Yarn producer Beaver Manufacturing had several HVAC challenges in retrofitting an existing 40,000-square-foot plant to expand its production facilities in Mansfield, Ga.
More than 170 one-horsepower motors required in the yarn production generate indoor temperatures surpassing 100 degrees Fahrenheit that are both detrimental to employee air comfort as well as machinery efficacy and longevity. Hot summer days can send indoor temperatures soaring past the 115 F mark.
Air conditioning solves the extreme heat problem; however, the huge 25,000-cfm air volume requirements combined with the facility’s low 12-foot ceilings would ordinarily locate supply ductwork too close to spinning yarn, which is manufactured for use as reinforcement in rubber hoses. Ventilation drafts are problematic for this sensitive process because yarn can easily be blown off its spindles.
Design/build mechanical contractor Air Conditioning Specialist (ACS) of Covington, Ga., suggested fabric duct because it has linear vents that disperse the air in a significantly more even and gentle manner than the inherently higher drafts of metal duct with registers every 10 feet. ACS also had success with fabric duct in previous projects that consisted mainly of indoor swimming pool natatoriums.
“We’ve used metal duct at our other facilities, but the low ceiling in Mansfield had us scrambling for a solution,” said Danny Peppers, manufacturing manager, Beaver Manufacturing. “The linear vents of fabric duct provided the gentle air dispersion we needed to keep the yarn spinning on track, but we were surprised that installation labor was significantly cheaper than conventional metal duct.”
Fabric duct can be custom manufactured in a variety of vent sizes, placements and quantities that can be combined with many different fabric porosities for the ultimate in even air flow, according to industry-generated laboratory smoke tests.
With the assistance of manufacturer’s representative Tom Barrow Company of Atlanta, ACS vice president Patrick Hayes specified Verona commercial fabric duct by fabric duct manufacturer DuctSox of Dubuque, Iowa. Hayes specified the Verona with Comfort-Flow, which allows approximately 15 percent of the air to flow through the fabric while the remainder is dispersed through laser-sewn L-Vents.
Hayes’ calculations were based on heat load measurements taken from similar manufacturing lines at other Beaver plants and DuctSox’s factory engineering assistance.
Supplying the ductwork is two 125-ton and one 30-ton McQuay rooftop dx units mounted on an exterior ground-level pad. Hayes supplied metal ducts from each unit through the wall to a tee that feeds a 32-inch truck line running nearly the width of the building. Each of the six 18-inch branch lines that run perpendicular across the multiple yarn production lines are suspended with a cable system.
Installation labor was reduced by more than 20 percent. Metal duct would have taken two or more weeks to install; however, Hayes’ four-man crew took three days to install the cable runs and just four hours to physically hang the DuctSox. The HVAC installation’s speed helped Beaver fast-track the project.
After installation, Atlanta Test & Balance of Alpharetta, Ga., was subcontracted to adjust the airflow. For example, turbulence was eliminated in several duct runs with DuctSox’s proprietary Air Flow Device (AFD), an internal air flow adjuster that’s quickly zippered into a duct run with easy access for future calibrations.
Other fabric duct benefits – it doesn’t attract condensation or dust because air flows through the fabric – will also keep moisture and dirt from collecting and falling on yarn production processes.
ACS’s design has performed flawlessly in keeping Beaver’s production process cool as well as on-line. More importantly, employees have a cool and comfortable workplace.
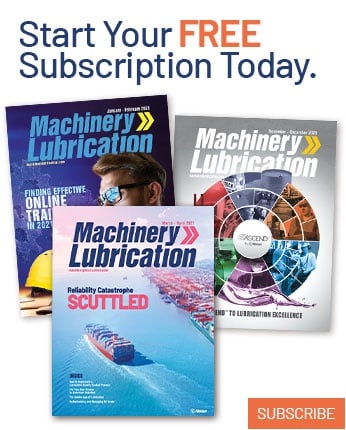