Wind turbines appear so simple – tall white sentinels cranking gracefully on the horizon. But up close, a wind turbine is an industrial workhorse. Inside the nacelle, hundreds of feet off the ground, hot metal gears grind and strain as shifting winds pull and twist the long flexible blades.
At the National Renewable Energy Laboratory (NREL), senior engineers are expanding a research partnership with operators, utilities and turbine manufacturers to determine why some key wind turbine components tend to wear too soon – sometimes within a few years of installation. That’s a problem because wind turbines are expected to operate for 20 years. Early equipment fatigue, especially in turbine gearboxes, threatens to reduce performance and drive up wind power costs just as the industry is poised to capture a greater share of U.S. generating capacity.
Improving their reliability is key to generating a consistently competitive power source – and a healthy return on investment. Both are needed if wind power is to meet 20 percent of the nation’s electricity needs by 2030, a scenario a U.S. Department of Energy report issued last year says is possible.
“The end-users and the owner-operators say we’re only getting five years or, in some cases, three years out of these gearboxes,” said NREL principal engineer Sandy Butterfield, who is leading the cooperative study.
Newer turbine designs may work, but without the NREL study it will take a number of operating years in the field to prove that the reliability problems have been resolved.
“This project is designed to search for any residual gaps in the design process and confirm a robust design practice used in current production turbines,” Butterfield said. “We can’t wait five more years to discover any residual gaps.”
Rows of turbines glow in the sunrise at Ponnequin Wind Facility on the Colorado-Wyoming border. NREL will test improved gearbox designs at the wind farm. (Courtesy of Jenny Hager Photography)
Collective Examination
In 2007, Butterfield, senior engineer Walt Musial and consultant Brian McNiff began assembling the Gearbox Reliability Collaborative among turbine manufacturers, utilities and suppliers. The collaborative tests extensively instrumented gearboxes to identify weakness in current design approaches and pointed out ways to improve initial designs and retrofit packages. The project identifies equipment failures that are common throughout the industry and targets deficiencies in the design process that are contributing to these problems.
NREL hopes to limit intellectual property concerns by running tests on representative wind turbine configurations and parts, but not replicating any specific manufacturer’s wind turbine model.
At the same time, the participants are expected to openly examine turbine problems and question every assumption of the design process.
Focusing on design is especially important, Butterfield said, because the expanding wind industry is trying to rapidly meet market demand for new and larger-capacity turbines. Designers and manufacturers are all following very stringent design quality, in some cases matching aircraft tolerances. Yet the problems persist. This implies the design standards are missing some critical loads or conditions that are unique to wind turbines. Without identifying the fundamental issues behind previous failures, he said, the same flaws could find their ways into new generations of turbines.
NREL senior engineer Shuangwen Sheng inspects the monitoring system for the long-term gearbox reliability study at the National Wind Technology Center. (Credit: Joseph B. Verrengia)
Nitty-Gritty of Gearboxes
The tests at the National Wind Technology Center focus on several aspects of gearbox performance.
- Automated spray lubrication. Wind turbines crank at low RPMs under high torque, especially in the first stage of gearing where heat and pressure are high. New designs have lubrication channeled directly to the bearing races.
- Oil cleanliness. New turbines have more aggressive filtration systems.
- Automated gearbox monitoring instruments. These systems are supposed to detect damaging operating conditions before a failure occurs.
- Micro-pitting. This phenomenon occurs as metal fatigue creates microscopic weak spots in gears that degrade the equipment over time.
- Load distributions on the gear tooth contacts and the bearing roller elements.
NREL principal engineer Sandy Butterfield is leading a cooperative study with wind turbine manufacturers and users to improve the performance of the turbines’ gearboxes and extend the systems’ operating lives. (Credit: Joseph B. Verrengia)
Initially, the gearboxes under review are being tested on the NWTC dynamometer, where Butterfield and others will simulate a variety of loads and measure the results.
Later, they will put one gearbox into test turbines at the Xcel Energy Ponnequin wind farm and monitor them under real load conditions. A second testing phase is likely to follow.
The gearbox of a large commercial wind turbine is instrumented for testing at the National Wind Technology Center. NREL is conducting long-term tests to improve wind turbine reliability and extend the lifespan of turbine components. (Credit: Joseph B. Verrengia)
Butterfield also intends to build a significant failure database to baseline current failure rates and verify reliability improvements in the future.
“I know we’ll discover a tremendous amount in the first year,” he said. “We hope we can quickly transfer this experience to the industry.”
Learn more about NREL’s wind energy research.
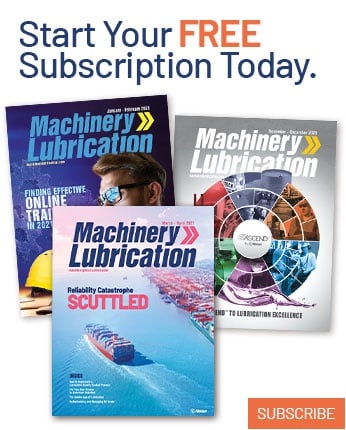