Azima DLI, a leader and premier provider of predictive machine condition monitoring and analysis services, on February 8 announced a series of simplified, pre-packaged programs to ensure comprehensive equipment reliability and uptime results. Based on its extensive industry experience, track record of customer success and established WATCHMAN Reliability Services, Azima DLI is able to strip away the complexity of traditional á la carte maintenance programs and introduce comprehensive, bundled solutions that are tailored to address specific requirements for lean and reliable plant operations.
Due to factors including an exodus of talent, streamlined operations and restricted budgets, Azima DLI has found that many plants are challenged to retain the expert analysis resources necessary to keep their condition monitoring programs running smoothly, or simply don’t know how to initiate a fresh start for a previously well-run program. WATCHMAN Reliability Service Plans were developed to help plants quickly address those challenges. There are three all-inclusive WATCHMAN Reliability Service Plans to choose from that feature an evaluation of the plant environment and risk profile along with a clearly-defined set of solutions and deliverables to meet specific uptime, compliance and cost-avoidance objectives.
Each solution includes primary technologies such as vibration analysis, lube oil analysis and infrared thermography as well as transparency of portal delivery, analysis support, and a range of optional services to ensure a complete condition monitoring solution. In contrast to competitors’ offerings that require heavy investments in hardware and software, Azima DLI’s flexible, scalable offerings don’t require up-front costs and are offered on a subscription basis:
WATCHMAN Professional – Built for plants or enterprises with 250 or more machine assets where unplanned outages cannot be tolerated. WATCHMAN Professional provides the procedures, processes, disciplines and qualified resources to achieve the highest standard in condition-based maintenance.
WATCHMAN Insight – Provides excellent coverage for moderate-sized plants of 75 to 250 machine assets, where unplanned outages are categorized as inconvenient and costly. WATCHMAN Insight provides a solid foundation for a quality condition-based maintenance program.
WATCHMAN Select – Applied to smaller plants with 15-150 machine assets, the program is intended to meet compliance obligations and maintenance planning budgets. WATCHMAN Select provides the essential elements of a growing condition-based maintenance program.
“In today’s market, á la carte choices vary widely from vendor to vendor. This causes uncertainty about how to communicate the value of condition monitoring programs to the C-suite, which has hampered progress and results for many of our competitors,” said Randy Johnson, vice president of sales and marketing, Azima DLI. “Azima DLI has taken important steps to develop easy-to-understand, easy-to-implement service packages that deliver immediate value by increasing plant availability and dramatically driving down unplanned downtime. By packaging our predictive services with a very low cost of entry, and delivering actionable results through our WATCHMAN Reliability Portal to those who need to make critical operational decisions, Azima DLI’s services are recognized by management as critical to plant profitability.”
Based on experience, Azima DLI knows that subscription-based predictive services are delivered best through plant personnel participating in vibration data and oil sample collection. Azima DLI provides the leading data acquisition tools necessary for a successful program, including the DCA-60 vibration data collector, to ensure maintenance professionals have the information they need to support equipment reliability and uptime goals. Additionally, the WATCHMAN Reliability Portal 2.0 provides secure Web-based access and automated alerts for the condition of all monitored equipment including history trends, statistics and reports; results can then be pushed to, or accessed remotely by, key stake holders.
“Azima DLI brings together the best analytics experts with proven technology to track, share and report on critical machinery health to drive better maintenance decisions. As a result, Azima DLI is highly qualified to deliver these new bundled solutions to ensure our customers’ success,” said Jonathan Hakim, president, Azima DLI. “Compared to small regional solutions providers, Azima DLI has an unparalleled bench of experts and broad industry experience associated with specialties such as vibration monitoring, thermography and lube oil analysis. And, unlike other global vendors in the market, Azima DLI is laser focused on machine condition monitoring so it can more effectively tailor programs to specifically meet industrial plants’ operational requirements.”
About Azima DLI
Azima DLI is a leader and premier provider of predictive machine condition monitoring and analysis services that align with customers’ high standards for reliability, availability and uptime. Azima DLI’s WATCHMAN Reliability Services utilize flexible deployment models, proven diagnostic software and unmatched analytical expertise to deliver sustainable, scalable and cost-effective condition-based maintenance programs. The company’s bundled solutions enable customers to choose comprehensive, proven programs that ensure asset availability and maximize productivity. Azima DLI is headquartered in Woburn, Mass., with offices across the U.S. and international representation in Asia-Pacific, Central America, Europe and South America.
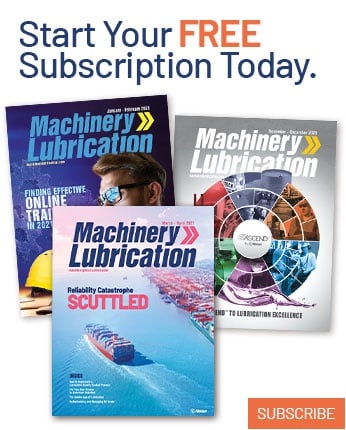