inadequate/outdated operating and maintenance procedures, which shorten the life cycle of asset components as well as increase exposure to unknown business risks.
- A lack of skills training and poor employee involvement which suppress the sense of ownership required to continuously improve the reliability of the assets and manufacturing process.
An MOC process ensures traceability of changes
A growing number of standards applicable to every major industry today require that changes are transparent and traceable. OSHA 1910.119 (2), for example, clearly sanctions the implementation of MOC as a means to evaluate and trace change. “OSHA believes that contemplated changes to a process must be thoroughly evaluated to fully assess their impact on employee safety and health and to determine needed changes to operating procedures.”
As each proposal is evaluated, modifications made and changes commissioned, a careful record stands up to all scrutiny and possible reversion to the former status quo. Changes tend to be very cyclical in nature, which lends some credibility to the adage “the more things change, the more they stay the same.” Companies without proper, systematic MOC tend to fall victim to wasting valuable time and resources retreading the same ground in all the major areas of change (mis)management: identification, evaluation, approval, execution and audit.
An MOC process ensures evaluation of alternatives
In my experience, it has never been difficult to find someone who has witnessed or found themselves in the following scenario. It is a Monday morning and you’ve discovered that a prime mover was modified in response to an urgent request for more throughput over the weekend in one area of the facility. No negative impact is immediately apparent, so this new setting is adopted as the norm. A short time later, however, inexplicable failures in critical equipment downstream in another area are observed. Quite often, with the best of intentions, changes are made which negatively affect the business. A systematic MOC process will be triggered whenever any such changes are proposed so that the proper evaluations of solutions take place. If nothing else, it will sometimes slow down or stop the execution of unnecessary changes and ensure careful planning of necessary work. The most important question you can ask is “should I be making a change at all?”
In the process and manufacturing environments, the MOC process will be used for controlling all types of changes (form, fit or function) to physical assets and processes, SOPs, drawings, BOMs, etc., so that it can be effectively managed. In general, all process and plant changes except replacements in kind should be associated with the MOC process, although some latitude can be exercised regarding the specific methodologies and the level of reviews required.
By all indications of what the future in manufacturing governance is shaping up to be, there will be an increasing need for proper management of changes. It is, hence, absolutely critical that systematic MOC programs are adopted by organizations seeking to obtain world-class manufacturing excellence.
References
- Moore, R. Making Common Sense Common Practice (third edition), Elsevier Butterworth-Heinemann; (May 21, 2004).
- OSHA 3132, Process Safety Management, U.S. Department of Labor, Occupational Safety and Health Administration.
- OSHA 1910.119, Process Safety Management of Highly Hazardous Chemicals, U.S. Department of Labor, Occupational Safety and Health Administration.
This article appeared in the July edition of Life Cycle Engineering’s newsletter, RxToday.
About the author:
Carl March has a wealth of experience in the areas of maintenance, reliability engineering, systems modeling and design. Carl holds an undergraduate degree in mechanical engineering and a graduate degree in automotive systems engineering. As a reliability subject matter expert at Life Cycle Engineering, his passion and focus is in the transfer of knowledge in Reliability-Centered Maintenance, Total Productive Maintenance, root cause analysis and Reliability Excellence to clients worldwide seeking to achieve manufacturing distinction. Carl has attained a significant level of professional recognition as a licensed Professional Engineer (PE), a Certified Reliability Engineer (CRE) by the American Society for Quality, and as a Certified Maintenance and Reliability Professional (CMRP) by the Society of Maintenance and Reliability Professionals. You can reach Carl at cmarch@LCE.com.
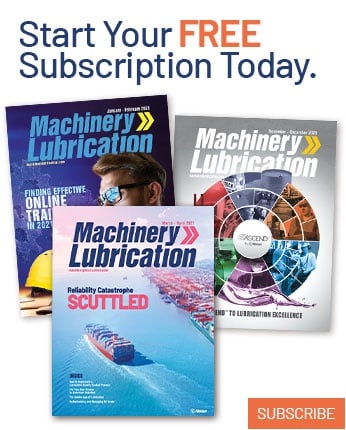