No matter where an asset sits in the plant, the need to understand its health has become increasingly vital. While most facilities continuously monitor their critical machinery, their less-critical assets – often called “essential assets” – cannot typically justify the expense of a traditional continuous monitoring system due to the installation costs of running wires and installing sensors. As such, these assets tend to be addressed with portable data collection programs where operators make rounds at monthly or quarterly intervals, manually collecting data. However, these data collection intervals are rarely satisfactory for essential assets, and problems can progress from “OK” to “serious” from one data collection interval to the next. Or, in some cases, manual data collection is simply not practical or possible due to the nature of the asset – jeopardizing the safety of the employee tasked with collecting data.
To address such challenges and elevate plant reliability, industrial facilities are increasingly turning to wireless. NV Energy highlights this trend with its recent installation of GE Energy’s Bently Nevada Essential Insight.mesh wireless condition monitoring system. The system was installed at the company’s Fort Churchill Operating Station in Yerington, Nev., with the goal of reducing operating expenses and increasing reliability.
Before the installation of Essential Insight.mesh, these assets were only infrequently monitored by a walk-around program. The wireless condition monitoring systems help to improve overall plant reliability and efficiency by extending condition monitoring to a broader array of essential assets that were previously underserved and classified as mid- to low-criticality.
“We were excited to be the first plant in NV Energy to utilize this new technology,” says Greg Bushman, plant manager at Fort Churchill. “We have always used Bently Nevada condition monitoring for our critical assets, so it seemed like a natural fit to extend this to our essential assets, as well.”
Over the course of two days, the entire wireless system was deployed and configured on a wide range of rotating machines, including boiler feed pumps, condensate pumps, AC lube oil pumps, service water pumps, circulation water pumps and an FD fan. The system consisted of 21 vibration sensors, seven wSIM nodes, three Repeaters and System 1 software.
The system began returning useful information almost immediately as anomalies were detected on cooling water pumps and confirmed the need to plan and schedule repairs.
Because the data from these assets is transmitted wirelessly to the plant’s Electronics Room, where a System 1 display computer is located, it is now within easy reach of plant operators and is integrated with all of the data from other monitored assets, such as the plant’s critical turbine-generator sets.
This provides operators with plant-wide analysis and insight capabilities on the mechanical condition of their assets, allowing data-driven decisions and thus reducing costs of plant operations and maintenance. Armed with these benefits, and the considerably lower costs of installation and deployment that wireless technology affords, customers can more confidently and easily justify expansion of online condition monitoring to a broader spectrum of assets in their plants, such as remote deep-well pumps, cooling towers and more.
By helping plants extend affordable, online monitoring to more asset types, they can operate smarter – increasing efficiency, reliability, and uptime, which can translate to a reduction in operating expenses.
For more information on GE Energy products and services, visit:
http://www.gepower.com/prod_serv/products/oc/en/bently_nevada/essential_insight.htm
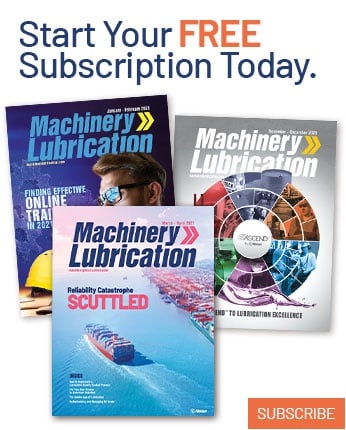