Continuous monitoring is the application of dedicated devices for the purpose of collecting predictive maintenance-style data to aid in a condition monitoring program. With each passing year, this technology gets cheaper, and the desire for more complex and more robust monitoring gets larger. Unfortunately, the technology scales have not fully tilted toward the benefit of the end-user just yet. But, they are leaning more and more that way.
Is continuous monitoring right for every application? Should I envision a day where every single vibration measurement, ultrasonic measurement, temperature measurement and oil sample is continuously monitored and the results displayed in real time on the plant intranet? Not really. How much is enough (or too much)? The answer lies within the analysis of the failure mode(s) you are trying to detect with the continuous monitoring system. The real test for whether or not a continuous monitoring solution is right for a given application is as follows:
1) Is the P-F interval of the failure mode so short that it is otherwise logistically impossible to have a human analyst perform a periodic route to detect the presence of an impending failure?
2) Is the cost of unplanned downtime for this machine so high that the business proposition for installing permanent monitoring systems is a "no-brainer"?
3) Is the frequency of failure such that a continuous monitoring system is required to capture all of the machine parameters surrounding the defect to completely identify the nature of the cause of the problem?
If your answer to any of these questions is "yes", then continuous monitoring may be the best solution for these types of failure modes.
There are numerous technologies that have extensive continuous monitoring options. What follows are some of the big hitters in the PdM world along with some benefits and limitations.
Vibration analysis is one of the largest and most popular continuous monitoring technologies. Vibration sensors such as accelerometers are permanently mounted in the bearing housings of the most critical components and then hard-wired back to a central computer that acts as a data collection, storage and analysis system.
There is a large misconception in the marketplace that these systems by virtue of their cost and complexity also perform the analysis for you. This is not the case. Granted, there have been major advances in narrow band alarming and advanced filtration systems that make the alarms coming from these systems much more meaningful, but an analyst is still required to properly interpret the data and make the assessment of asset health.
Another issue to consider is the fact that although these systems boast of 12, 24 and 36 channels, some measure of capacity is typically forfeited for an increased number of channels. Some systems are limited in the amount of bandwidth that each channel can use. In simple terms, this can limit the quality of data coming into the system. This is even more so in systems that use wireless sensors. While this is convenient and cheap from a wiring standpoint (none), it can severely hamper the amount of data that can be transferred. And, depending on the failure mode being monitored, that could take wireless sensors right out of the picture.
In certain situations, continuous monitoring of vibration data is the right solution. Educate yourself about the advantages and limitations of the system you may be considering. Remember, every system has strengths and weaknesses.
Vibration analysis isn't the only thing that can be monitored continuously. Under certain circumstances, temperatures can be continuously monitored using infrared thermography. Kilns and rotary vessel dryers are common applications for thermography. Single detectors, like the ones used in handheld spot radiometers, can be installed inside an electrical panel to monitor the temperature of a single connection. There are even systems that can continuously monitor the condition of lubricants. Viscosity, water content, ferrous content and particle count can all be automatically measured and reported.
With any system, a positive business case is required to make it a good idea. Consider things such as installation cost and ongoing maintenance costs along with the initial purchase price when deciding if a continuous monitoring system is right for you. Just because you can outfit every point on every machine with a continuous monitoring system doesn't mean that you should.
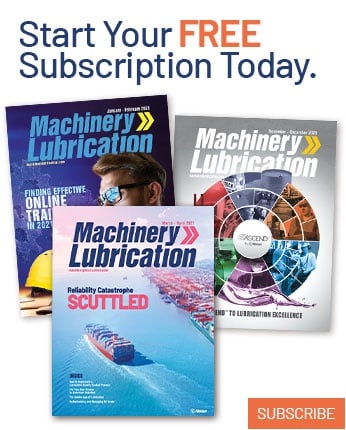